Along with stone and clay, wood was one of the first materials worked by early humans. Microwear analysis of the Mousterian stone tools used by the Neanderthals show that many were used to work wood. With the advances in modern technology and the demands of industry, woodwork as a field has changed. Skilled fine woodworking, however, remains a craft pursued by many, and many artisans are in constant search of new, bespoke techniques of working with this material.
Eindhoven-based designer and Design Academy Eindhoven graduate Sho Ota started his practice as a wooden furniture manufacturer in Japan where he worked as a designer and a prototype maker. After he moved to the Netherlands, he established his own design studio aiming to explore the structure of wood that couldn’t be achieved through mass production.
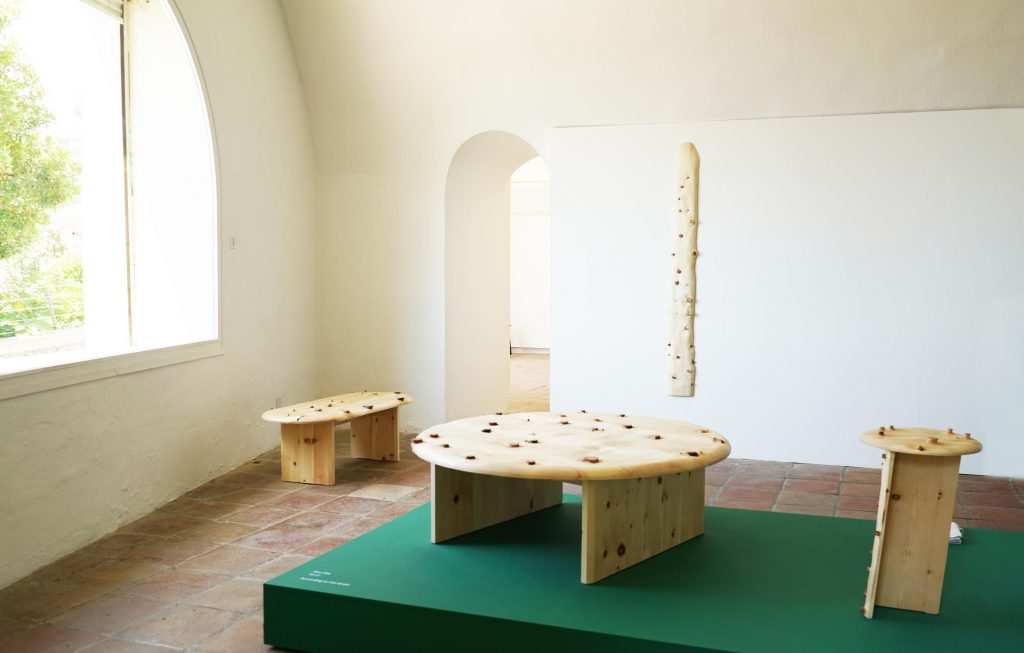
Knot series by Sho Ota (also header image)
Normally, mass production creates flat surfaces out of wood, cancelling any imperfection and trying to make each surface as similar as the other one. Rather than polish the wood, Ota focuses on the identity of the material and carefully chisels each knot, revealing textures and highlighting the quality of wood grain.
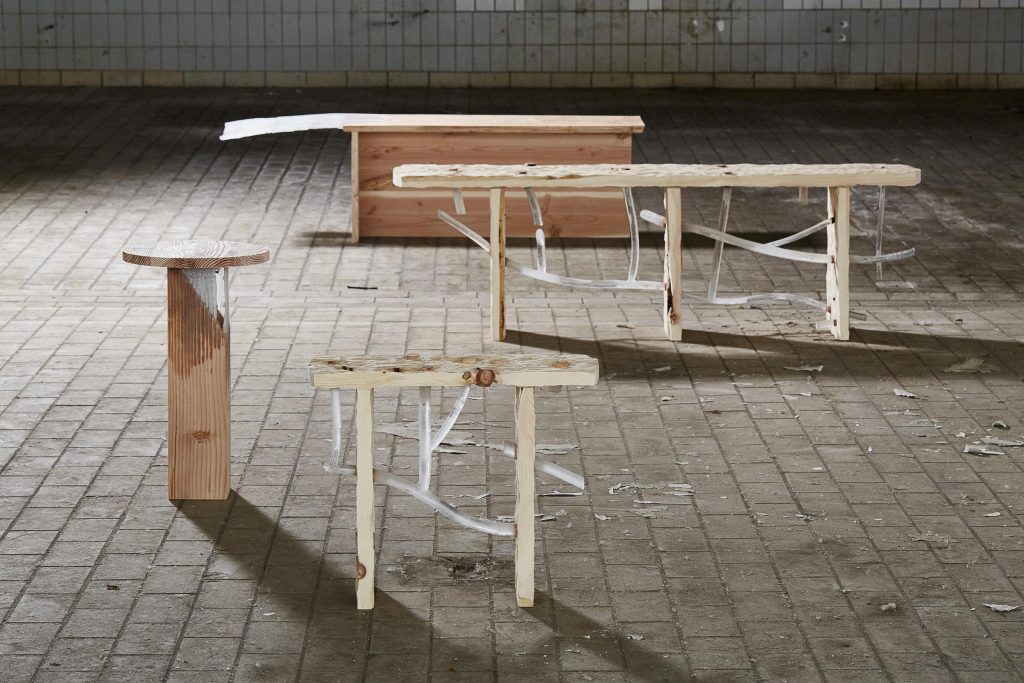
Surfaced series by Sho Ota
In his Surfaced series, which includes chairs, benches, shelves, trays, and a coat rack, every item is constructed from an assembly of wooden elements of different sections, most of which are considered waste material. The designer takes the pieces, glues them together and then carves them, resulting in new sculptural pieces, that are both striking and functional.
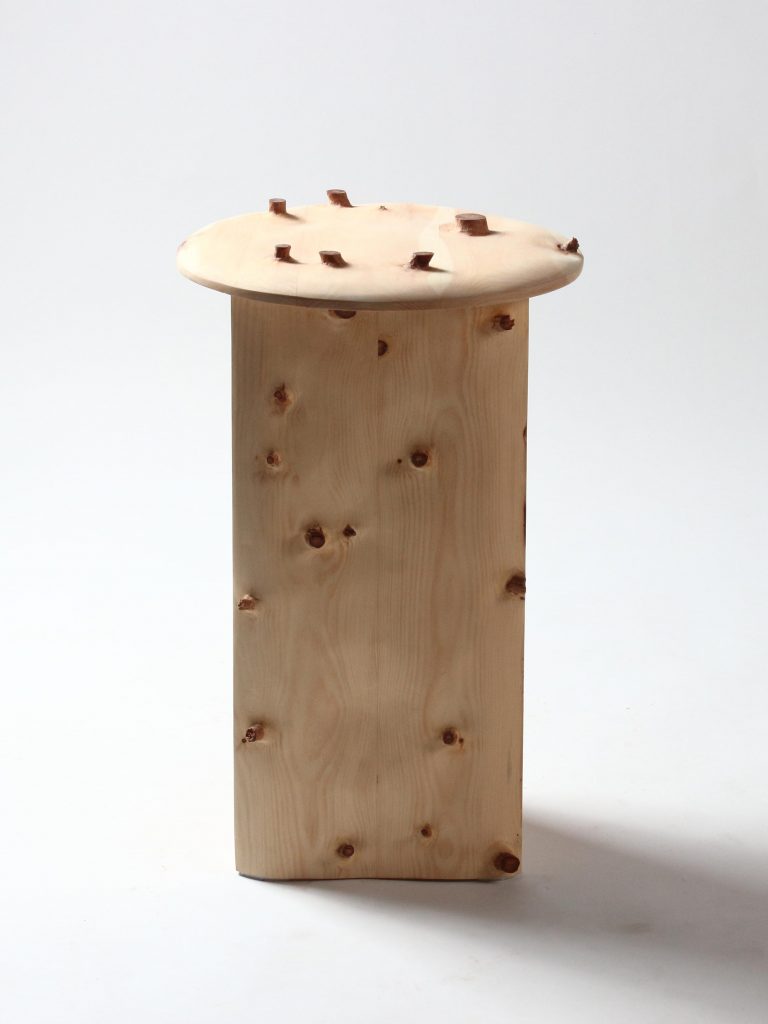
Knot series by Sho Ota
The Surfaced series was followed by the Knot series, where the woodworker chisels down the knots found on wood, bringing out their three-dimensionality and texture. In some cases, the designer connects the knots using epoxy resin, recreating the branches and making sure every object is truly unique.
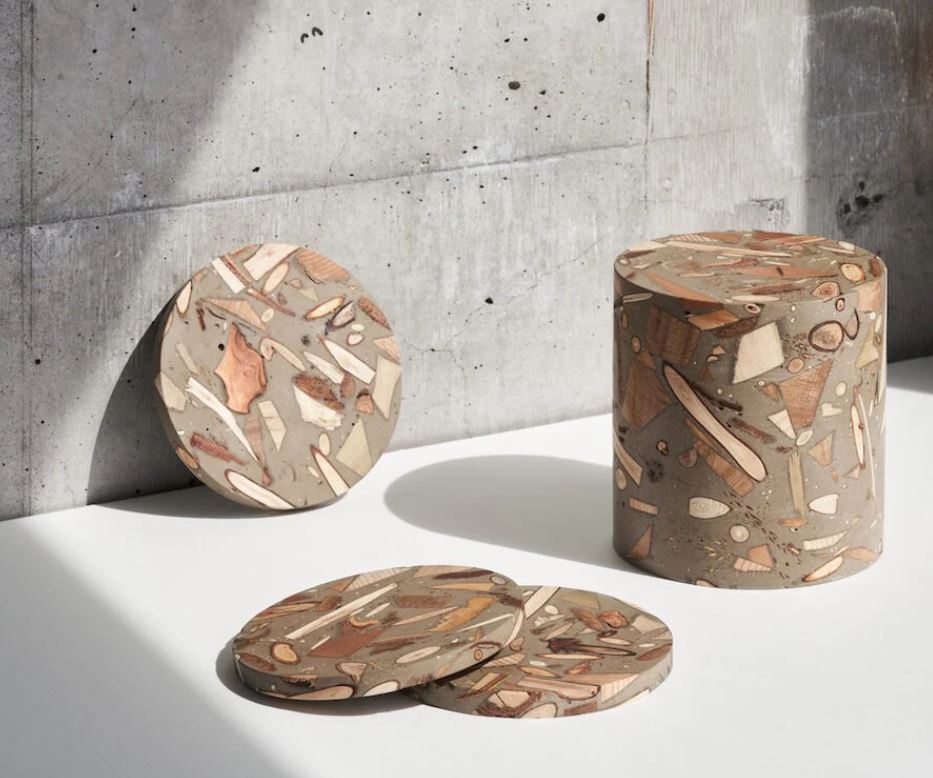
ForestBank by Yuma Kano
Another Japanese designer, Yuma Kano, works with forest debris normally considered ‘worthless’ for furniture construction. Mixing small trees, leaves, bark, seeds, and soil, with a reactive mineral base and a water-based acrylic resin that contains no organic solvents, the designer has created ForestBank, a new type of wood with unique patterns that vary depending on the season telling a unique story. The material can be shaped by using normal woodworking methods and applied in various fields like furniture construction and interior design.
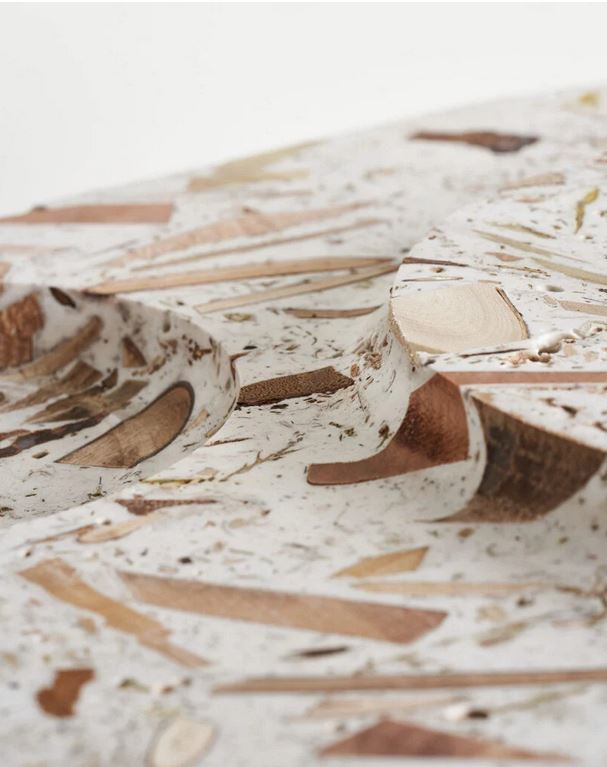
ForestBank by Yuma Kano
As its title suggests, the new material explores opportunities around forests and seeks to determine their full value. Different colours of the pattern reflect the characteristics of the harvest site. The yellows and greens are the actual colouring of the trees, which are dyed by bacteria found in nature. The green leaves mixed in change to orange and brown as the seasons change. In addition, soil from the forest floor can be mixed in, adding shades of brown and black, while of cross-sections of roots and seeds hidden in it result in complex patterns of the material.
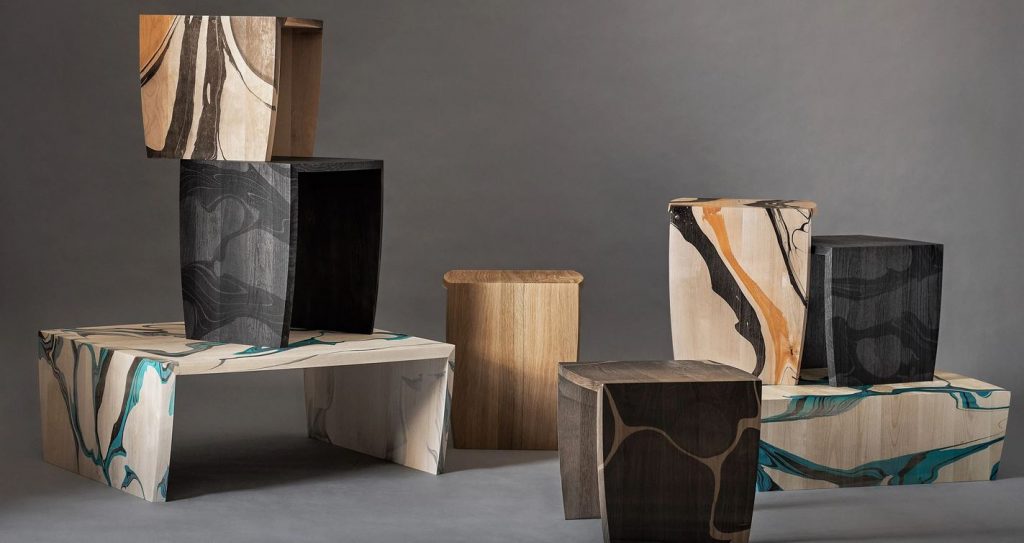
Suminagashi marbling technique by Ringvide
Seeking unusual colouring methods for their pieces, Swedish furniture producer Ringvide has developed a way to imprint swirling patterns on wooden tables using suminagashi, the traditional Japanese marbling technique normally used on paper.
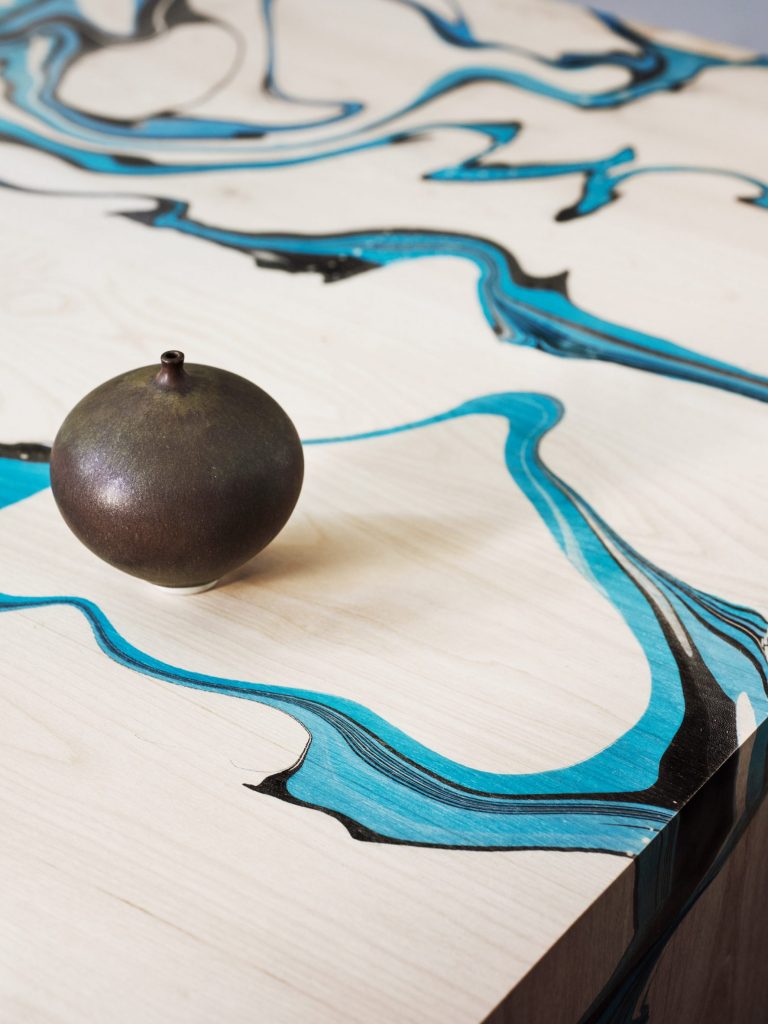
Suminagashi marbling technique by Ringvide
When a drop of ink is gently put onto a water surface the difference in surface tension spreads the ink over the surface. When this is done repeatedly, the colour eventually covers the whole surface. Varying the way the colour is applied to the surface together with different means of disrupting the surface creates different patterns, some more easily controlled than others.
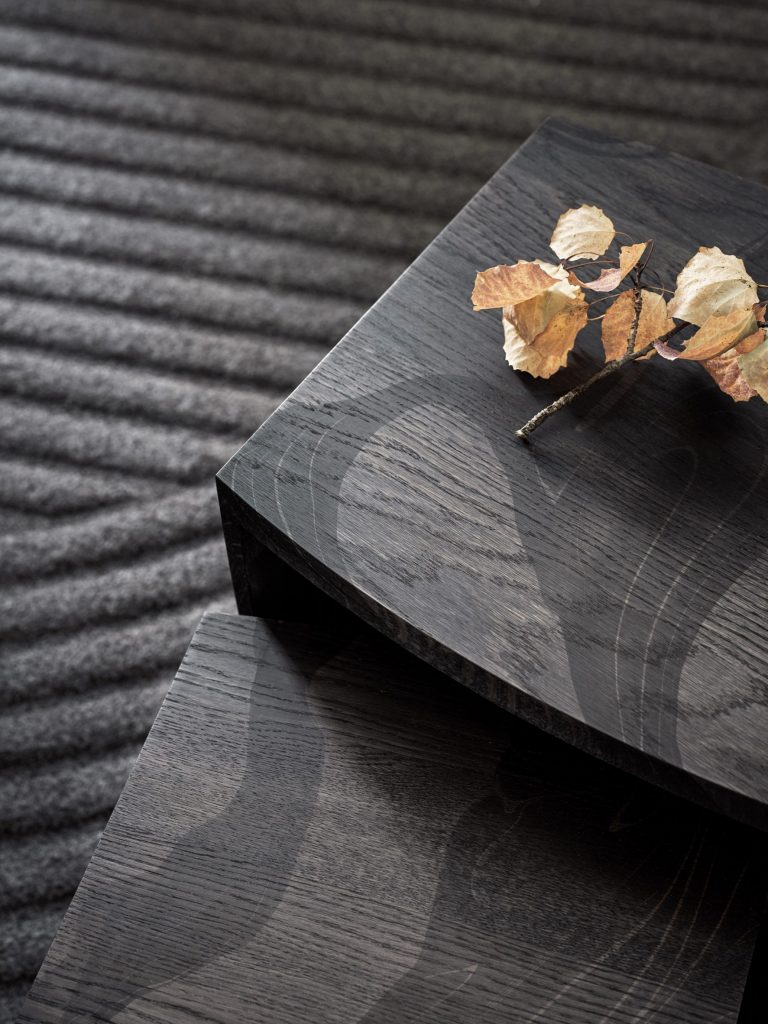
Suminagashi marbling technique by Ringvide
To create the designs, the studio adds water-based ink into the water that has been previously mixed with Carrageena, a biopolymer extracted from algae, to make it thicker and easier to create shapes. Then the fully-assembled birch tables is dipped into the water to ensure that the pattern wrapped around its corners and sides. The acrylic binding in the ink that makes colour stick to the surface of the furniture, creating patterns that vary from piece to piece.