If we could appreciate and cherish things we already have, that could be a strong starting point for solving many environmental issues. These chair designs crafted from reclaimed and leftover materials and discarded objects are driven by the aspiration to make a positive societal and ecological impact. And they are as eye-catching as they are sustainable.
To create its Welsh Mountain Hembury Chair UK-based company Solidwool uses an innovative fibreglass-like composite made from local wool of low market value as reinforcement and bio-resin as a binder.
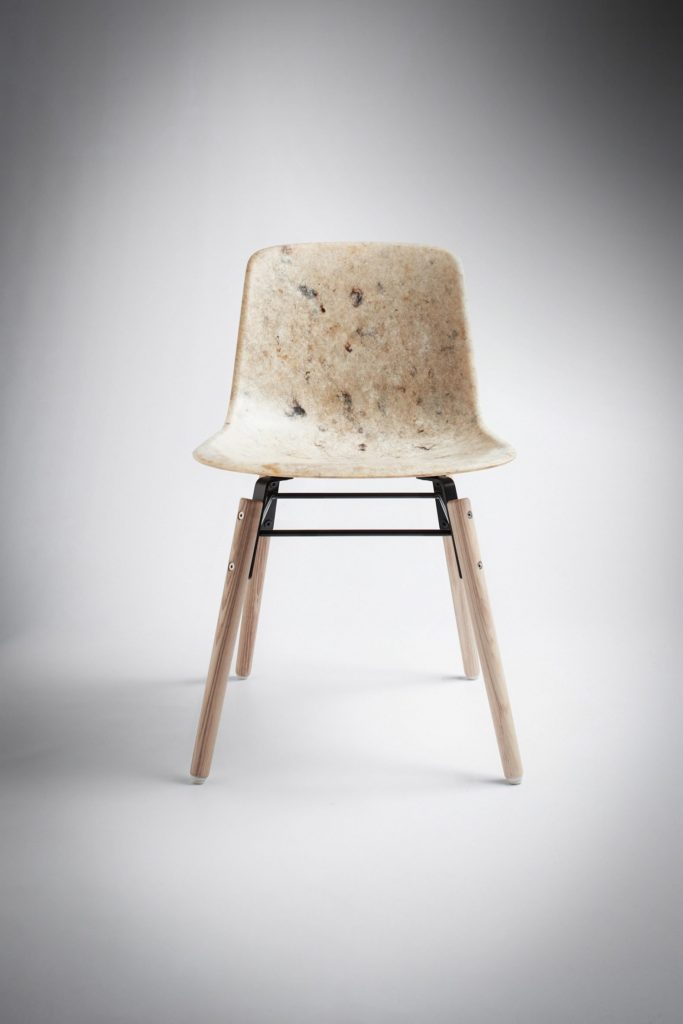
Welsh Mountain Hembury Chair by Solidwool (also header image)
The team aims to make Solidwool the most natural, lowest impact and highest quality wool composite material available, which would serve as a sustainable alternative to today’s petrochemical based structural reinforced plastics. At the same time, they seek to create a beautiful natural material with a story that connects people to the land it has come from and helps keep local traditional skills and craftsmanship alive.
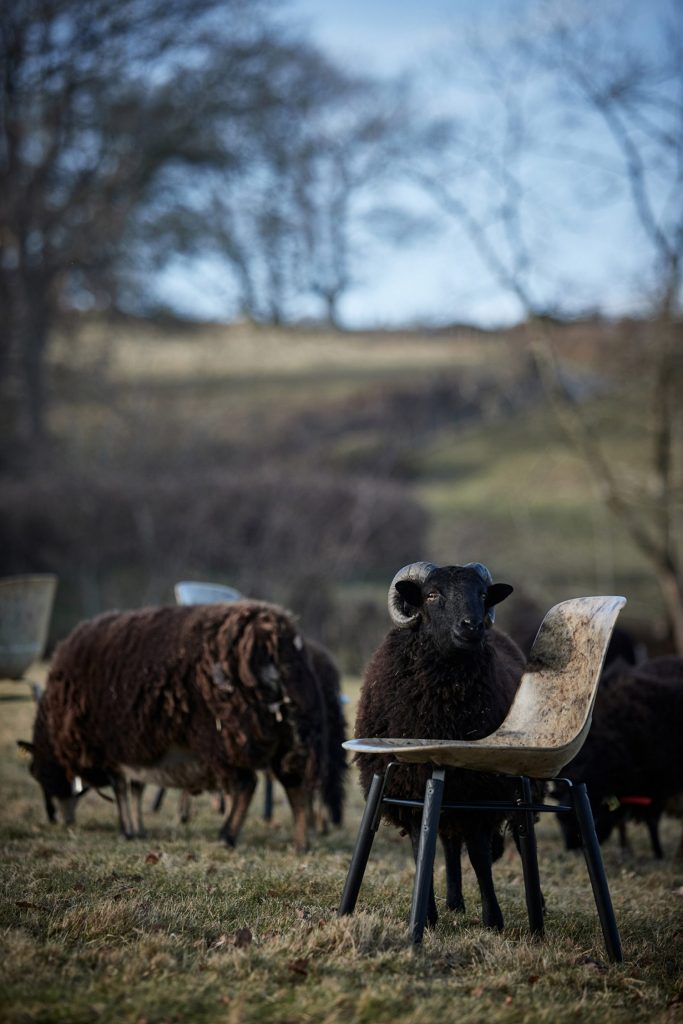
Welsh Mountain Hembury Chair by Solidwool
The chair’s principle material comes from traditional sheep breeds, such as Herdwick and Welsh Mountain. Both are bred for its meat as opposed to its fleece, which is too coarse to spin into wool for knitting and too difficult to dye and is subsequently often disposed of.
Using this close-textured wool from both the white and black Welsh Mountain sheep, the multicoloured white, grey-brown and black kemp reveals a distinctive veining throughout the composite. This creates a striking marbled effect, showcasing the unique layering of textures and tones found in this incredible wool.
Besides, by using traditional British breeds Solidwool supports local farms and reduces the carbon footprint of the product.
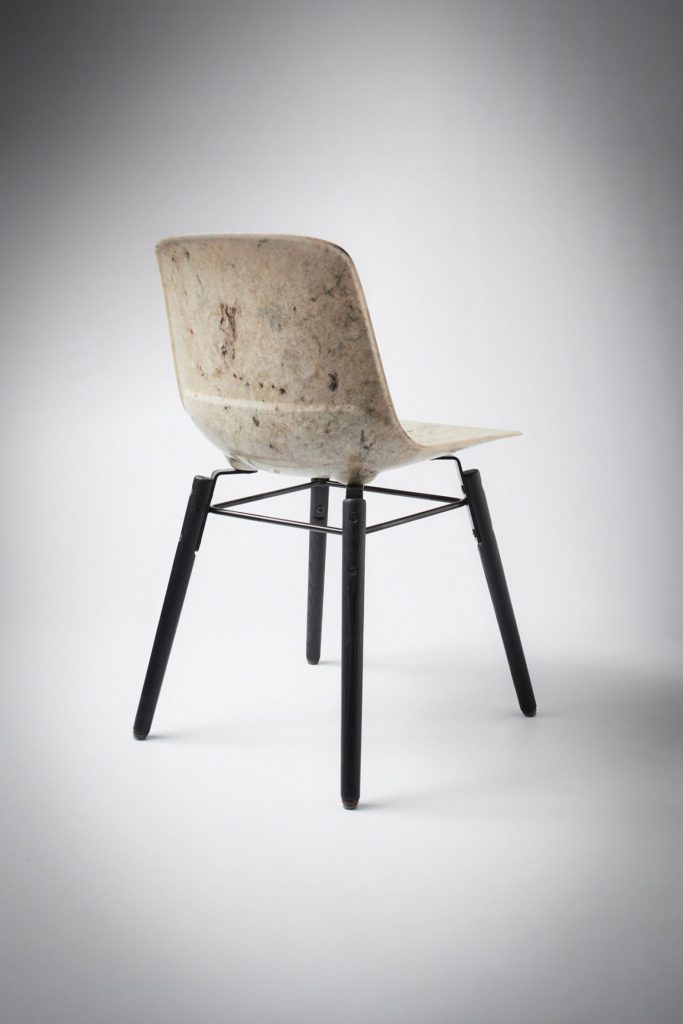
Welsh Mountain Hembury Chair by Solidwool
In order to make the composite, the team combines the wool with bio-resin with a 50% bio-based renewable content in a specially developed manufacturing process. Sourced from waste streams of other industrial processes, such as wood pulp and bio-fuels production, the sustainable resins allow for strong and durable composites with a lower environmental impact.
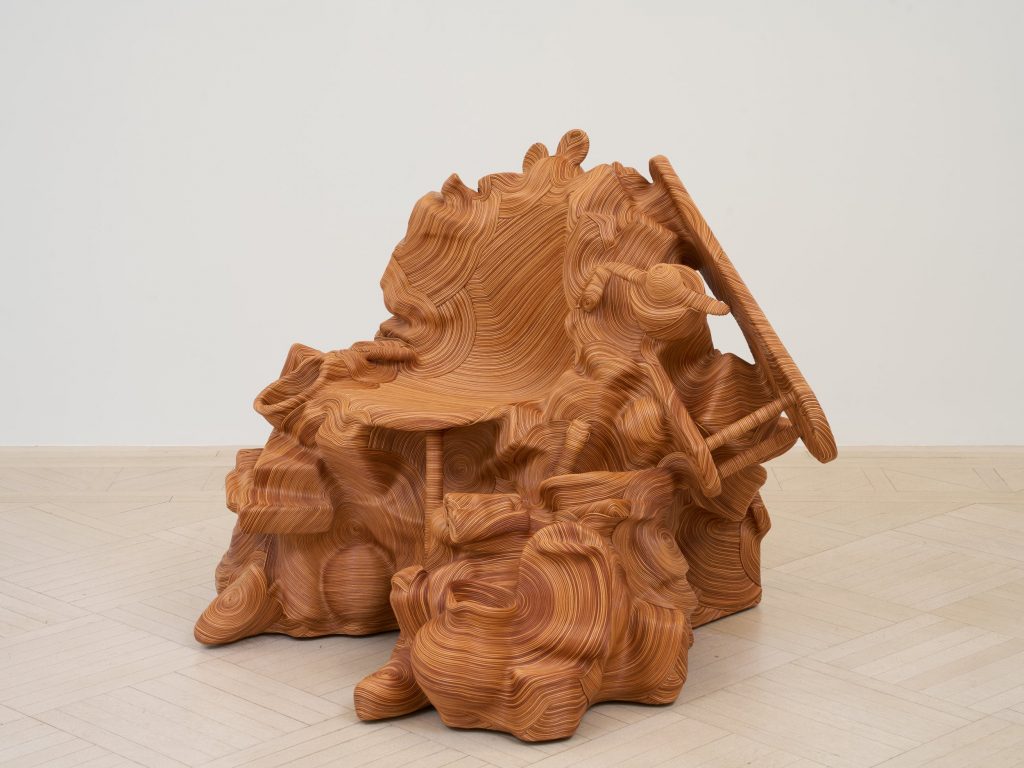
Salvage Chair by Jay Sae Jung Oh
Seattle-based and Korea-born designer Jay Sae Jung Oh creates chairs made from discarded household objects encased in leather as a commentary on waste culture. For the Salvage Chair, the designer has combined thrown-away instruments – including a drum, drumsticks, a French horn and an electric guitar – into an armchair-like arrangement before hand-wrapping the entire form in ribbons of thin brown leather.
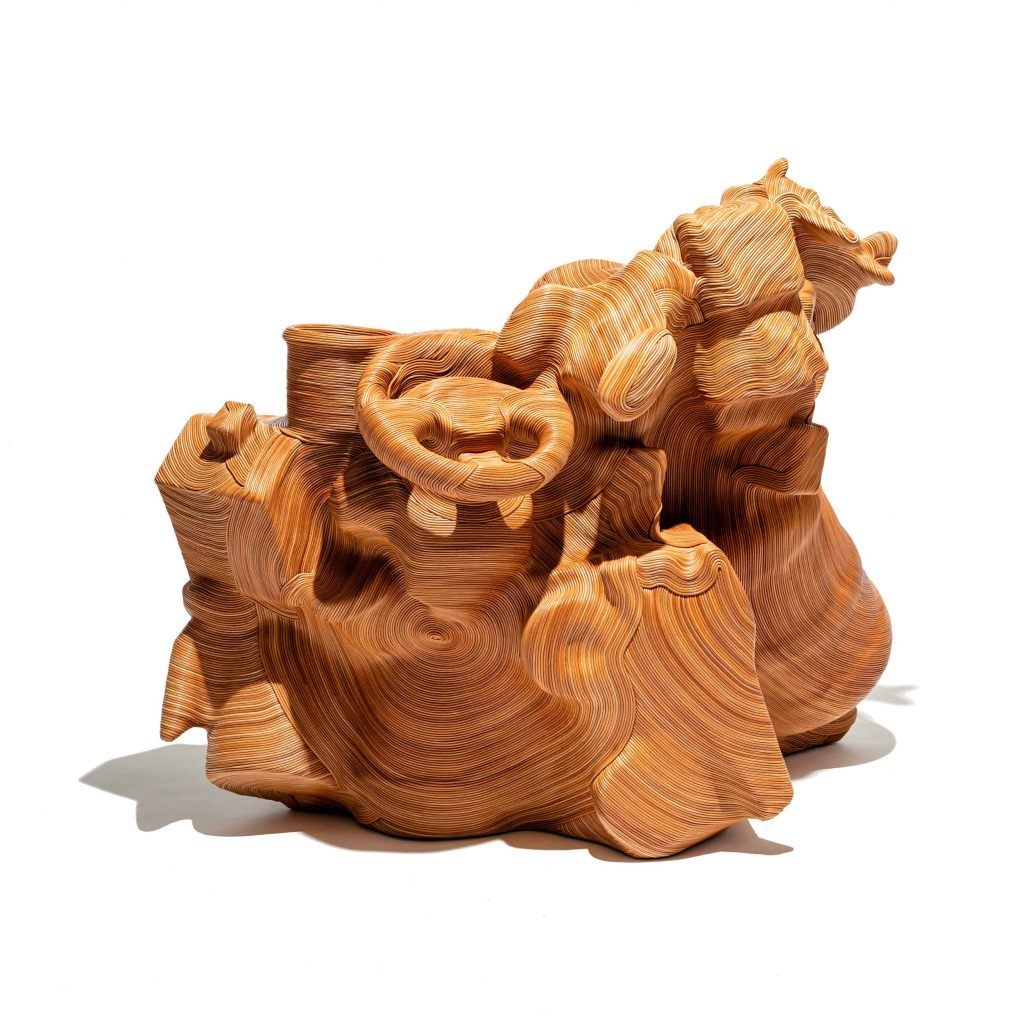
Salvage Chair by Jay Sae Jung Oh
Conceived from the awareness of social issues like sustainability and abundant waste, her ongoing Salvage series includes various household furniture including a stool, wall organizer and a large sculptural planter made of a shovel, watering can and planting pots.
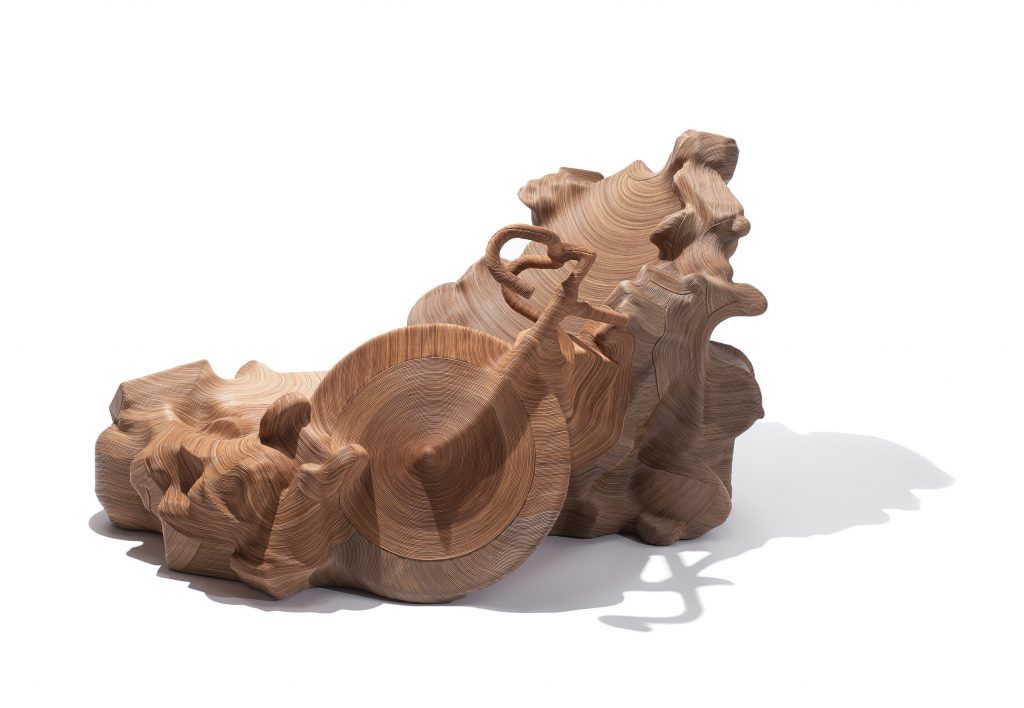
Salvage Chair by Jay Sae Jung Oh
The production process takes place in several stages. First, the designer sources various leftover or damaged objects from thrift store outlets, as well as from friends or neighbours. After meticulously designing the overall form, the collected pieces are assembled into a furniture-like structure. Once the form is completed, Oh designs intricate patterns on its surface and then proceeds to wrap it in leather. The designer was surprised how easy it is to collect objects. In her opinion, the ease of this process “highlights just how much stuff we throw away in our daily lives.”
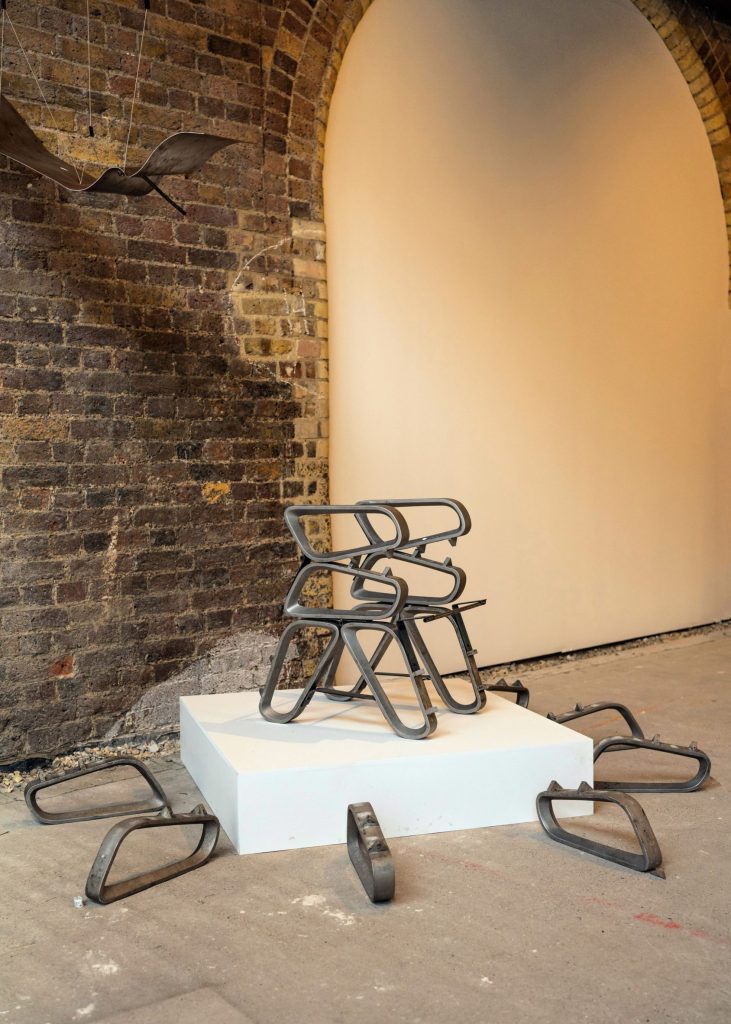
Aluminium chair by Sara Afonso Sternberg
12 London-based designers, bothe established and emerging, presented their 1:1 scale prototypes of chairs, as well as chairs that are still works in progress, as part of Prototype/In Process, an exhibition of seating presented by virtual magazine Chair of Virtue during London Design Festival.
Sara Afonso Sternberg unveiled sculptural aluminium seating made of armrests salvaged from the middle of public benches in Camberwell parks. Originally, the armrests were supposed to make it difficult for homeless people to sleep or rest on the benches. In this project, however, they were given a new form and use, inviting the public to critically engage with control mechanisms such as hostile architecture.
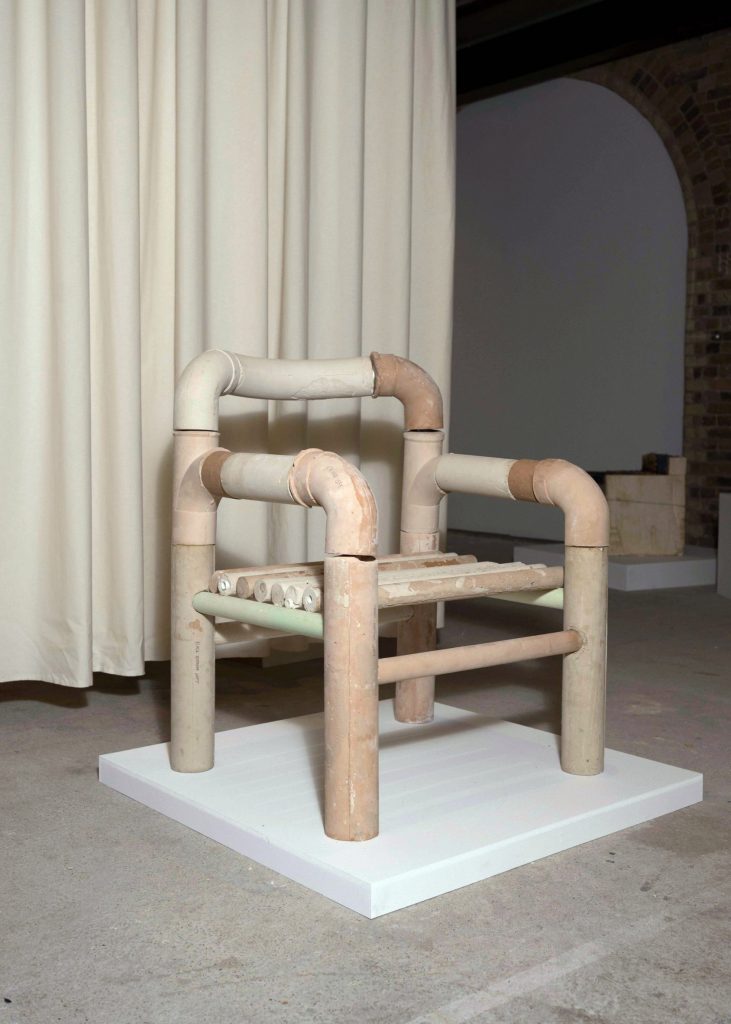
Chair from salvaged construction materials by Louis Gibson
Louis Gibson experimented with unconventional use of construction stock materials. Wishing to address the problem of reassembly, he created casts from disused pipes. the designer chose plaster for the purpose of quick setting, he also felt it was in keeping with the world of builders’ merchants stock supplies.