These alternative bricks projects demonstrate how design and construction industry can come together to address the climate crisis in a meaningful way. All of them use different kinds of waste to create durable products that has the potential to replace conventional bricks.
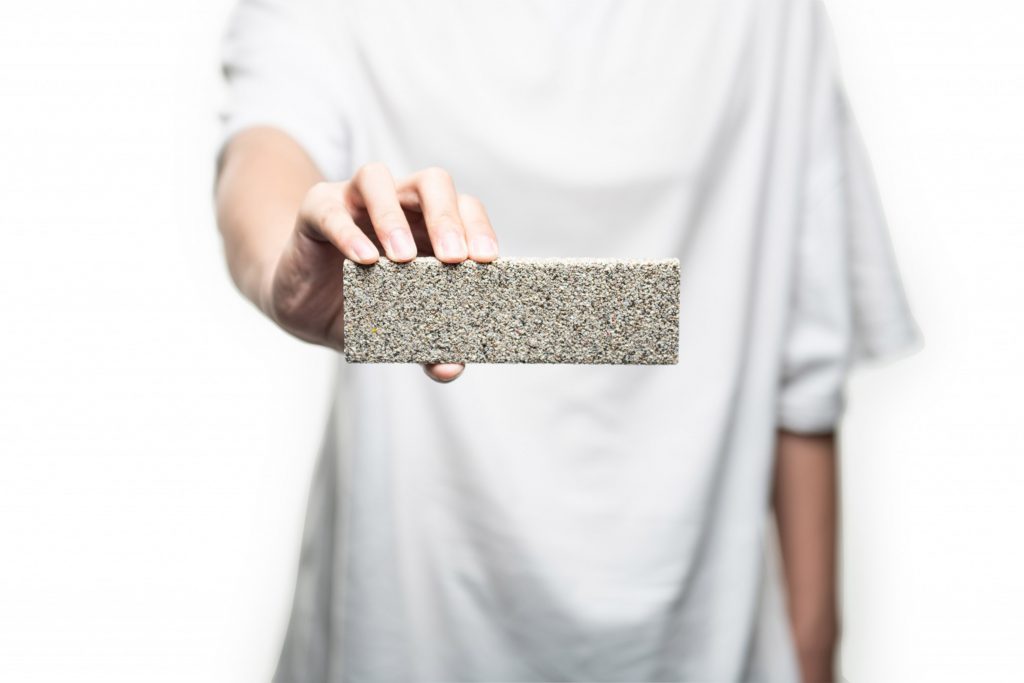
Permeable YiBrick by Yi Design (also header image)
According to the Chinese materials company Yi Design, established by curator and artist Caroline Cheng and designer Karl Yin, China produces approximately 18 million tonnes of ceramic waste each year, the majority of which is dumped or buried illegally. Aiming to address the problem of this enormous volume of waste, the team has developed a porous brick that could be used to prevent flooding in urban areas. The Permeable YiBrick is made from to 97 per cent recycled ceramic waste sourced from industrial porcelain manufacturers in the city of Jingdezhen, which is known as the ceramics capital of China.
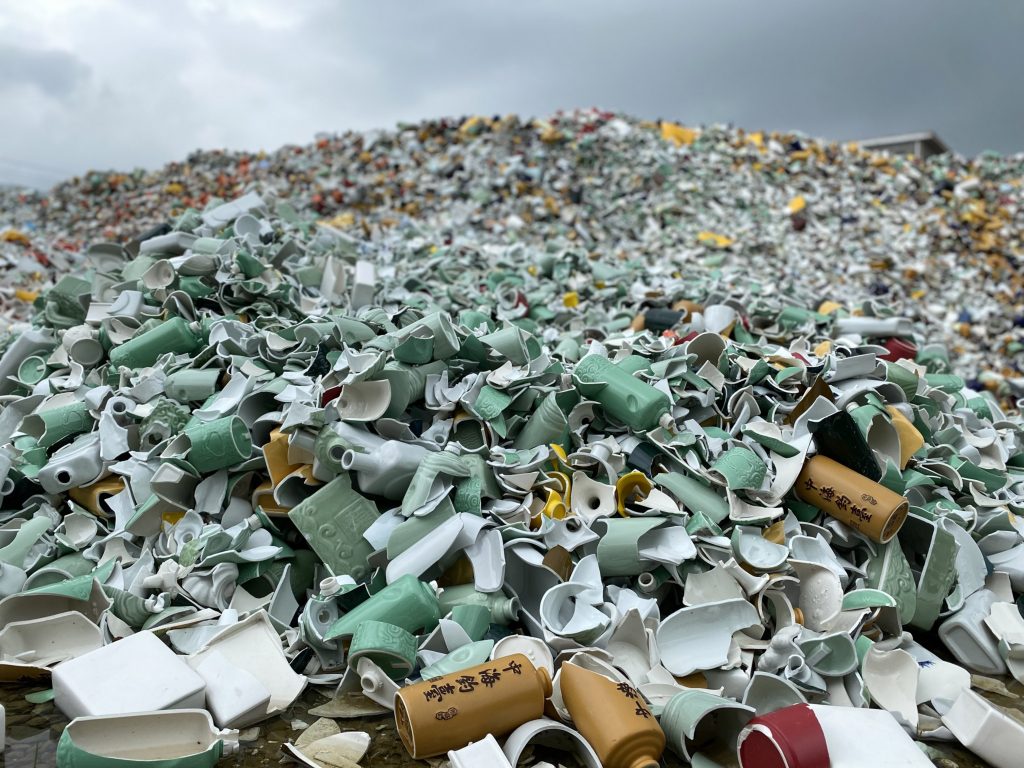
Permeable YiBrick by Yi Design
Yi Design grinds and binds the collected waste together using a specially developed non-organic chemical binder, which the company claims is free from plastics and cement.The resulting material is highly porous and robust, which allows to use it as a more absorbent alternative to conventional cement bricks in various architectural contexts.
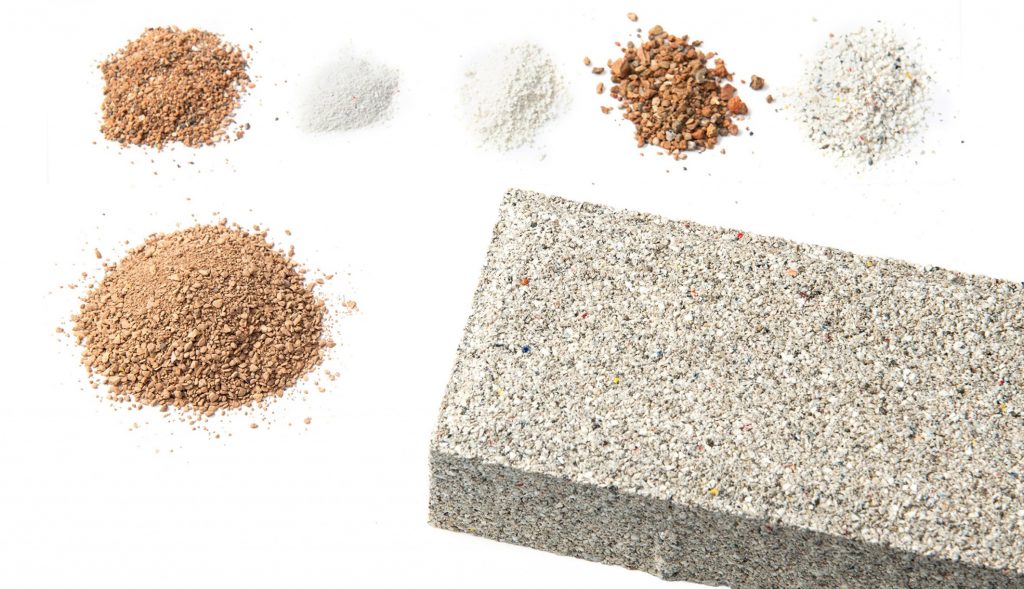
Permeable YiBrick by Yi Design
The brick can harvest rainwater, redirecting it from the sewage system to the water table by permeating through the ground. It can be utilized for sponge cities – urban spaces that retain stormwater before gradually filtering and releasing it, – for outdoor use in paving areas and gardens, or as a base of water fountains.
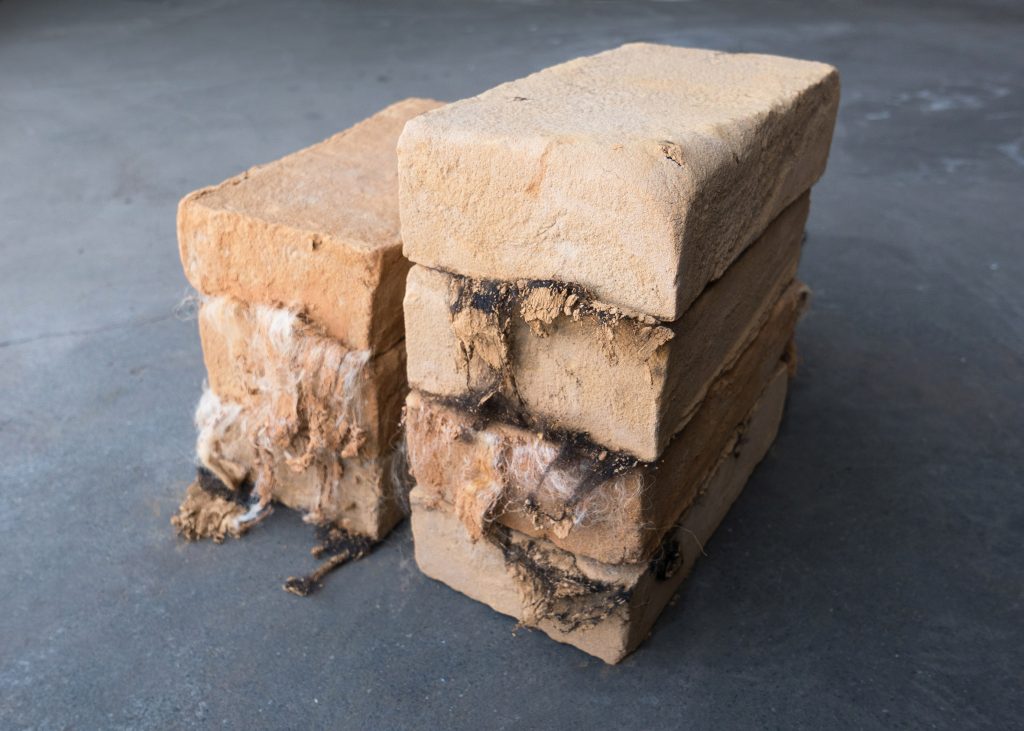
Building The Local by Ellie Birkhead
As part of her final project on the Social Design masters programme, Design Academy Eindhoven graduate Ellie Birkhead has developed a process of brick making that incorporates mixing clay with local waste products including hair from a hairdresser, horse manure, glass bottles, wool and straw ash from a farm, and used grain from a brewery.
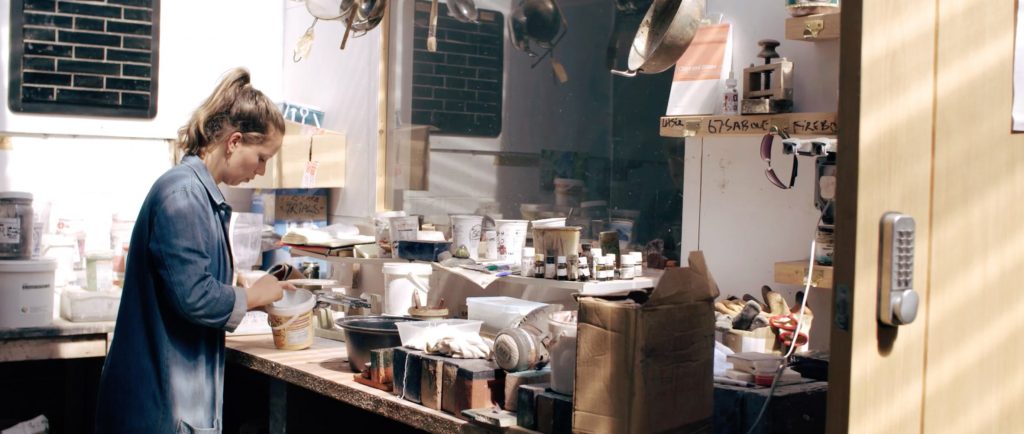
Building The Local by Ellie Birkhead
All waste is sourced from the Chiltern Hills, UK, once home to more than 100 brick-making businesses, all of which are now closed due to the importation of cheaper products from abroad and elsewhere in the UK. ith her project, Birkhead, who is originally from Buckinghamshire, aims to create new connections that might help sustain the brick-making industry in the area.

Building The Local by Ellie Birkhead
Called Building The Local, the project comprises six types of bricks depending on the material used for their production. The hair is used to make an unfired brick known as a stock, which is normally produced using straw. The wool and horse manure bricks are made in a similar way. The straw ash brick is fired, the straw changing the final colour of the brick. New colours are also achieved via addition of waste glass from local pubs. The brick made using spent grain creates a porous product as the grain burns off during firing.
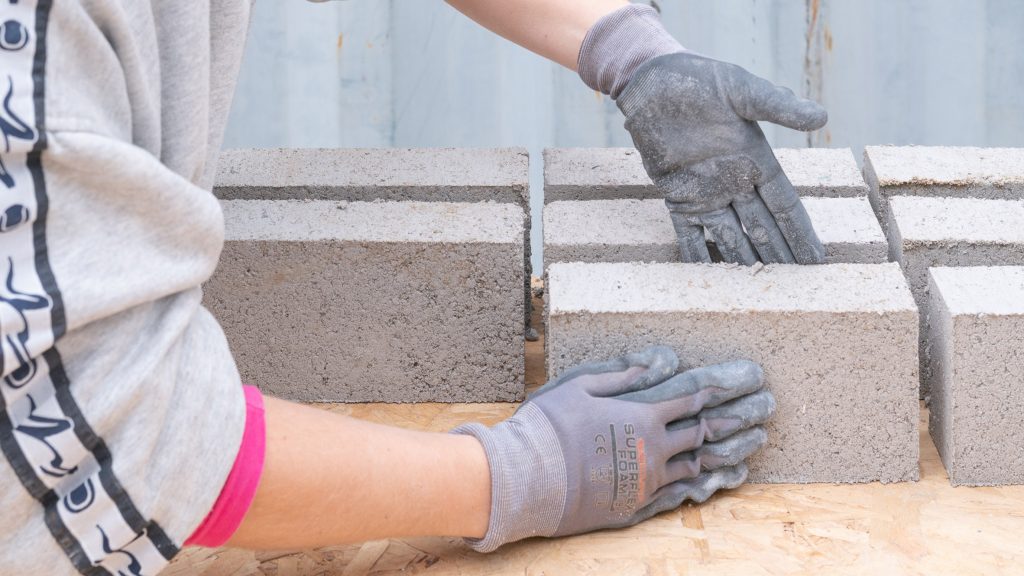
Gent Waste Brick by Carmody Groarke and TRANS Architectuur Stedenbouw
Architecture studios Carmody Groarke and TRANS Architectuur Stedenbouw have teamed up with circular economy specialist Local Works Studio and materials manufacturer BC Materials to similarly develop a brick from local waste – but they opted for construction waste, which was collected from a local recycling centre for demolition concrete and glass.
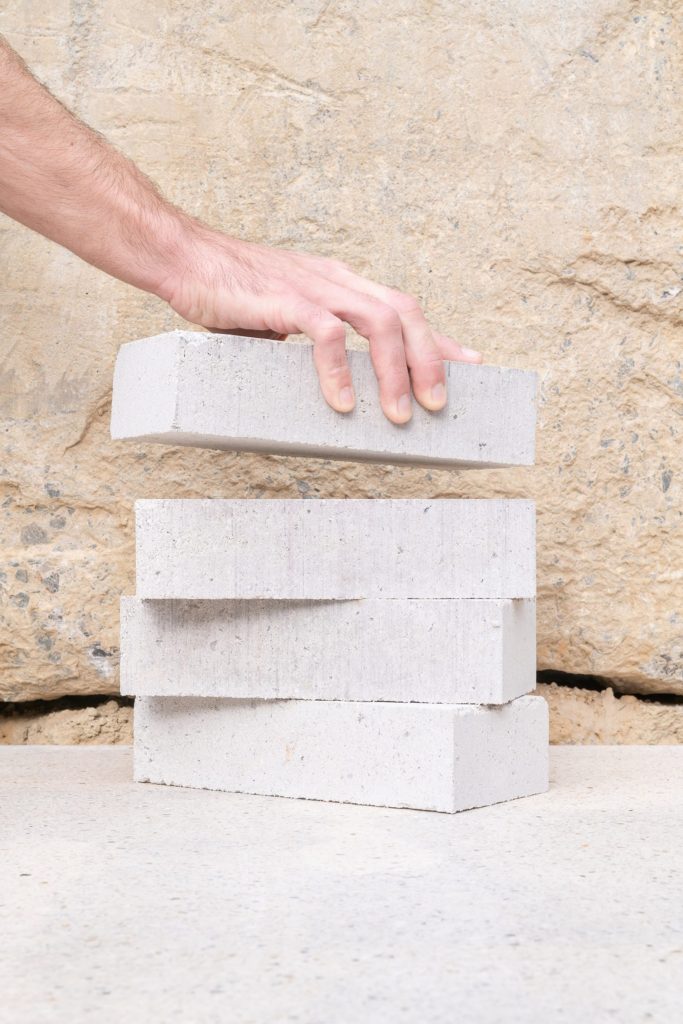
Gent Waste Brick by Carmody Groarke and TRANS Architectuur Stedenbouw
The Gent Waste Brick is made from 63 per cent recycled municipal waste sourced from Ghent, which is mixed with lommelzand sand from the Belgian municipality of Lommel and bound together with hydraulic lime and ground calcium carbonate.
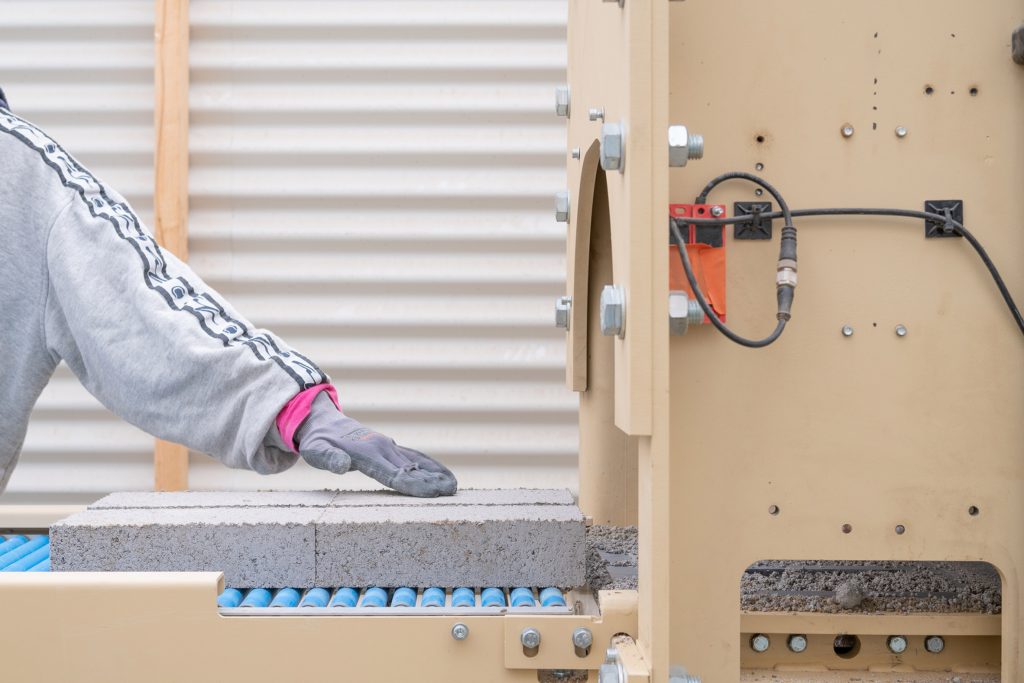
Gent Waste Brick by Carmody Groarke and TRANS Architectuur Stedenbouw
The bricks are cured in a humid setting for two weeks and left to dry naturally instead of being fired. They become robust through a process known as mineral carbonation, which involves the calcium carbonate in the brick reacting with carbon dioxide in the surrounding air. In such a way the resulting material is carrying just 0.17 kilograms of CO2 per kilogram, i.e. one-third of the embodied carbon of a Belgian clay-fired brick.
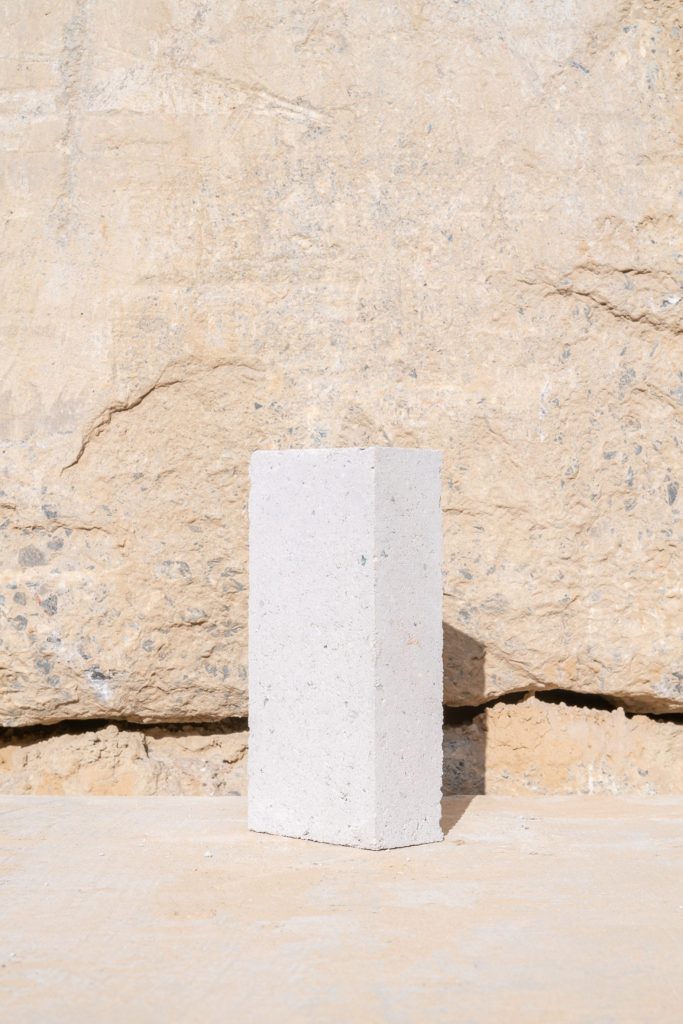
Gent Waste Brick by Carmody Groarke and TRANS Architectuur Stedenbouw
The alternative bricks will be used to build the new wing of the Design Museum Gent, so it has the same pale grey tone as other local civic buildings.