Modern construction techniques exploit raw materials without considering that they are amongst the largest contributors to carbon emissions. In the long run, the amount of waste they produce is frightening. Several materials researchers have come up with ways to improve the brick to make it more environmentally friendly.
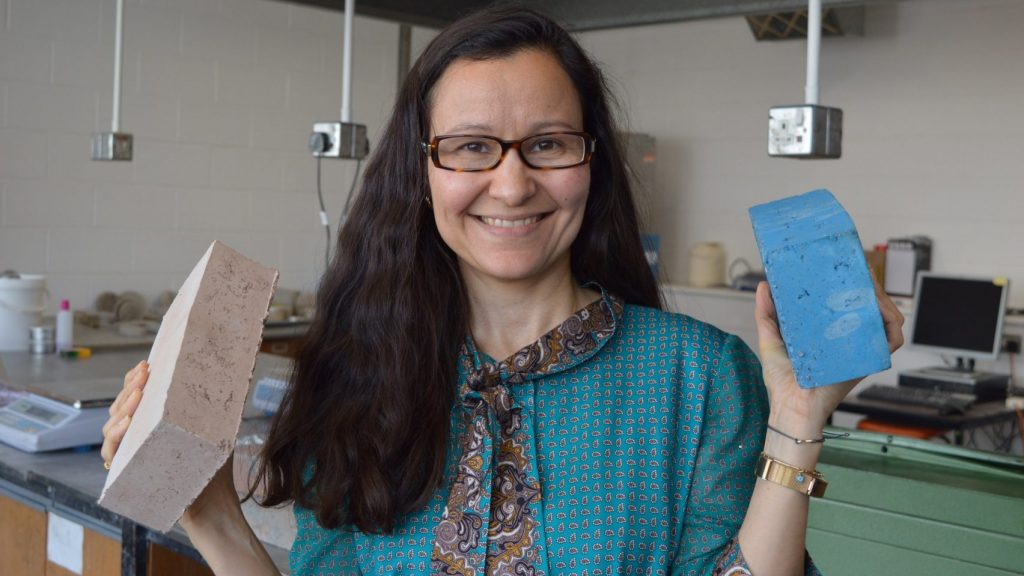
K-Briq by Kenoteq
Driven by the desire to reduce the amount of emissions produced by construction industry, engineering professor Gabriela Medero at Edinburgh’s Heriot-Watt University has invented a more sustainable building brick that generates less than a tenth of the carbon emissions in its manufacture than a regular brick.
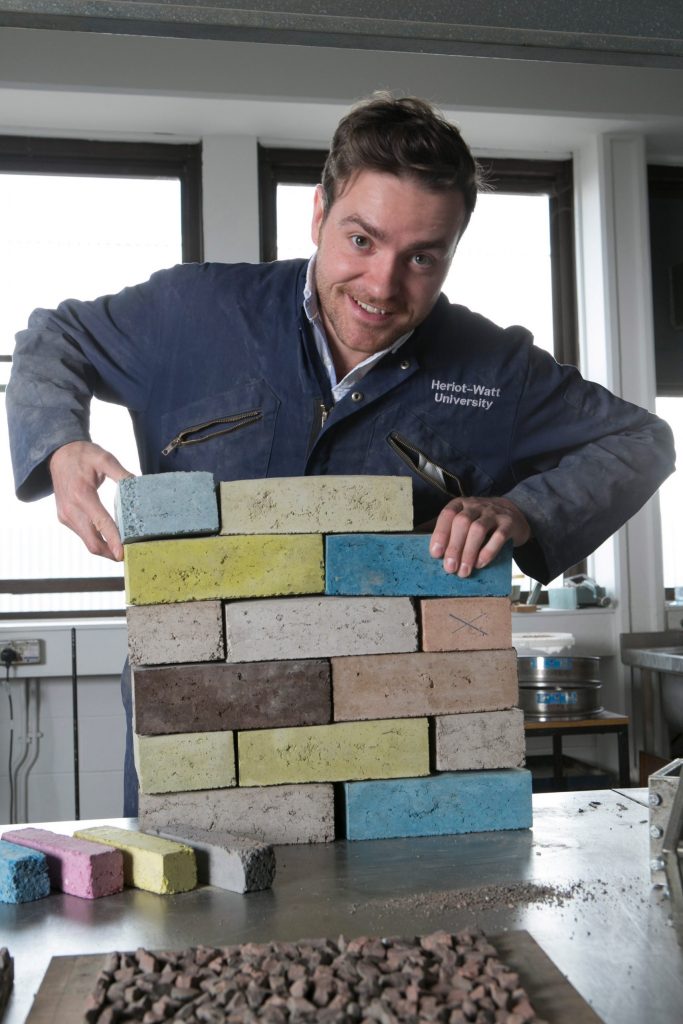
K-Briq by Kenoteq
Named K-Briq, the brick looks and weighs like a conventional brick but is made using 90 per cent construction waste and is unfired to save energy. Medero also claims that the new product offers better insulation properties and can be produced in any colour.
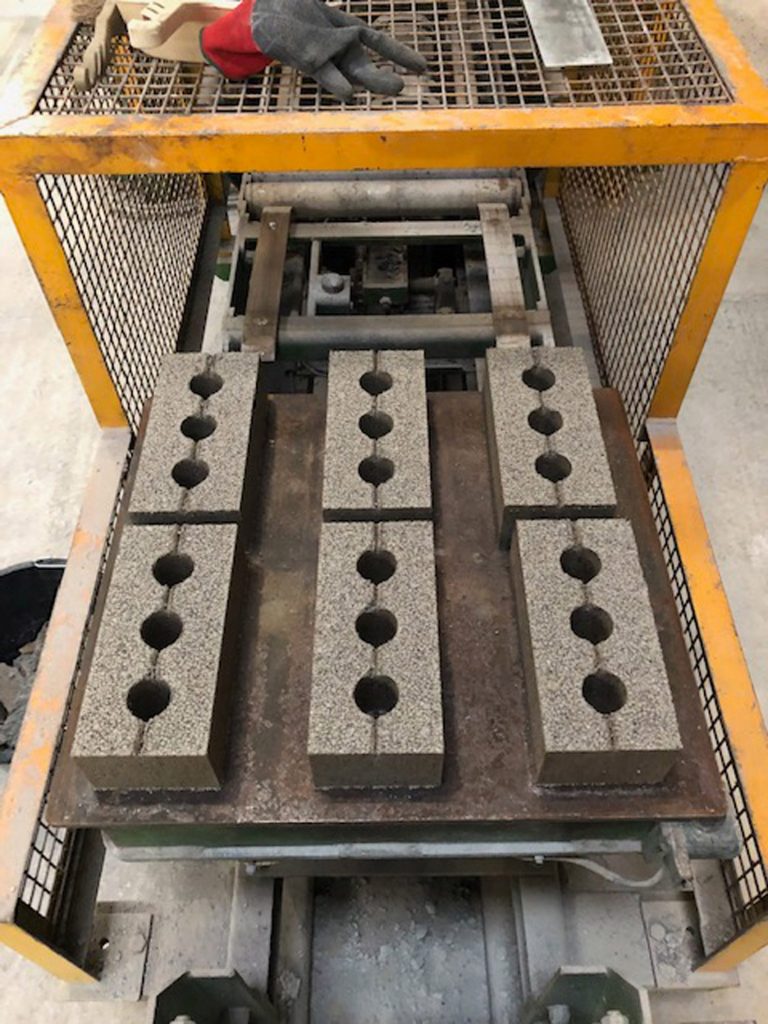
K-Briq by Kenoteq
To put the bricks into commercial production, Medeto co-founded a startup Kenoteq, which is producing its bricks on-site at Hamilton’s Waste and Recycling in Edinburgh, minimising the amount of transport required in the process.
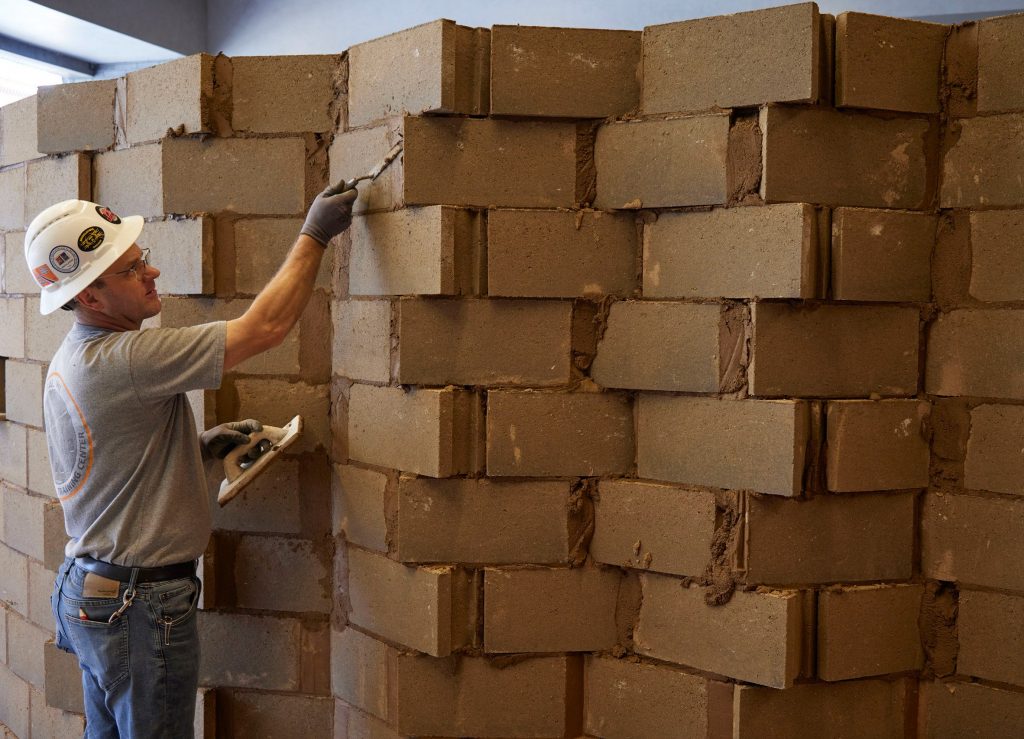
Bio-Block by SOM and Prometheus Materials
Colorado-based material company Prometheus Materials that was established in 2021 by professors at the University of Colorado at Boulder, has developed Bio-Block, a masonry block using micro-algae and aggregate that offers a zero-carbon alternative to standard concrete.
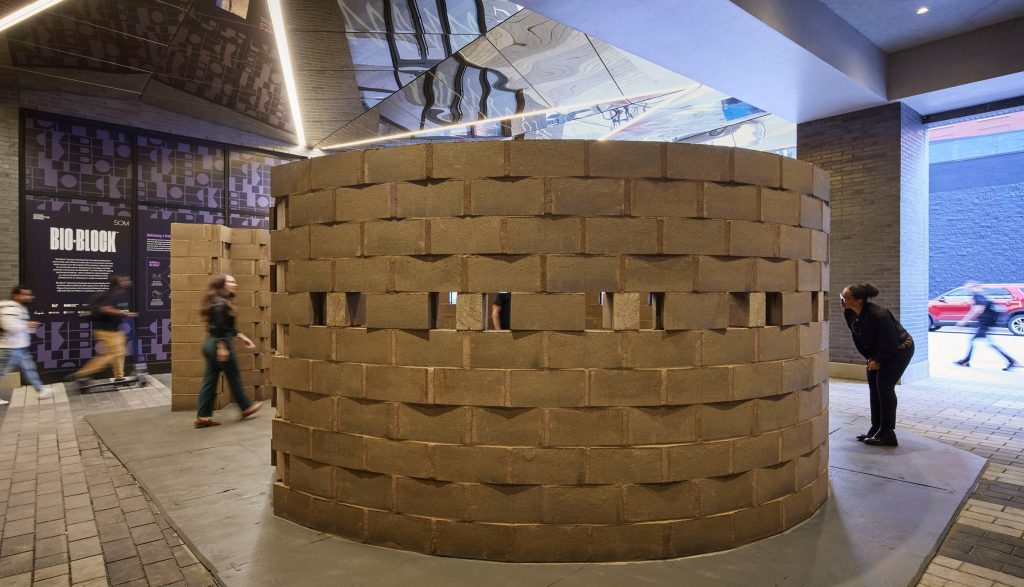
Bio-Block by SOM and Prometheus Materials
The process of the material production eliminates the use of Portland cement, which is the most common type of cement used around the world, which contributes to about 8% of the world’s carbon dioxide emissions.
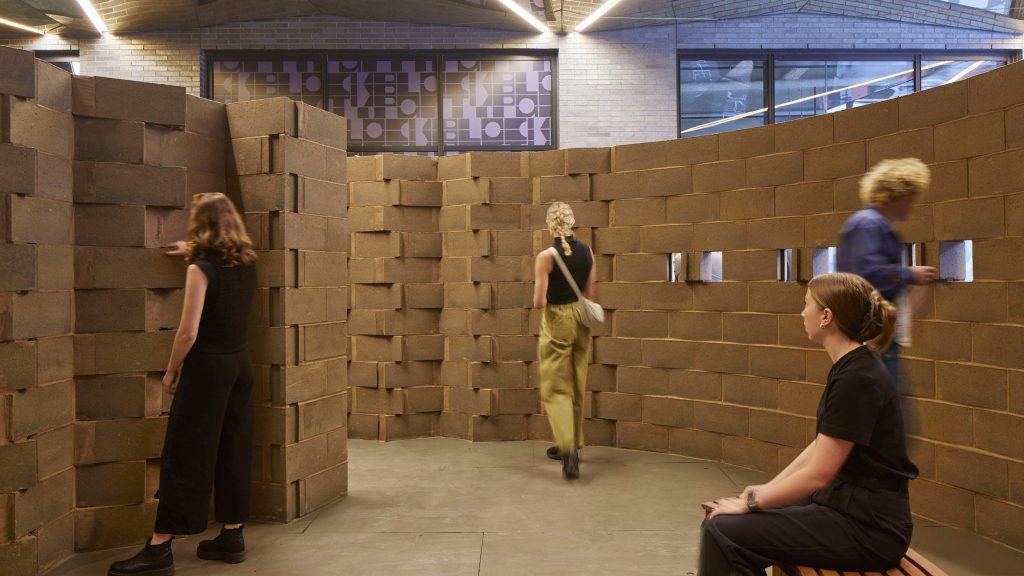
Bio-Block by SOM and Prometheus Materials
Currently, the material is going through testing to meet the American Society for Testing and Materials (ASTM) standards, and the team hopes it can be a direct substitute for Concrete Masonry Units (CMUs).
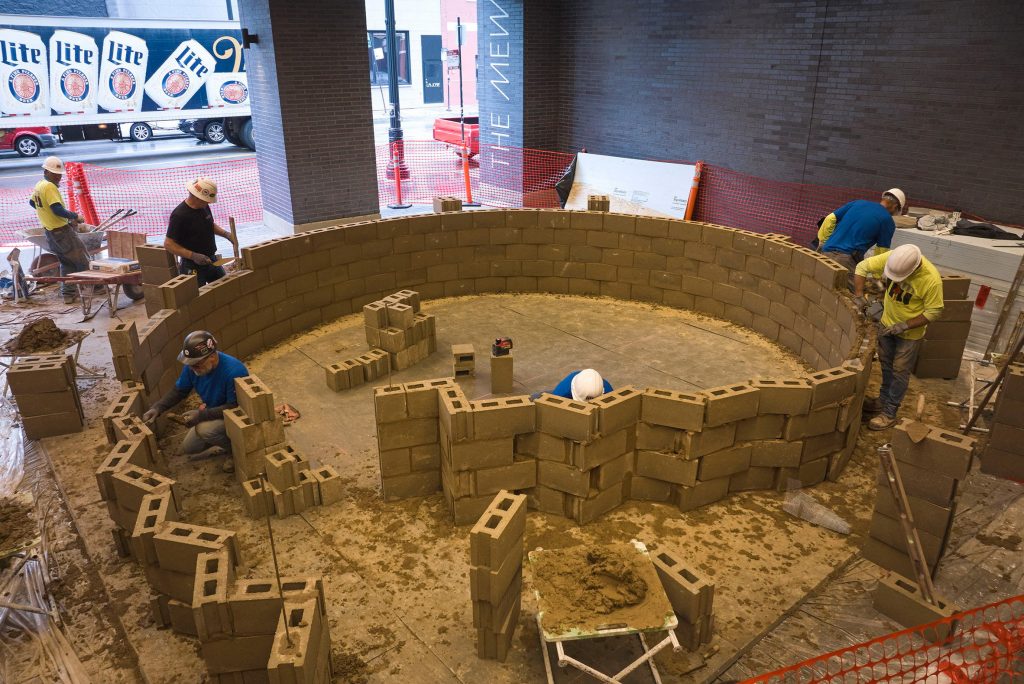
Bio-Block by SOM and Prometheus Materials
To demonstrate the qualities of the innovative material, Prometheus Materials has commissioned architecture studio SOM to create a spiral installation made of bio-bricks for the 2023 Chicago Architecture Biennial. Echoing the shell-like material composition of the bio-cement, the team conceived a spiraling form ssembled using a conventional stacked masonry technique. Pleated end of the spiral improve the structural stiffness of the installation, allowing it to be self-supported.
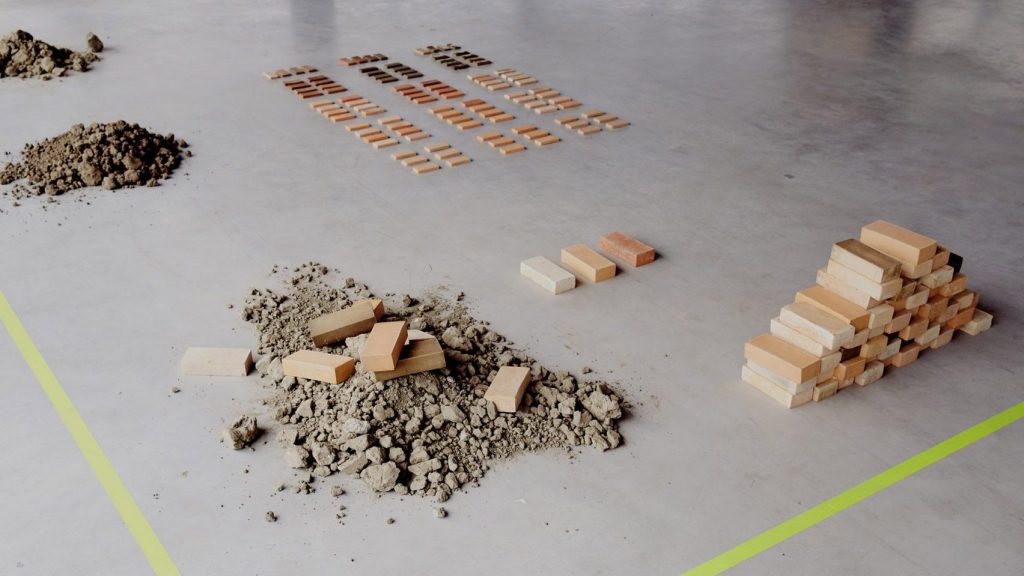
Claybens bricks by Emy Bensdorp (also header image)
Emy Bensdorp, a 2020 graduate from the Design Academy Eindhoven, produces bricks from heavily contaminated soils. PFAS “forever chemicals,” the acronym referring to per- and polyfluoroalkyl substances, are widely used to make items such as non-stick pans, umbrellas and waterproof mascara but are now known to be toxic. These substances do not break down in the environment when they leak into our soils and waterways, and can can be traced in up to 90 per cent of Dutch soils.
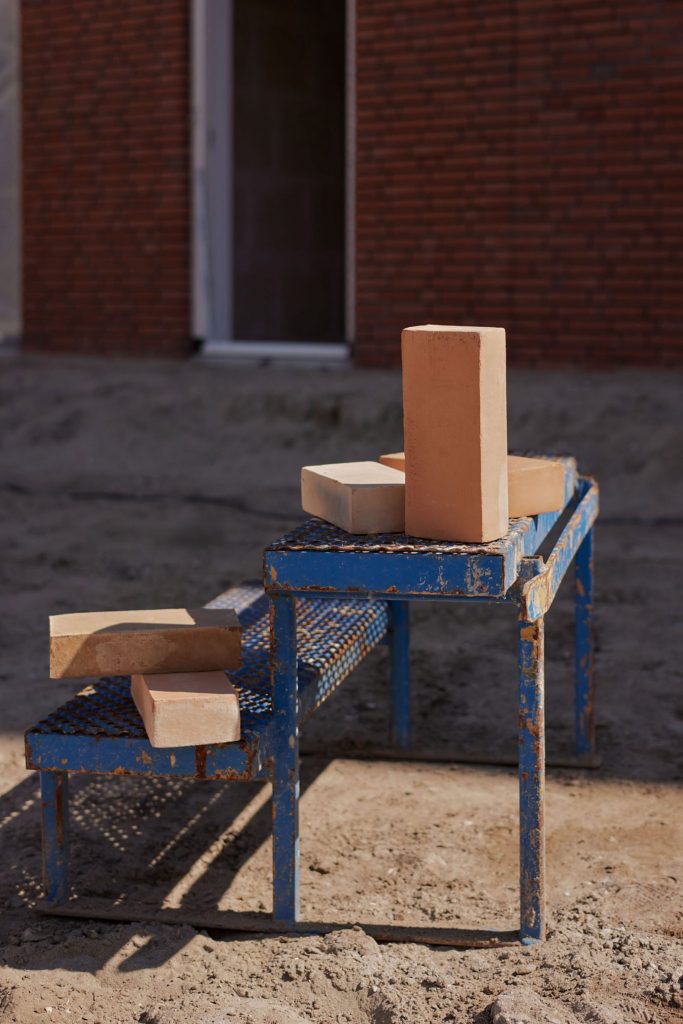
Claybens bricks by Emy Bensdorp
The problem is particularly bad in certain areas, where industrial activity, incorrect waste management or heavy use of firefighting foam have resulted in soils with extremely high levels of PFAS. But until now, there was no solution for the clay soil. Currently, contaminated soils are being stored in depots and covered with sand.
With her start-up Claybens, Bensdorp eliminate PFAS chemicals from contaminated clay soil by firing it into bricks. During the manufacturing process, ceramics are re heated to between 900 and 1,200 degrees Celsius in a kiln, destroying the PFAS chemicals, without emitting any toxic fumes or particles. The process makes use of the extreme heat of kilns to activate a chemical reaction called defluorination, which breaks down the chains of fluorine atoms that make up PFAS.
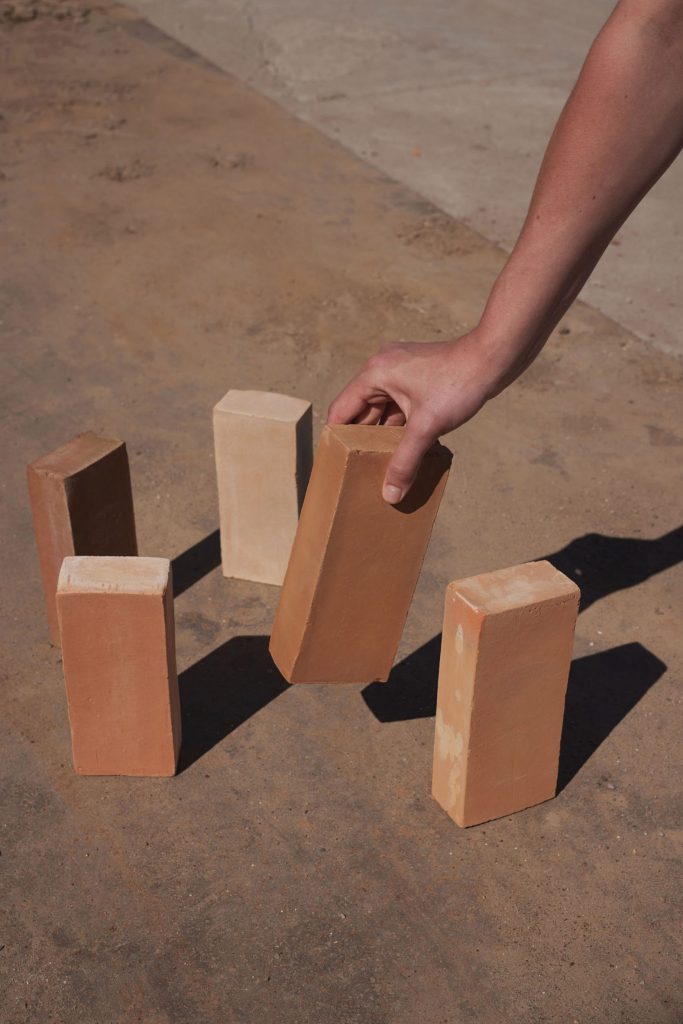
Claybens bricks by Emy Bensdorp
Bensdorp manufactures the clay soils into bricks of various colours and stamps them with a mark indicating the location of origin and amount of PFAS removed. What is great about these chemicals is that they’re actually great because they are water resistant, they’re fireproof and they last for a long time.