There are several different choices in bags for you to use. Some take thousands of years to degrade, others cost a lot of energy to make and recycle, which can also be damaging to the environment. These innovative bag options prioritize comprehensive sustainability, by finding new ways to keep the planet healthy.
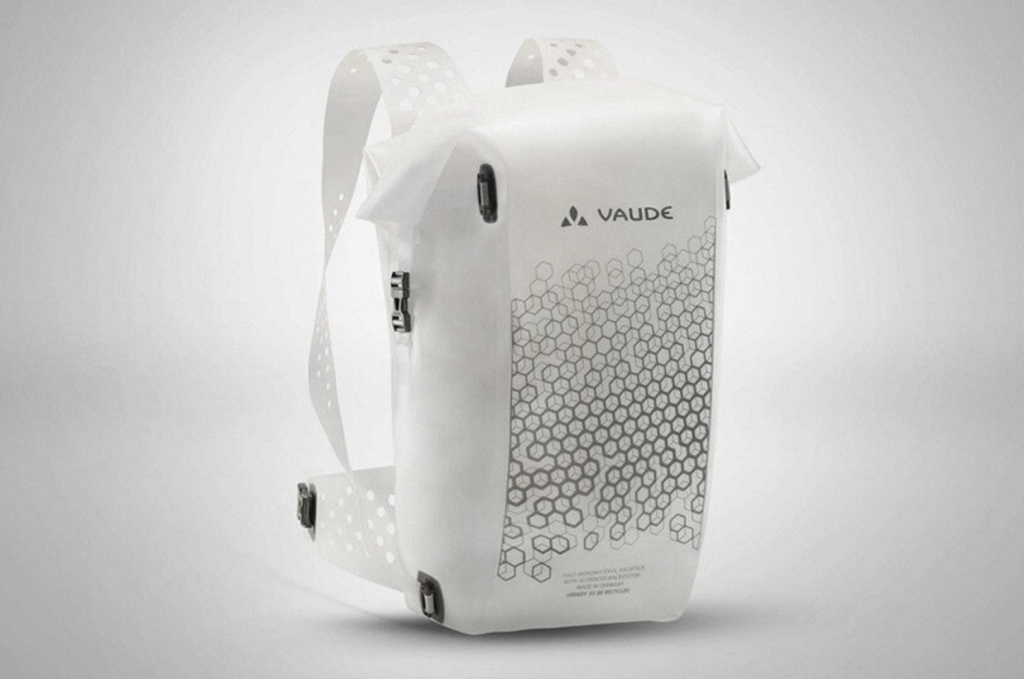
Novum 3D backpack by VAUDE
German outdoor brand VAUDE has developed what it claims is the first recyclable backpack made from mono-materials. Named Novum 3D, the product can be returned completely back to the production process at the end of its life cycle.
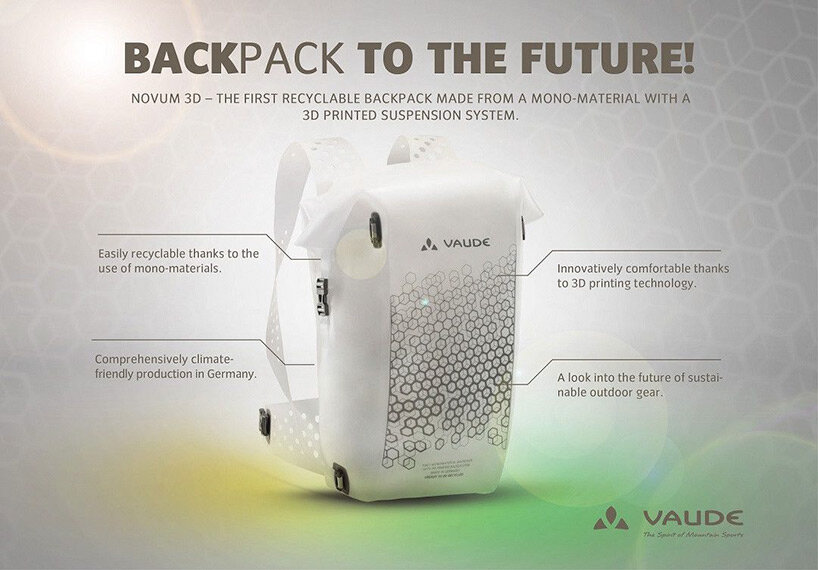
Novum 3D backpack by VAUDE
While most textile products consist of at least 5 to 10 different materials or mixed fabrics and therefore cannot be separated by type, this innovative backpack is completely recyclable thanks to its design, mono-material, welding technology, and 3D printed suspension construction.
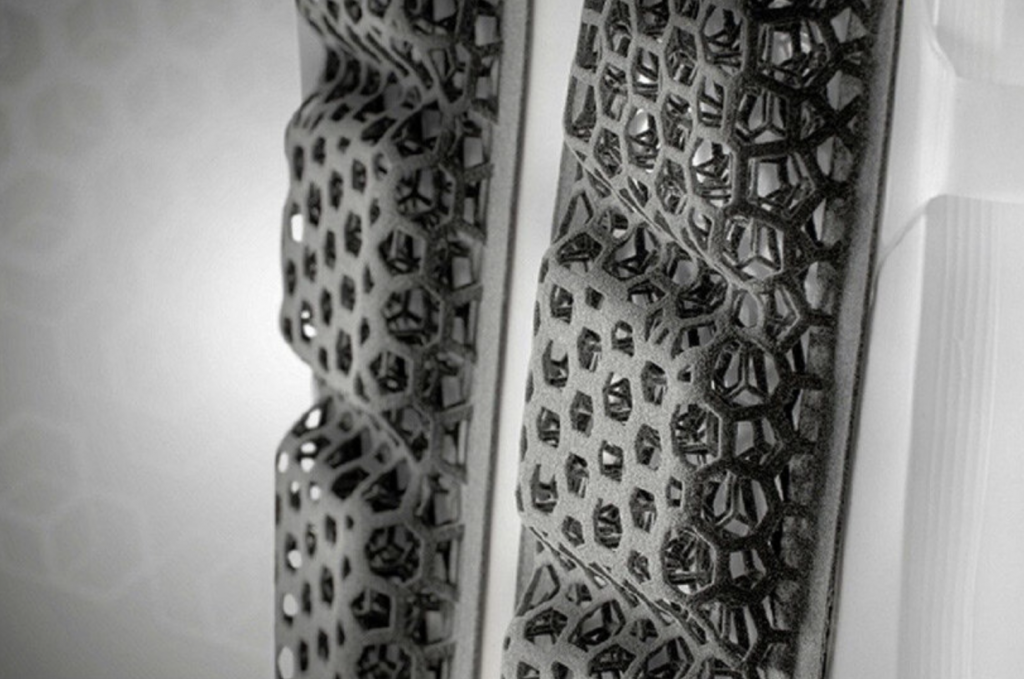
Novum 3D backpack by VAUDE
All parts of the prototype, including the back pads, the packsack, and the straps, are 3D printed from a 100% thermoplastic material (TPU), and are easily removable and fully recyclable. The honeycomb construction ensures maximum stability with minimum use of materials. The lightweight, open structure also automatically provides ideal ventilation.
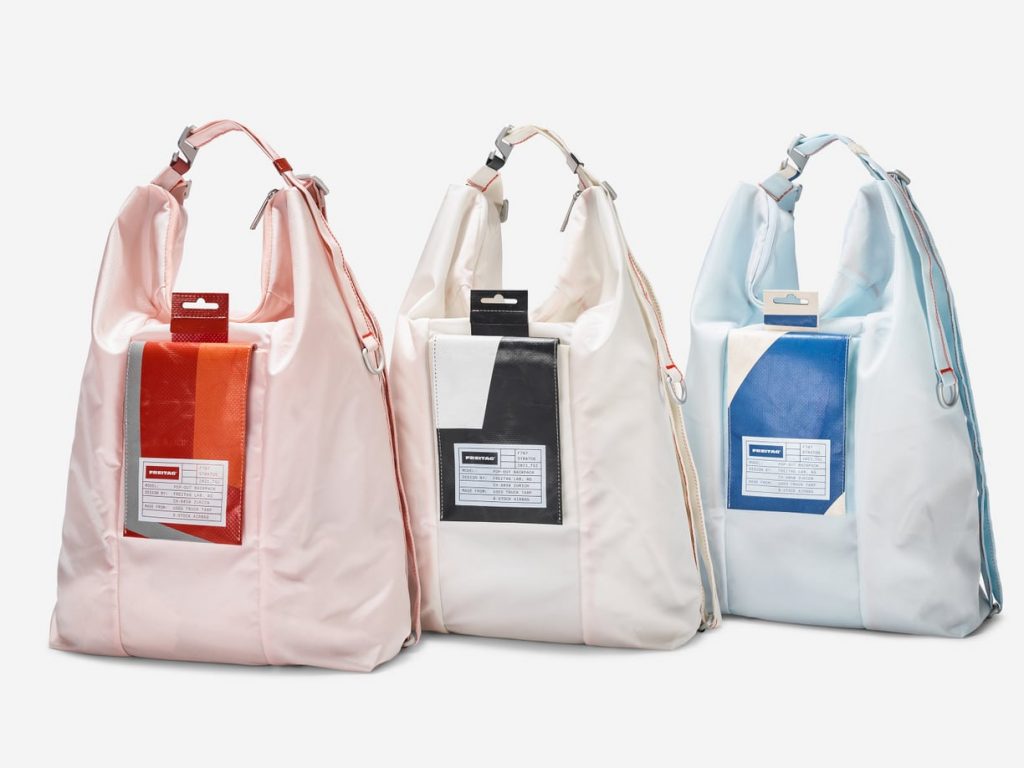
F707 Stratos rucksack by Freitag
To create its F707 Stratos rucksacks, Zurich-based bag manufacturer Freitag uses discarded truck tarpaulins and airbag fabric that failed a safety test and was rejected as a B-material.
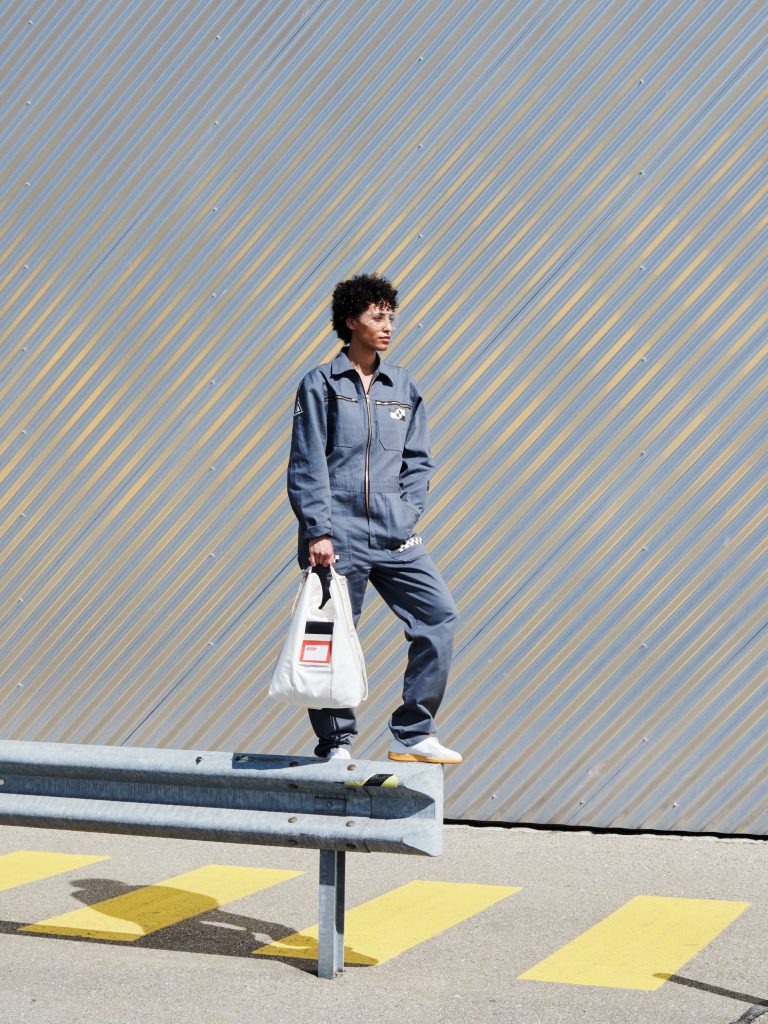
F707 Stratos rucksack by Freitag
The team decided to give the fabric a second life while taking advantage of the airbag’s initial function. Just as the airbag in a car, the backpack unfolds from its pocket made from tarpaulin.
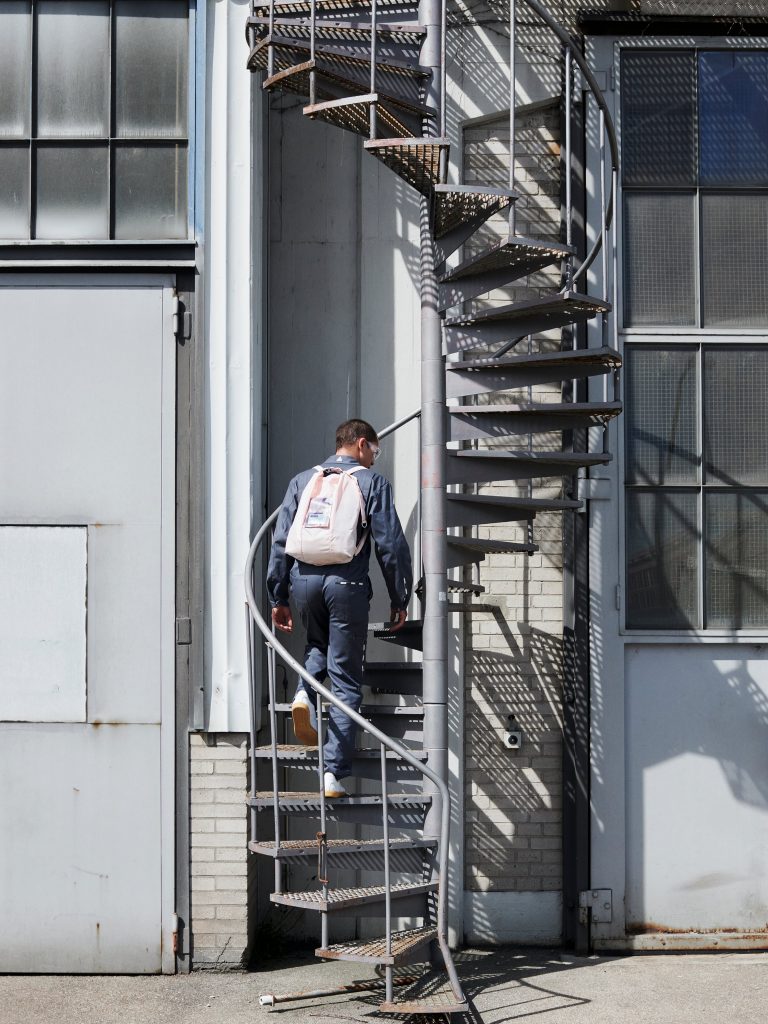
F707 Stratos rucksack by Freitag
The bag can be carried as a handbag, a backpack, and a shoulder-bag thanks to an additional strap.
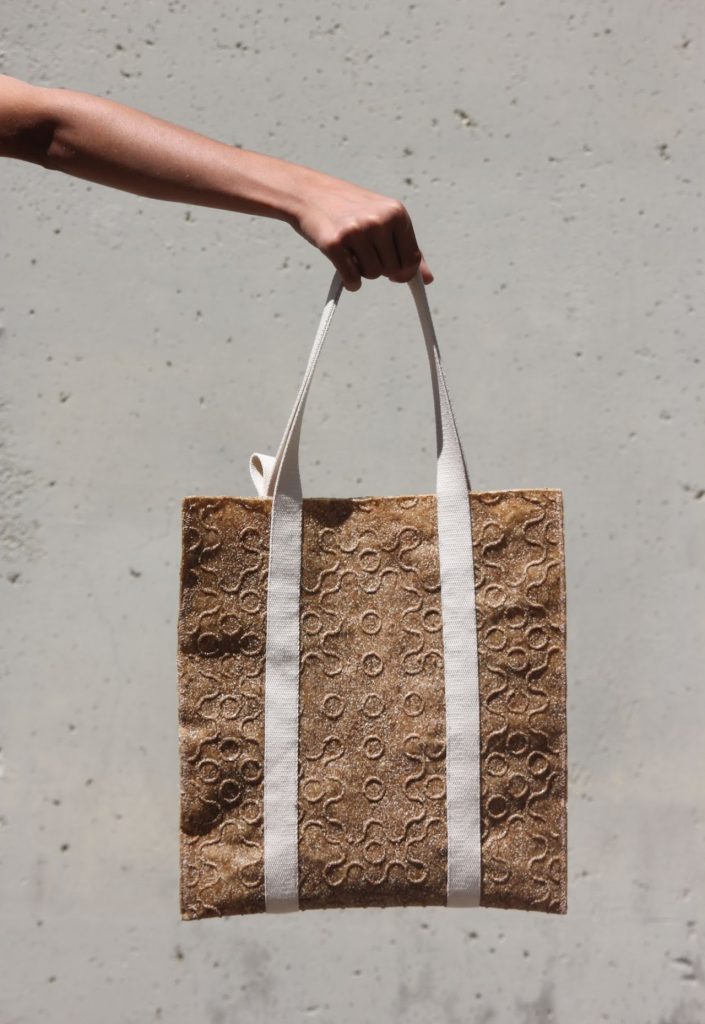
Sacalho tote bag by Guilherme Giantini (also header image)
Created in Portugal, where around 1 million tons of food are lost annually while the textile sector is responsible for up to 20% of the contamination of fresh water, Sacalho tote bag by designer Gui Giantini uses a completely biodegradable composition, resourcing the waste of garlic peels for its fabric production.
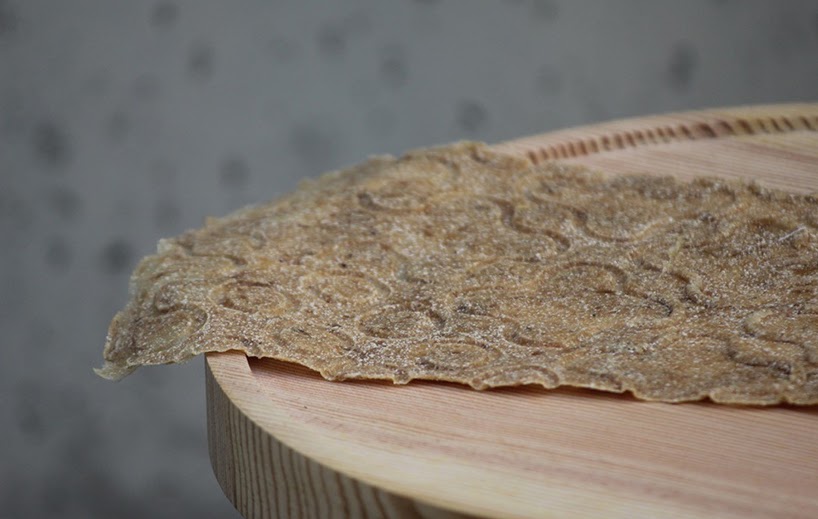
Sacalho tote bag by Guilherme Giantini
The project began with the exploration of the composition of various food residues, such as coffee grounds, wood ashes, garlic, carrot, onion, potato, egg and peanut hulls. Garlic husks, very typical of Mediterranean cuisine, was chosen.
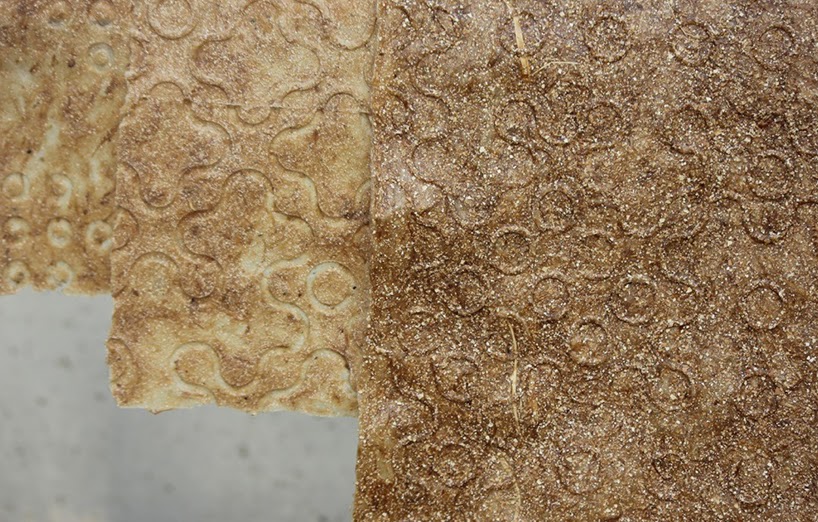
Sacalho tote bag by Guilherme Giantini
The mechanical properties of this biotextile are similar to those of two other fabrics commonly used in tote bags, cotton and TNT. The parametric design process allowed the designer to customize the dimensions of the project, generate geometric pattern options, and optimize the manufacture of modular mixing molds for the production of the bio-material. The mixture gets unmolded after two days, and the garlic husk bio-textile is sewn to take the shape of a tote bag.