The search for green materials has become increasingly urgent, as an estimated 92 million tonnes of textiles end up in landfills annually adding to such global problems as greenhouse gas emissions, climate change and the prevalence of microplastics. Concerned about the future of the planet, researchers and designers are working to deliver more regenerative materials to the fashion market, producing beautiful garments from discarded materials.
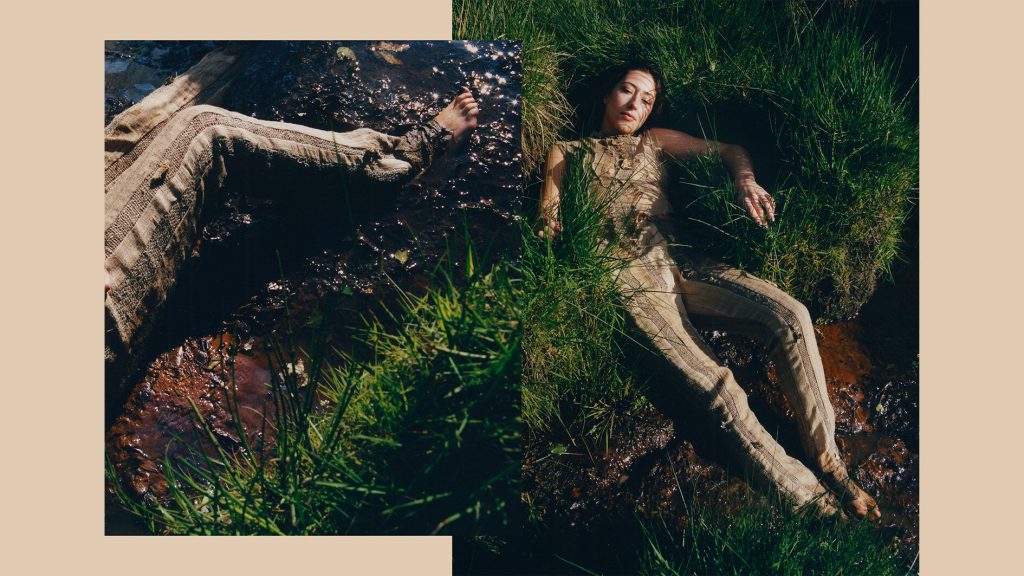
FI (Fungal Integrated) by Helena Elston (also header image)
As part of her ongoing project FI (Fungal Integrated), London-based designer Helena Elston creates various clothing using a combination of local waste products, including London-sourced textile waste, coffee sacks and vegetative filaments of fungi – mycelium.
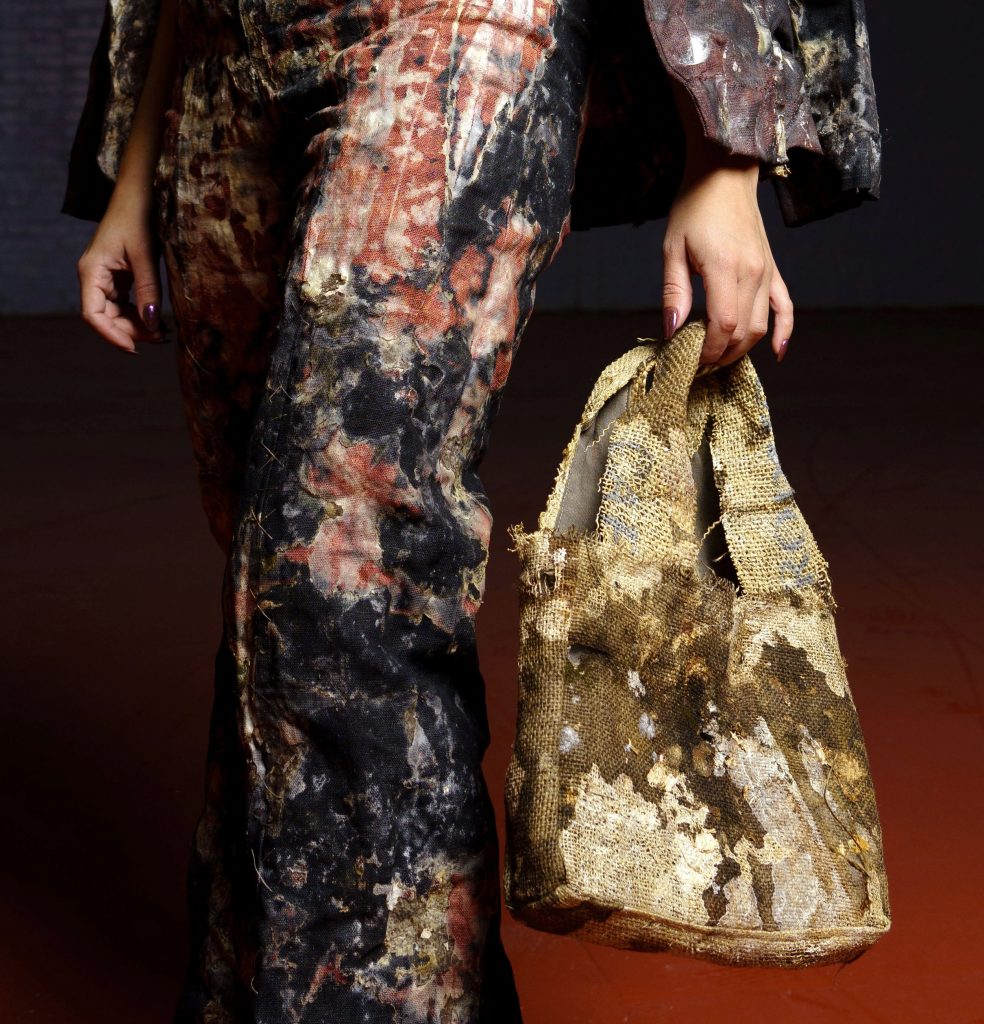
FI (Fungal Integrated) by Helena Elston
The collection includes a seamless dress, a navy trouser suit, heeled boots, and a jacket, designed to fully decompose when no longer needed rather than being disposed of in landfill, reducing waste. The time for each garment to biodegrade would depend on its material, with natural fabrics taking between two and six months to break down, according to the designer.
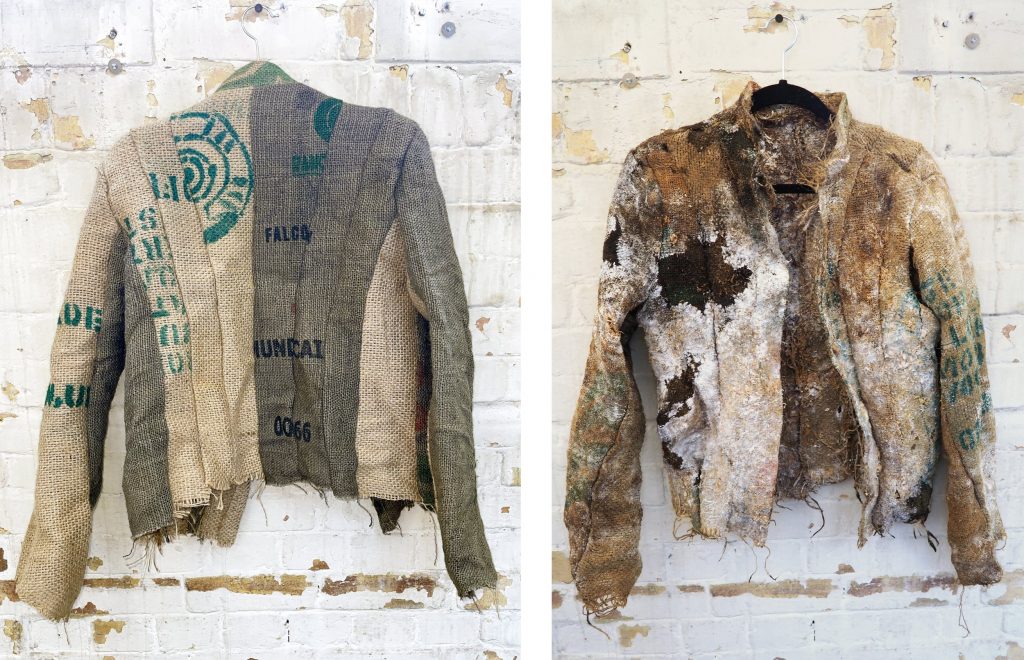
FI (Fungal Integrated) by Helena Elston (before/after)
The fabrication process, which the designer is trying to patent, involves application of surplus fabrics using a mycelium growth that lasts for roughly six weeks at a specific dampness, darkness and temperature. After that, the garments are left to dry out, after which they can be worn.
While Elston’s finished pieces are made from discarded textiles, she is also working on producing a way to use mycelium as an alternative sewing tool in order to connect patches of fabric.
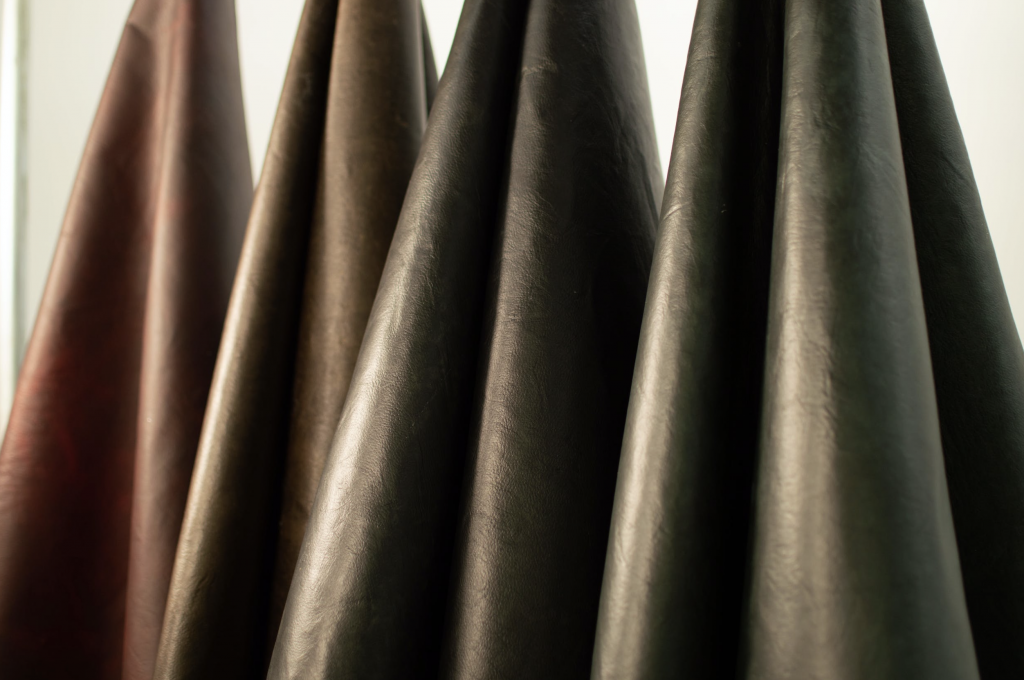
Celium™ by Polybion
Mycelium seems to be on everyone’s lips these days. But although even major brands turn to mycelium as a source of leather alternative, Polybion, biotech company based between Spain and Mexico, claims that its Celium™ leather made from bacterial cellulose is even more sustainable. According to the company, it requires fewer natural resources in its production and has a quarter of the carbon footprint compared to mycelium leathers while producing higher yields, according to a preliminary lifecycle assessment (LCA).
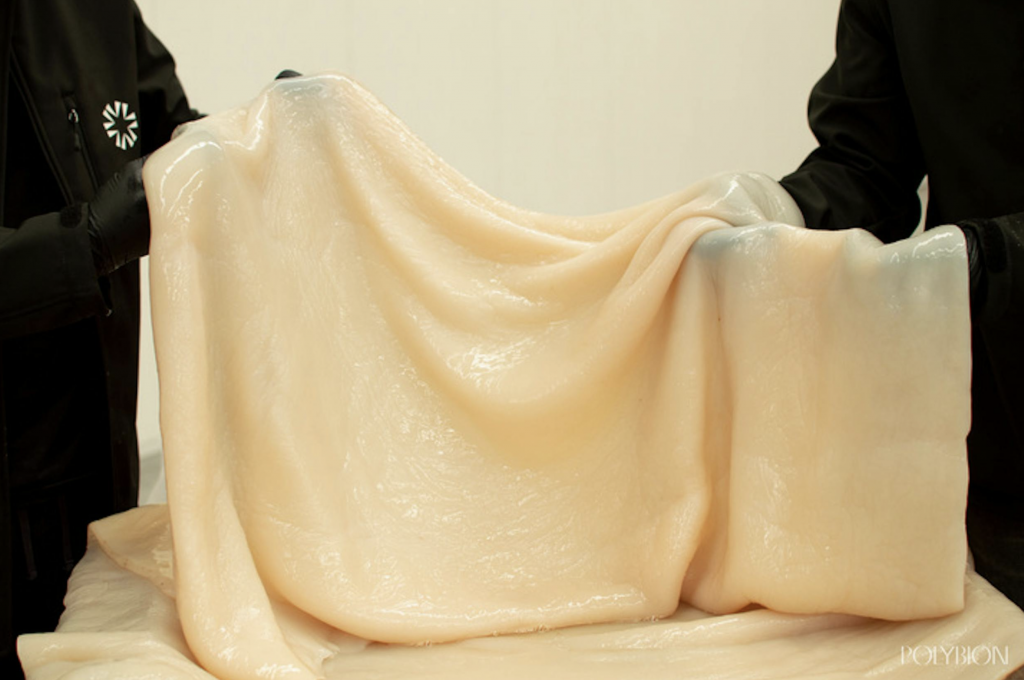
Celium™ by Polybion
Polybion grows Celium by feeding bacteria that have been genetically modified with mango fruit waste from the agriculture industry, converting the sugar it contains into cellulose as part of the bacteria’s natural digestive process. The team claims that the material possesses high-performance qualities such as strength, lightweightness, and breathability, which outperform both real and fake leathers. The biofabrication system is very efficient and uses solar-powered electricity and heat, going from waste to finished material under the same roof.
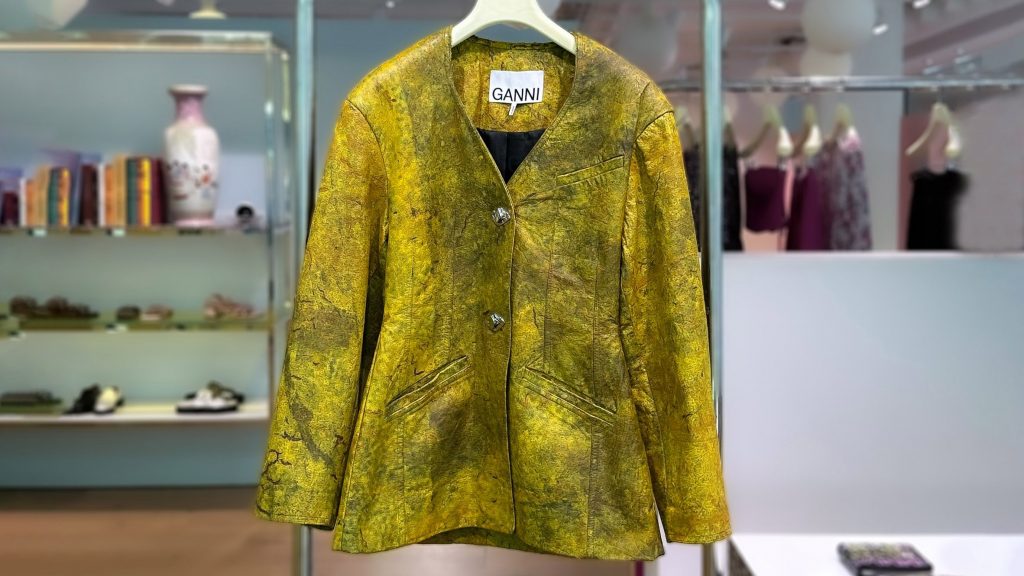
Ganni blazer from Celium™ by Polybion
This year, Ganni Fabrics of the Future, the research and development branch of the Danish fashion brand Ganni, showcased a mesmerizing marbled-yellow blazer made with Celium. For this prototype outerwear item, the Celium bacterial cellulose membrane was tanned much like cowhide.
At the moment, however, the material still needs a polyurethane coating for durability.
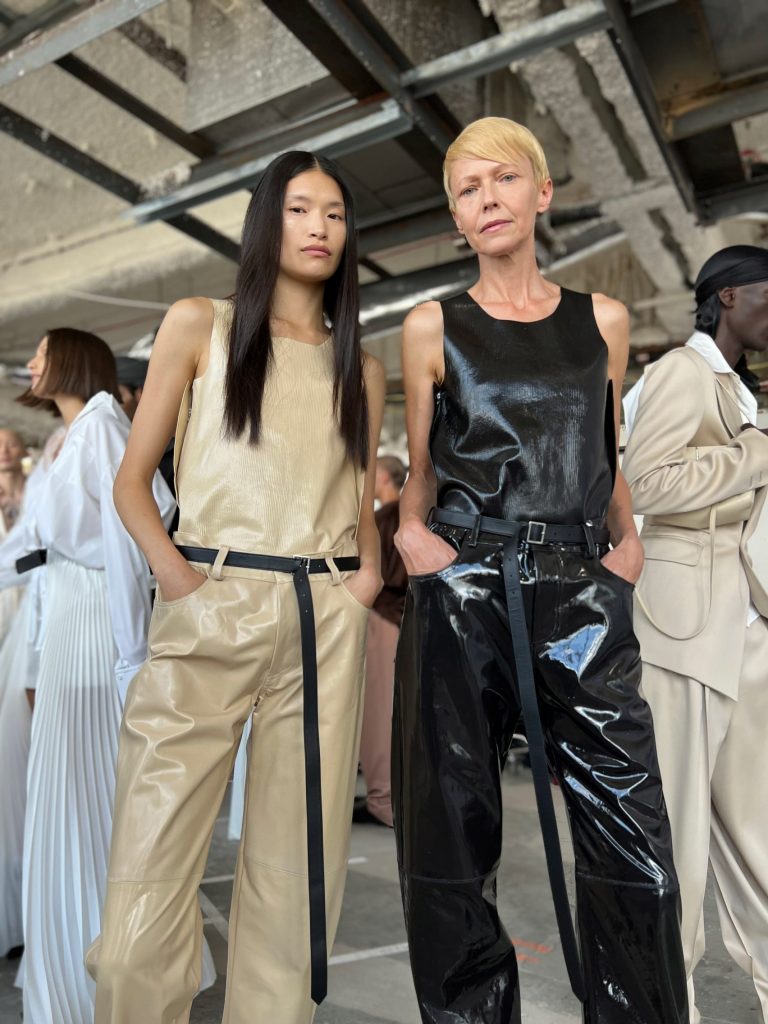
TômTex looks at Peter Do’s Spring Summer 2023 show
Novel non-woven biofabric by New York biobased material developer TômTex also has the look and feel of leather. This 100 per cent biodegradable material is fabricated from chitosan, a derivative of a biopolymer named chitin, extracted from seashell and mushroom waste, which the company sources from Vietnam-based suppliers.
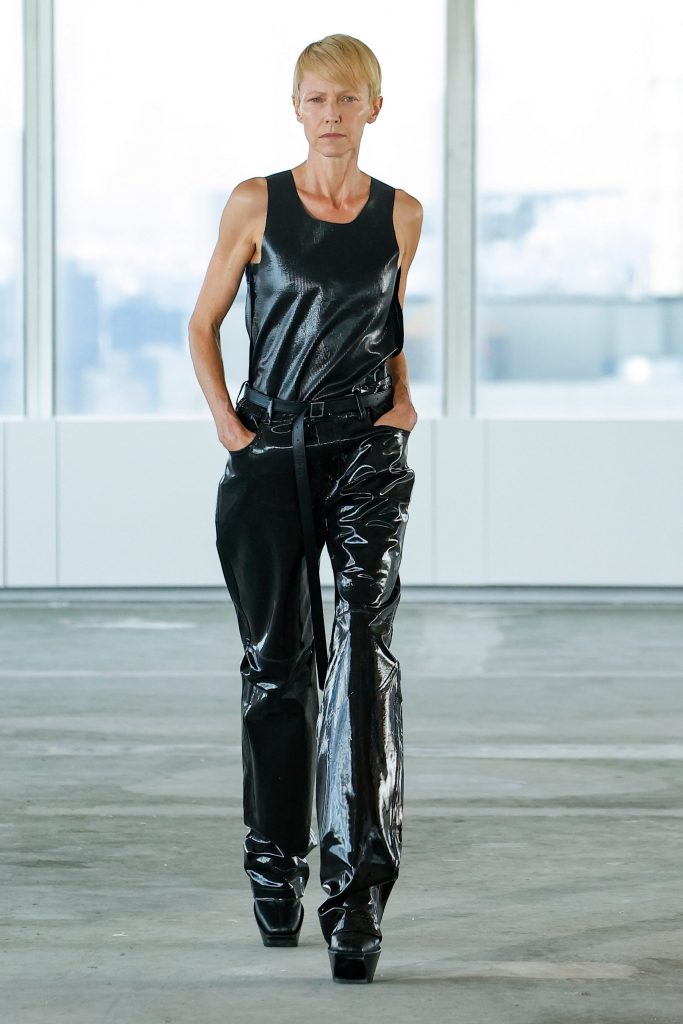
TômTex looks at Peter Do’s Spring Summer 2023 show
The innovative material alternative was used by New York-based fashion designer Peter Do to create two looks for his Spring Summer 2023 collection at New York Fashion Week. The collaboration arose from TômTex’s founder Uyen Tran and Do’s existing relationship after Tran worked for Do at the start of the fashion brand’s inception.
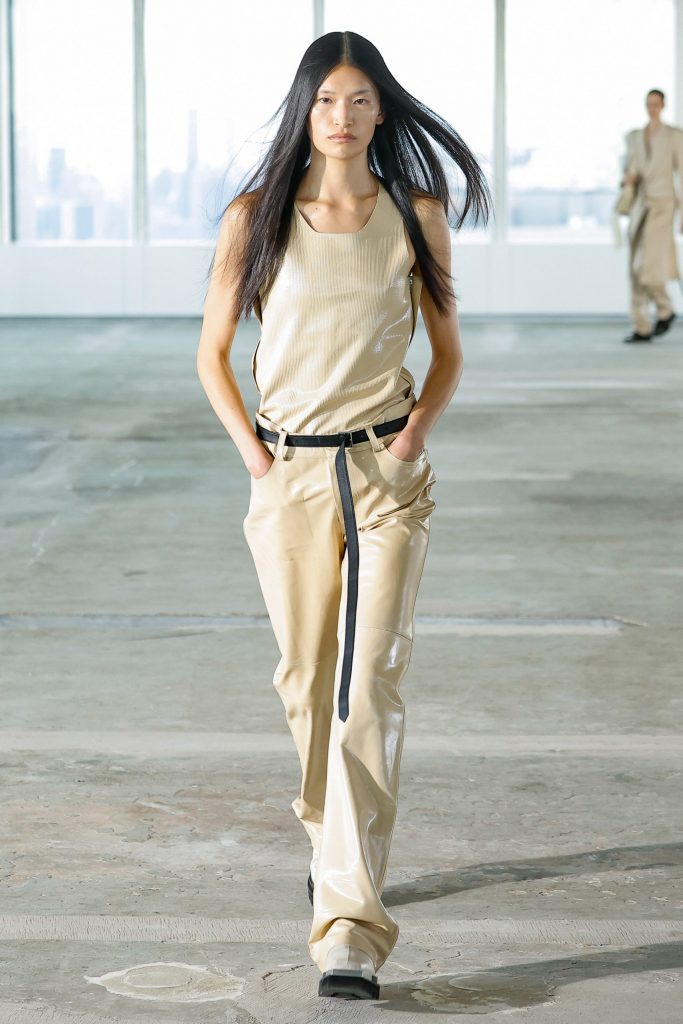
TômTex looks at Peter Do’s Spring Summer 2023 show
The brand has made significant to the material’s properties and composition since its launch back in 2020. The mechanical behavior and aesthetic properties have been improved. Without adding any plastic or petrouleum-based material, by subtly tweaking the material formula, the team managed to more than triple its absolute breaking strength. The tactility of the material has also been changed via the change in the process – now the material is more soft and silky, which allows to even make suede-like textures.