Seafood, including crabs and scallops, is widely eaten as a delicacy and the shells and husks are discarded. Researchers and designers experiment with the seafood waste, which would otherwise be thrown away, to push the limits of this natural substance and develop sustainable biodegradable materials with a wide range of applications.
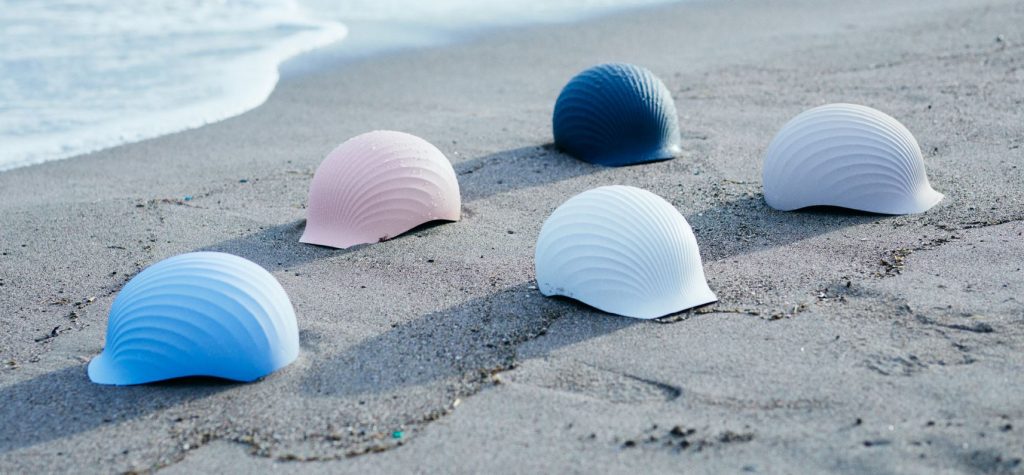
HOTAMET by Quantum
Japanese start-up Quantum has teamed up with agency TBWA HAKUHODO to reduce the disturbing amount of discarded scallop shells piling up in Sarufutsu Village, Japan, that slowly turns into a giant landfill. The area generates about 40,000 tons of shell annually, derived from marine waste when processing scallops for the food industry.
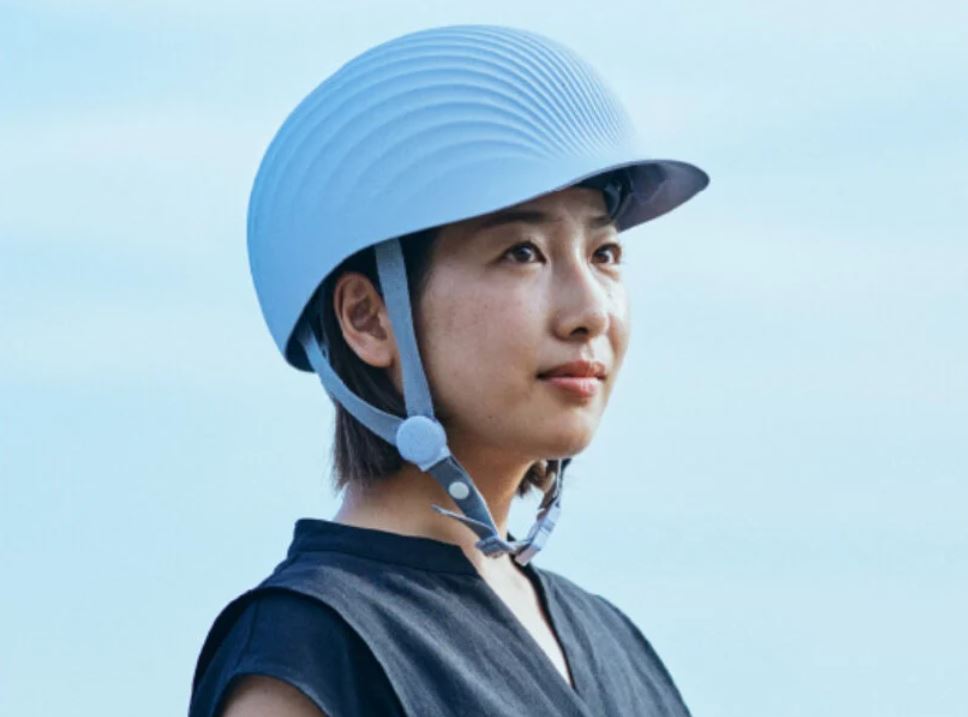
HOTAMET by Quantum
The team used the husks to create a robust and lightweight head protector for local workers and employees to use in a variety of situations, from everyday use to work sites. Made from eco-friendly plastic fused with recycled shells, HOTAMET helmet has a design that pays homage to the shape of the scallop husks they were made of.
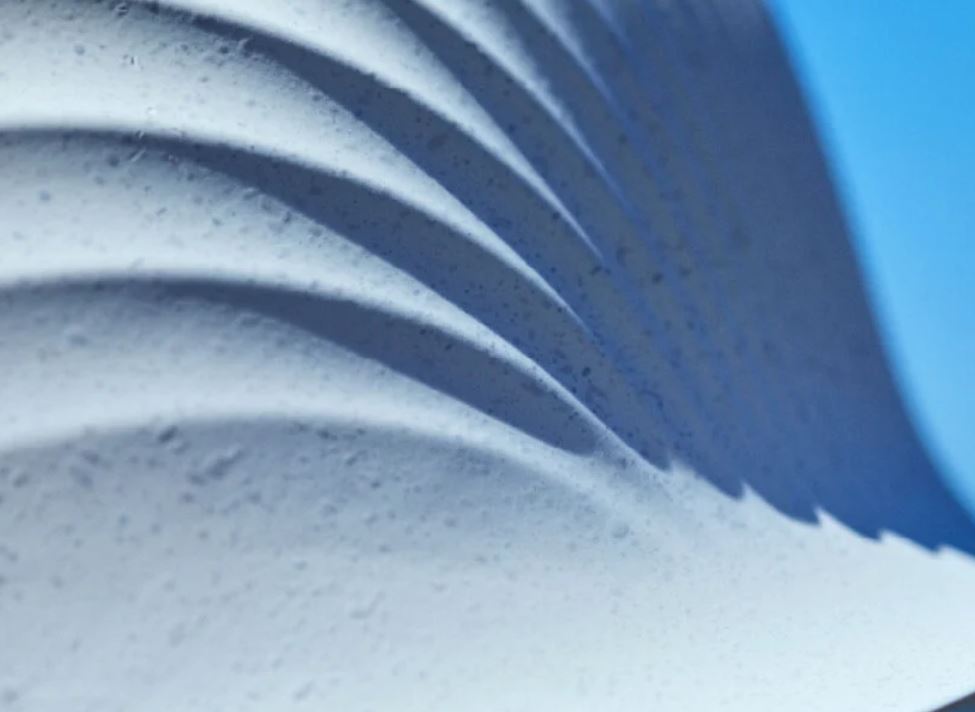
HOTAMET by Quantum
According to the team, by adopting a rib structure peculiar to seashells, the scallop helmet’s durability is increased by about 30% compared to the conventional shape. In the meantime, it only weights about 400 grams, which makes it a great choice for various situations, such as earthquakes, tsunamis, and snow damage due to climate change.
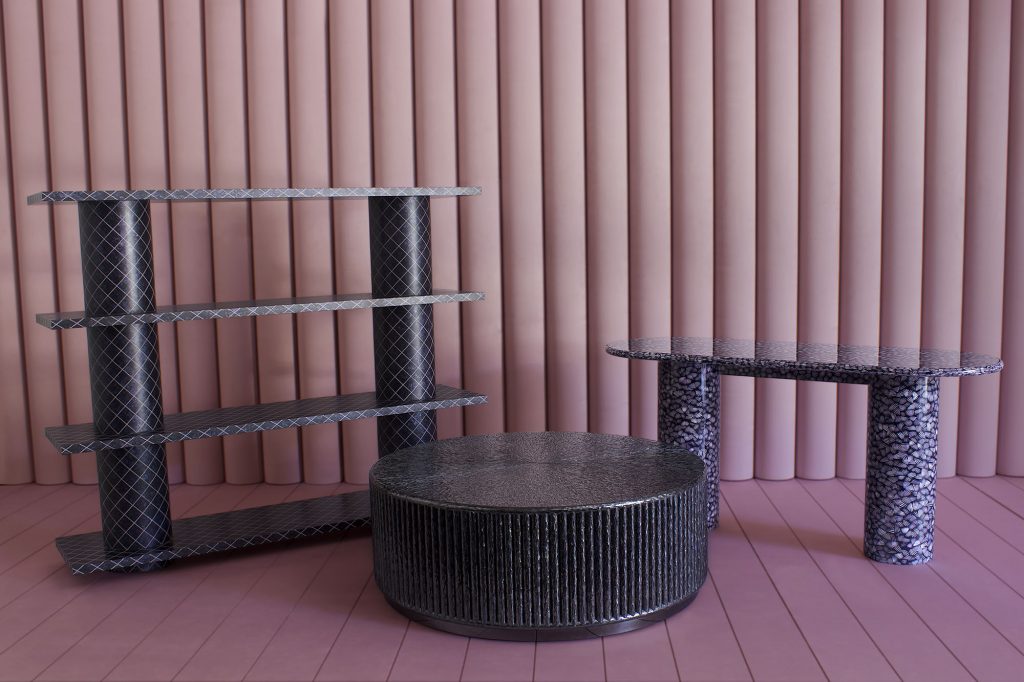
Exploring Eden by Bethan Gray and Nature Squared (also header image)
The collaboration between British designer Bethan Gray and ethical design brand Nature Squared has resulted in a collection of iridescent furniture clad in leftover materials from the seafood industry.
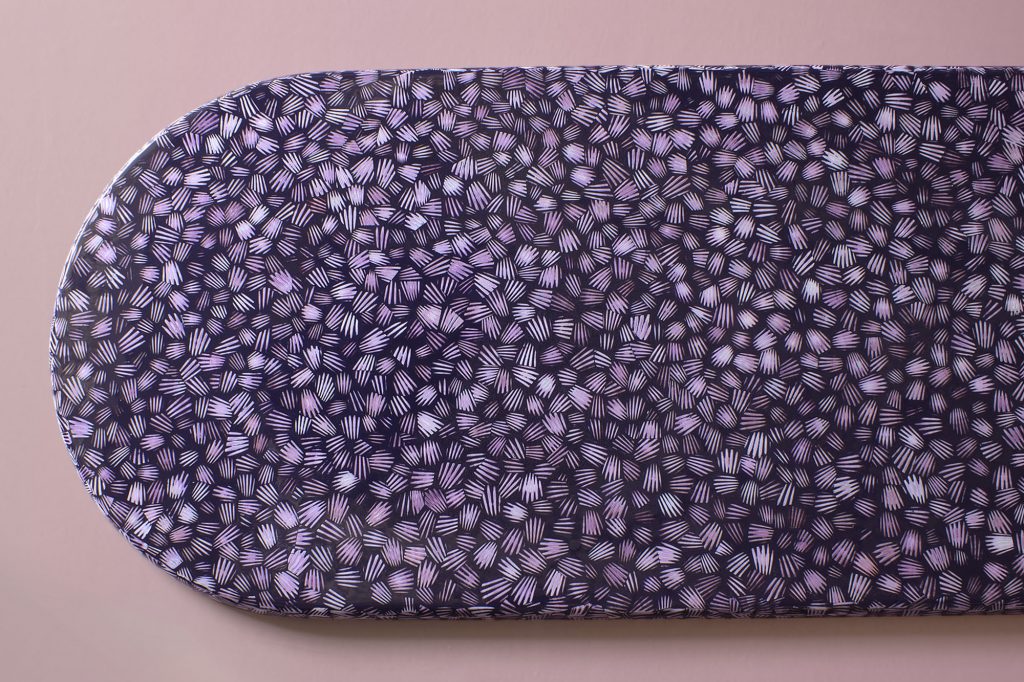
Exploring Eden by Bethan Gray and Nature Squared
Set on a mission to create truly innovative sustainable surfaces, Nature Squared works with fishing communities and craftspeople in the Philippines. The company buys the shells from fishermen on the island of Negros, where extensive conservation efforts are being made, especially in the recovery of damaged plastic fishing nets that choke the local seas. The workers collect the seafood, tin it and would then otherwise throw the shells away. After that, Nature Squared employs 250 local artisans, who turn the raw shells into luxury surface materials that are usually used for the interiors of super yachts and private jets.
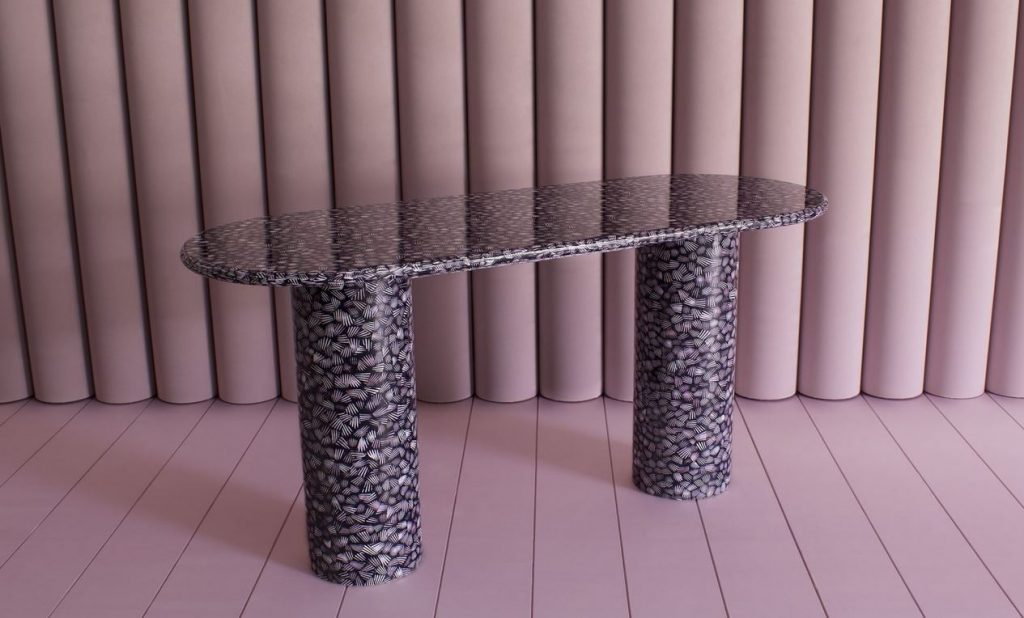
Exploring Eden by Bethan Gray and Nature Squared
The Exploring Eden collection exemplifies the merging of traditional craftsmanship with precision furniture making and exquisite design. To create a series of cylindrical, fluted stools, a scallop shell table and a pen shell coffee table, as well as a capiz shell shelving unit, Nature Squared produces fine shell-threads from leftover mother-of-pearl taken from river-pearl cultivation. Each thread is then ground down to the desired smoothness and fineness before being inlaid into the base material, and the gaps filled in with a black resin. The inlay process for each item takes many weeks to complete due to the intricate detailing and high quality finish.
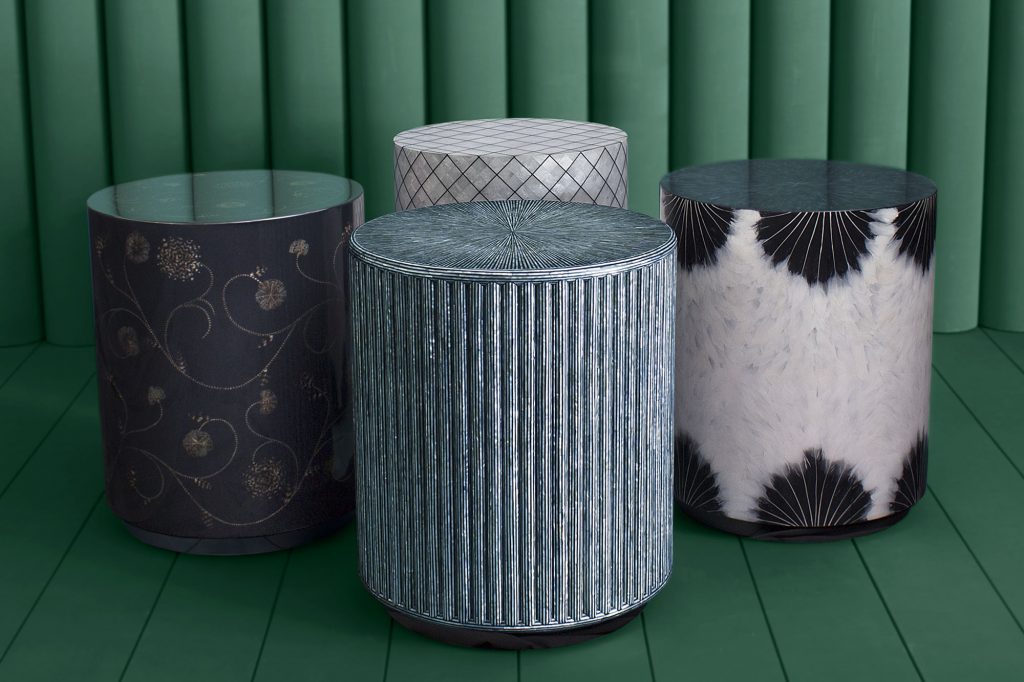
Exploring Eden by Bethan Gray and Nature Squared
The scallop shells used in the production of the collection come in a wide variety of natural colours from acid yellow through to inky purple and pink. This can be seen in such items as a table with etch-like patterns, made by inlaying pink scallop shells into the surface, and a shelving unit with a pink, gridded pattern that makes use of scrapped capiz shells. The pearlescent and iridescent qualities of capiz, pearl, scallop and pen shells give each of the furniture pieces a unique pattern and colour.
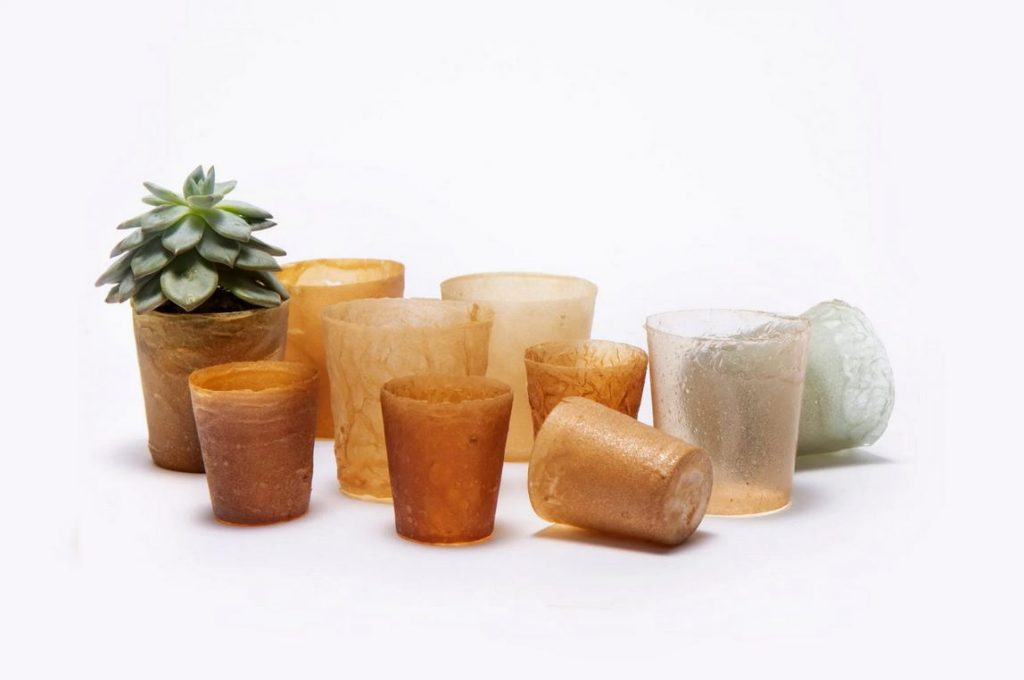
Shellworks by Ed Jones, Insiya Jafferjee, Amir Afshar and Andrew Edwards
The project, called Shellworks, by Ed Jones, Insiya Jafferjee, Amir Afshar and Andrew Edwards from the Royal College of Art and Imperial College, focuses on recycling the shells of crustaceans. The team has developed a series of machines that turn this seafood waste into a biodegradable and recyclable bioplastic.
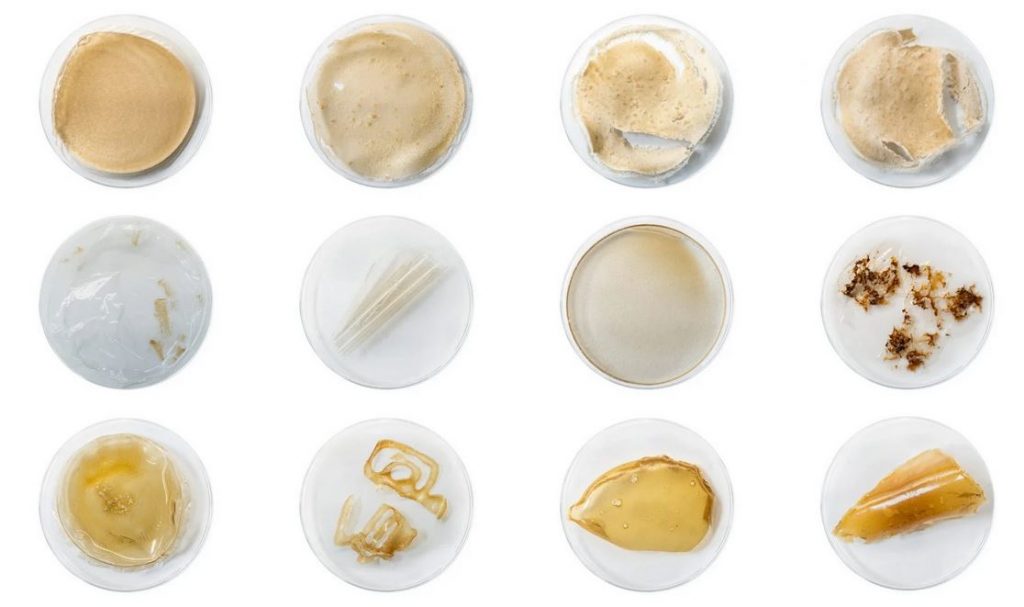
Shellworks by Ed Jones, Insiya Jafferjee, Amir Afshar and Andrew Edwards
The material is made via combining vinegar and a biopolymer called chitin that makes up the exoskeleton of crustaceans. Before chitin can be turned into a practical material, it needs to be chemically extracted from its source, which is very time-consuming. So the designers decided to forego the existing extraction methods and developed their own. Their experiments resulted in the invention of five manufacturing machines, called Shelly, Sheety, Vaccy, Dippy and Drippy.
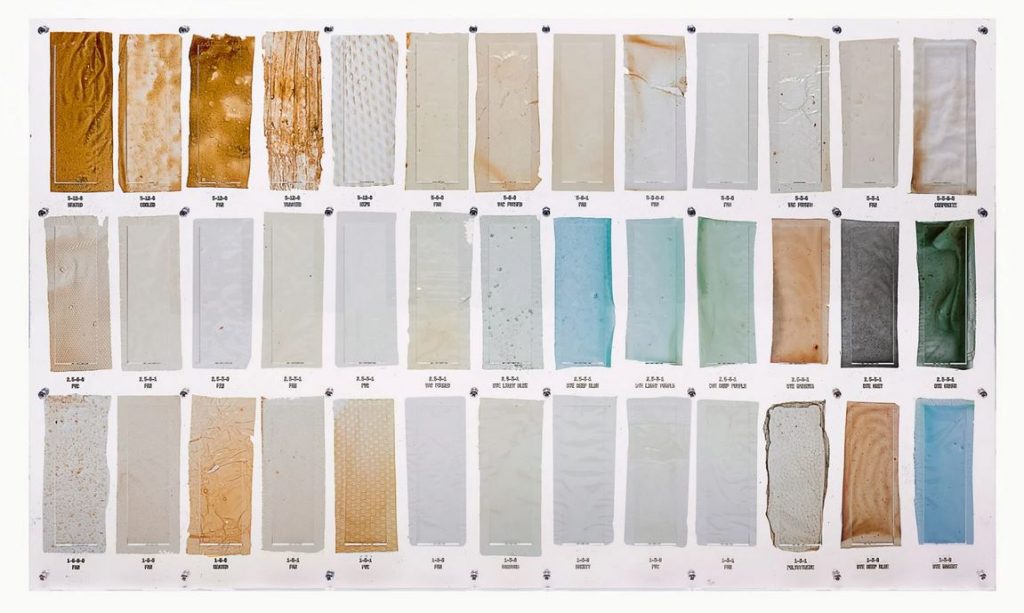
Shellworks by Ed Jones, Insiya Jafferjee, Amir Afshar and Andrew Edwards
The first machine, called Shelly, is a small-scale extractor designed to offer complete control over each parameter of the process in order to allow for further experimentation at the polymer level of the material.
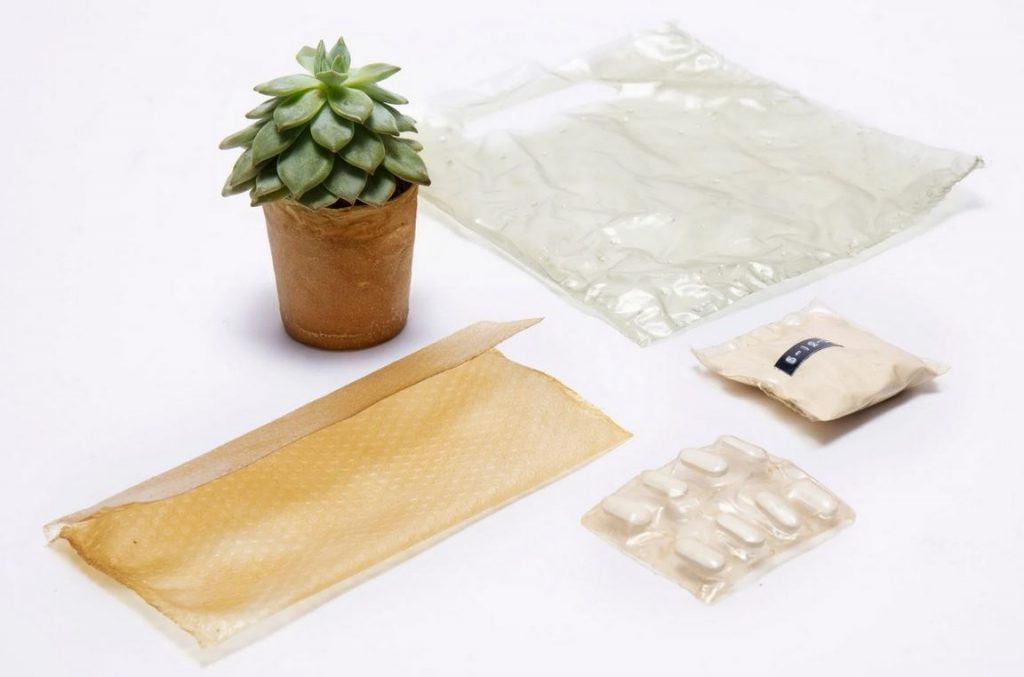
Shellworks by Ed Jones, Insiya Jafferjee, Amir Afshar and Andrew Edwards
Each of the other four machines exploit a specific property of the bioplastic solution to demonstrate its potential. Sheety uses heat and wind to transform the bioplastic solution into flat sheets of material, which can be glued together using the liquid form of the bioplastic; while Vaccy forms the sheets into moulded packaging, taking on the shape of whatever object is put in the vacuum former. The last machine, Dippy, is comprised of two solid metal elements attached to a heat source, which are dipped in the liquid material and left to dry, forming various 3D vessels like cups and containers.
By adjusting the ratios of the base ingredients, the designers can change different material properties, such as stiffness, flexibility, thickness and opacity of the material, according to need. The resulting biomaterial can act as a sustainable alternative to single-use plastics. The areas of application include but are not limited to anti-bacterial blister packaging, food-safe carrier bags and self-fertilising plant pots.