Aluminum furniture is frequently associated either with garden chairs or with highly functional pieces manufactured utilizing industrial aluminum. Some designers, however, aim to prove this sustainable material offers great possibilities for creating state-of-art furniture in most unexpected designs and techniques.
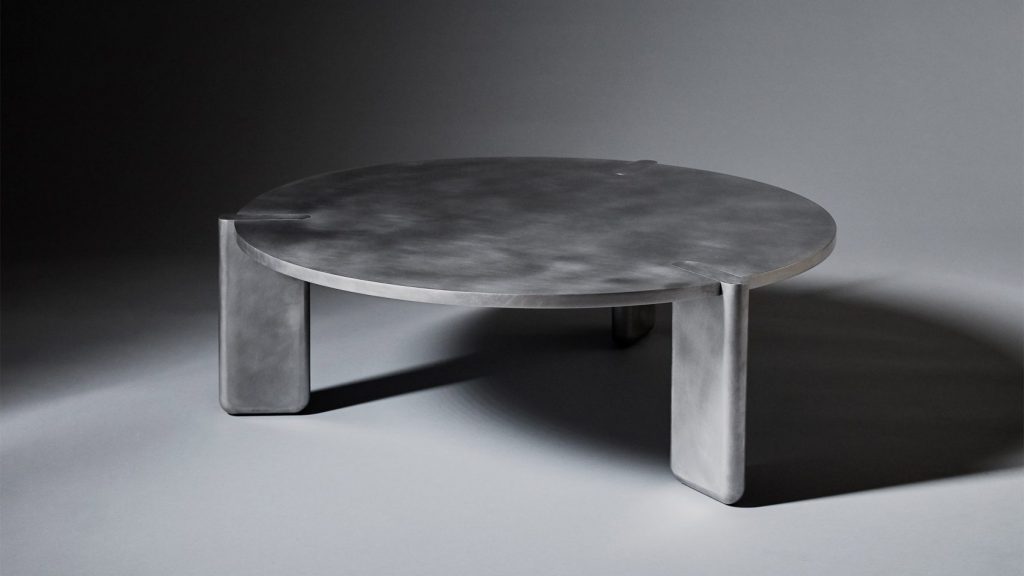
DVN table by Pelle
New York studio Pelle headed by Jean and Oliver Pelle has created DVN Table, a low table made from pieces of solid aluminum that are milled to a tolerance of 1/1000 of an inch and fixed together utilizing traditional Japanese joinery techniques. The team describes the resulting piece as an experiment in innovative manufacturing and hand craftsmanship and an attempt to create something really basic.
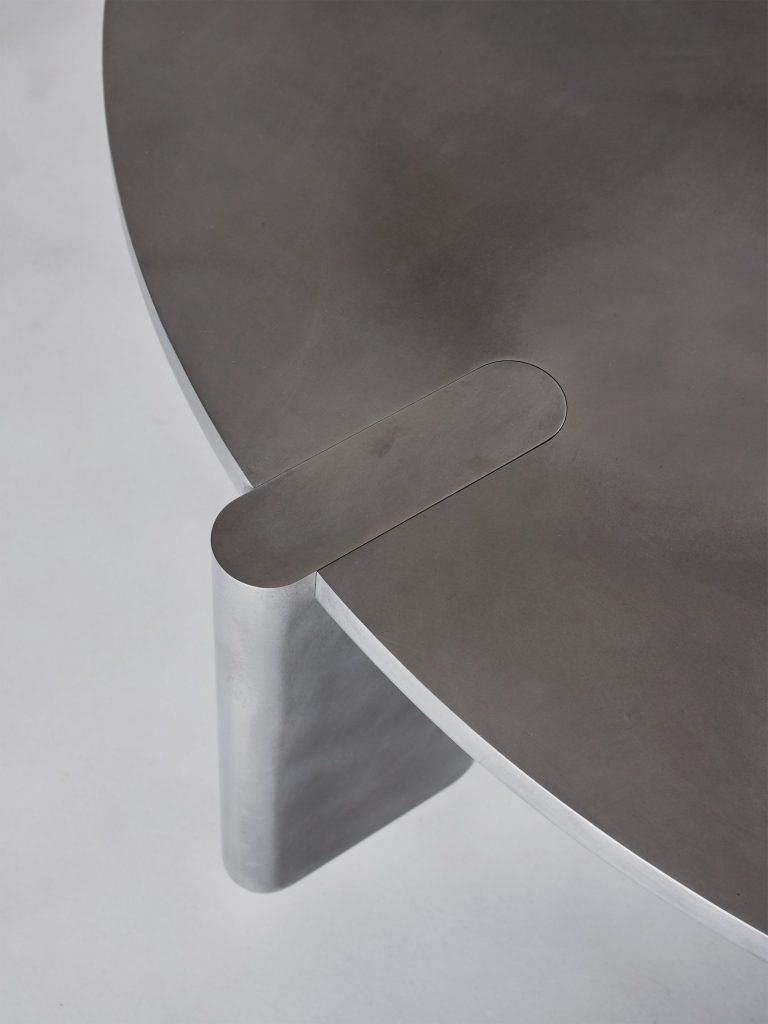
DVN table by Pelle
The fact the item is made of metal, not, wood, adds extra excitement to the result. The circular tabletop is made entirely from solid aluminum with a hand-polished surface achieved using different grades of sandpaper. Three solid aluminum curved legs are attached to the tabletop with the help of a tongue and a groove connection which is completely concealed within the internal structure. Custom-milled bits were created to precisely carve the metal components so they interlock and form these hidden, friction-based connections. This type of connection without using nails or fasteners is borrowed from traditional Japanese joinery and enhances the illusion there is nothing holding the supports in place.
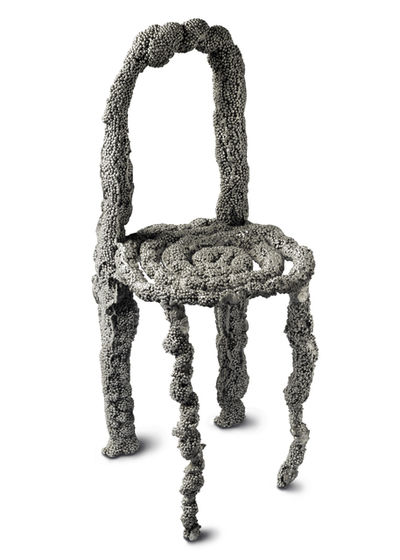
Los Huesos series by Chris Wolston
New York based artist Chris Wolston has developed a Los Huesos (Spanish for ‘skeleton’) series of furniture manufactured as an experiment with atypical mediums that alter the ordinary outcome of aluminum sand-casting. Wolston added various types of foam material to sand and observed how they transformed when combined with molten metal.

Los Huesos series by Chris Wolston
During the process the heat of the aluminum melts the soft foam leaving an impression of the material’s original texture. Thus, the surface of chairs is defined by the tiny foam beads, while larger pieces, like the table, are produced by interlocking of organically-shaped tabletop cast in sand with the legs made of Styrofoam squares and foamed aluminum sheeting, which is an architectural material ordinarily used for sound-proofing.
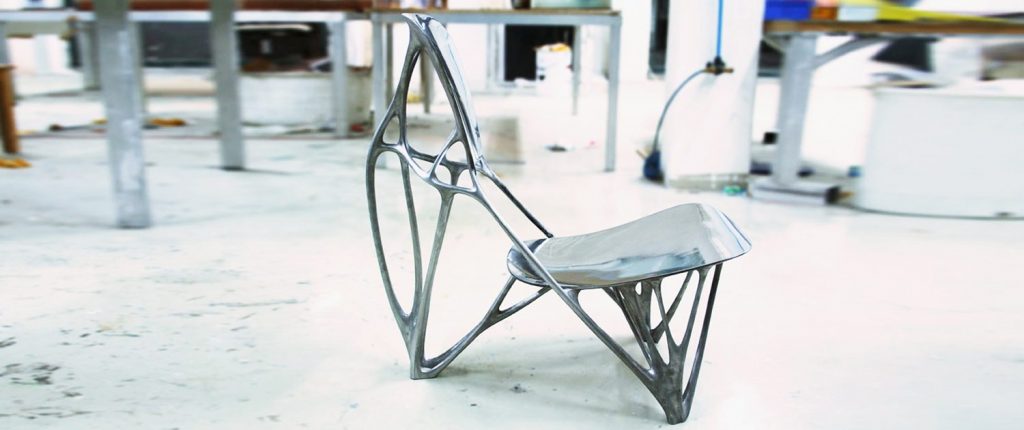
Bone Chair by Joris Laarman Lab
Amsterdam based Joris Laarman Lab creates bespoke aluminum furniture using the most innovative software and production techniques.
The structure of their Bone Chair was created using the algorithm which was developed by the German engineer Professor Lothar Harzheim, together with the International Development Centre Adam Opel GmbH, which mimics the ability of bones to take away material where it is not needed, in order to optimize car parts. The computer-generated form had to be refined for the specifications of aluminum, which resulted in a much more slender shape. If the chair was assembled from cast components, it would have visible welding stains, so to cast the piece in one go the team chose to use complex molds assembled from 3D printed ceramic parts.
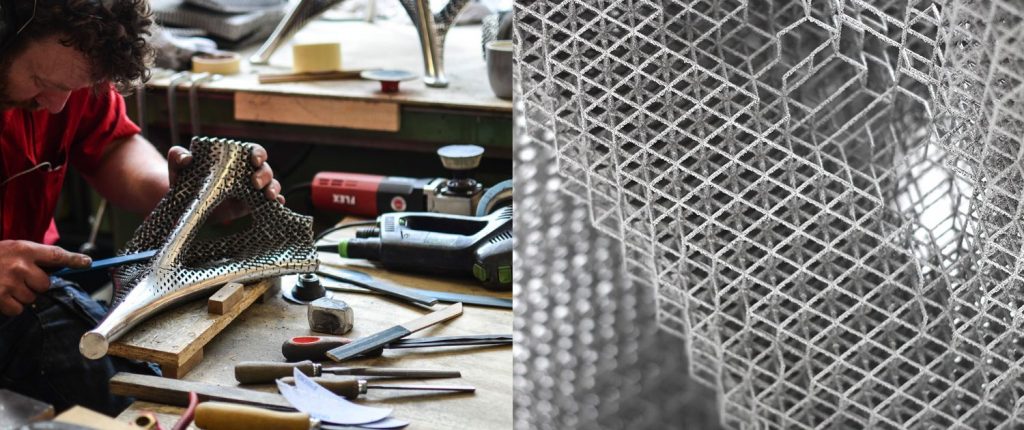
Gradient Chair by Joris Laarman Lab
The Gradient collection which consists of a chair and a lounge is an exploration of cellular based structures. Using generative design tools and new material research, the team created a lightweight aluminum foam-like structure that is engineered on a cellular level. The solid cells in the design create structural strength and rigidity, while the more open cells create material reduction and lightness. The mixed textile upholstery for the lounge was knitted on a computer controlled knitting machine exactly fitting the hexagonal pattern of the structure.
header image: Gradient Lounge by Joris Laarman Lab