To create more sustainable fashion products and shift collective behaviours around our consumption-oriented habits towards forming a sustainable future, designers collaborate with researchers and look to plant-based materials. Algae, which is abundant, is one of the options.
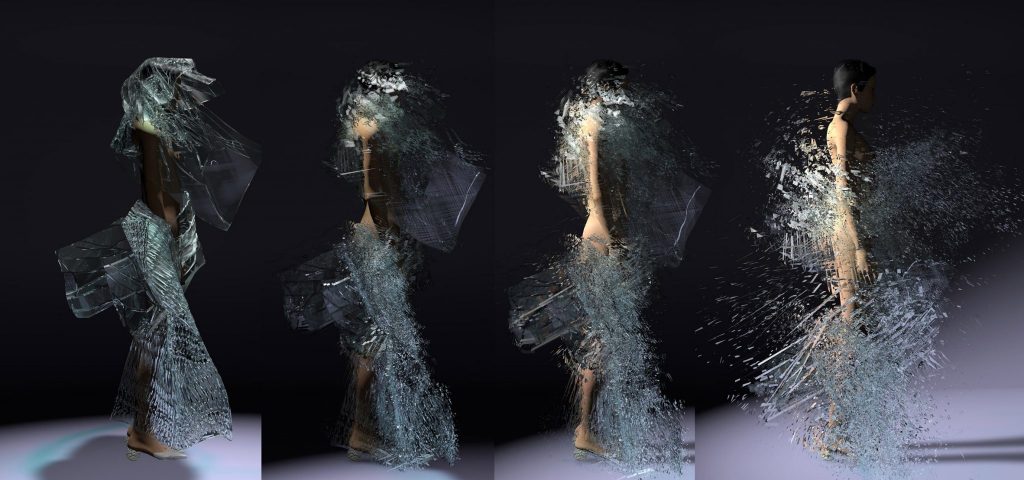
Decomposition of Materiality and Identities project by Scarlett Yang
After becoming aware of the amount of waste created by the fashion industry, Central Saint Martins graduate Scarlett Yang developed a biomaterial made of a mixture of water, coloured dye, algae extract and silk cocoon protein. She used it to create a dress that grows over time and can decompose in 60-degree-celsius water within 24 hours. Alternatively, the garment would degrade naturally in rain, river or sea water.
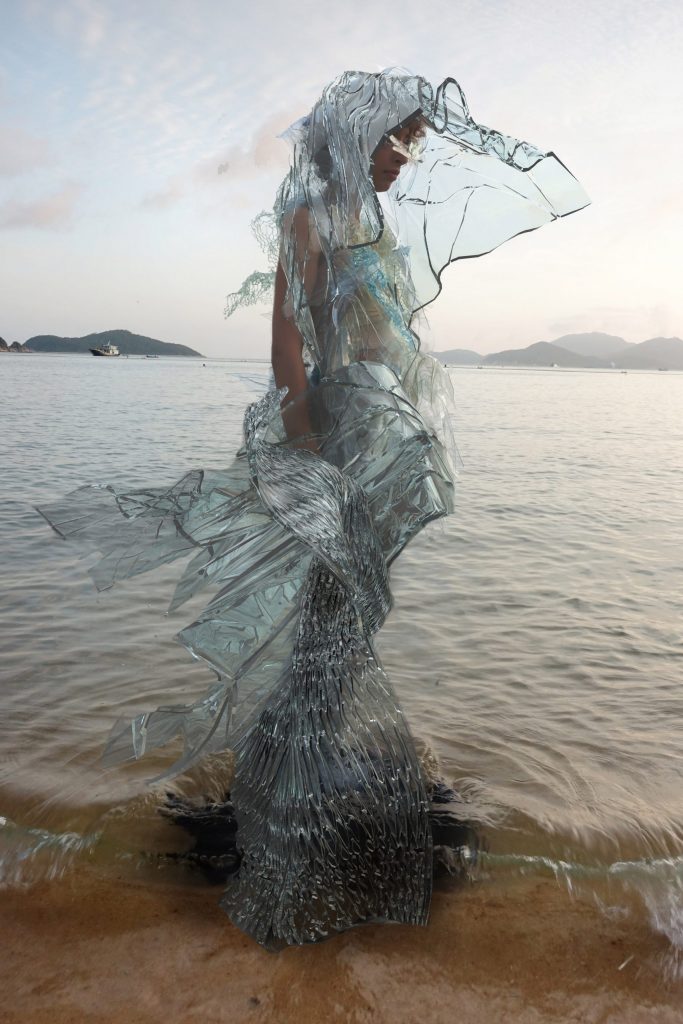
Decomposition of Materiality and Identities project by Scarlett Yang
To avoid an excess of material that would go to waste, the making process includes generative design used to create a 3D computer model of the textural shape that the material would take and digital fabrication of a casting mould using 3D-printing and laser-cutting technologies. The liquid biomaterial is then left in the mould to solidify.
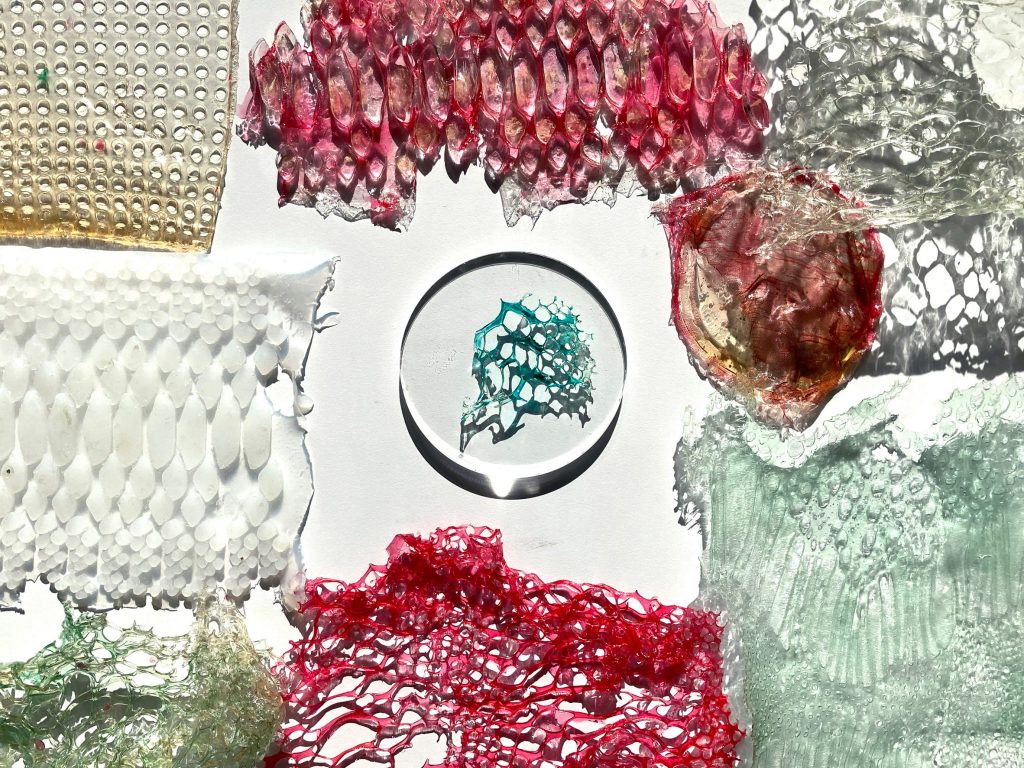
Decomposition of Materiality and Identities project by Scarlett Yang
A silk cocoon protein, known as sericin, is applied onto selective parts of the material. Due to its “hydrophobic” characteristics, the protein makes the material to crease and shrink, changing shape of the dress in response to different humidity and temperature levels. During a dry winter, for instance, the garment would stiffen and look more sculptural. In this way, the glass-like garment displays the beauty of natural life forms.
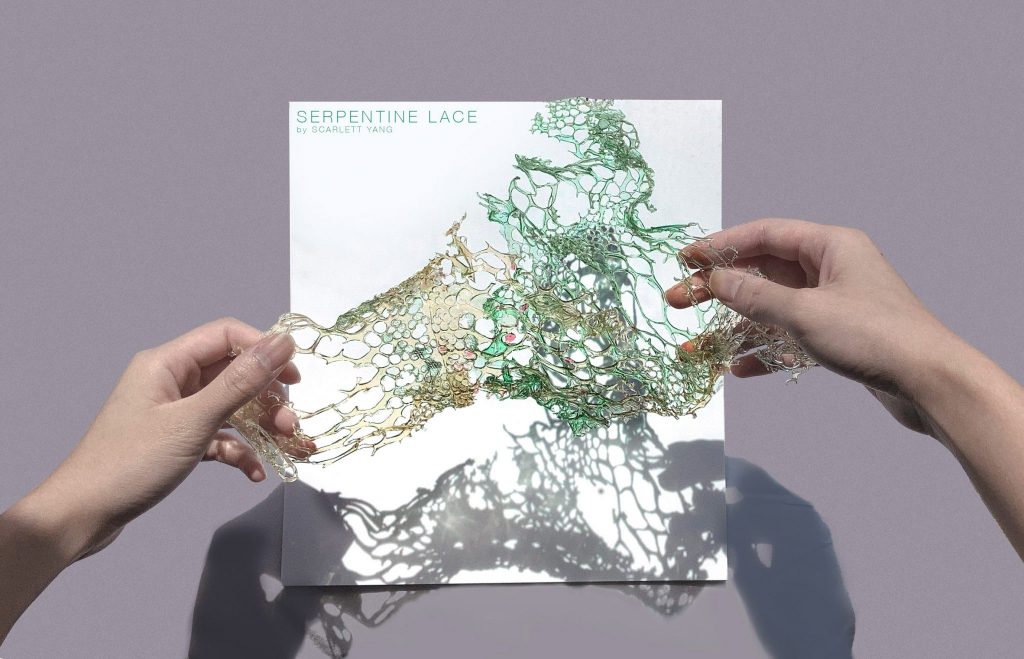
Decomposition of Materiality and Identities project by Scarlett Yang
According to the designer, sericin she uses is saved from European and Asian traditional silk production plants, where it would otherwise end at a landfill as a refuse in the textile manufacturing.
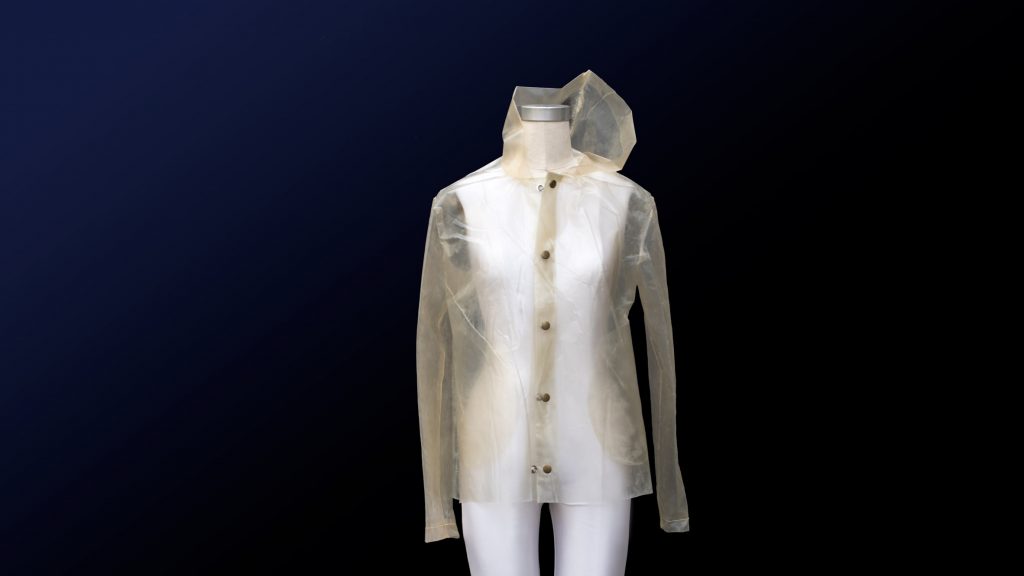
After Ancient Sunlight by Charlotte McCurdy
New York designer and the Rhode Island School of Design graduate Charlotte McCurdy has created a raincoat from a bioplastic entirely biopolymers derived from algae. This algae plastic is made of CO2 that has been drawn from the carbon reservoir of the atmosphere and put into the stock of carbon of our built environment.
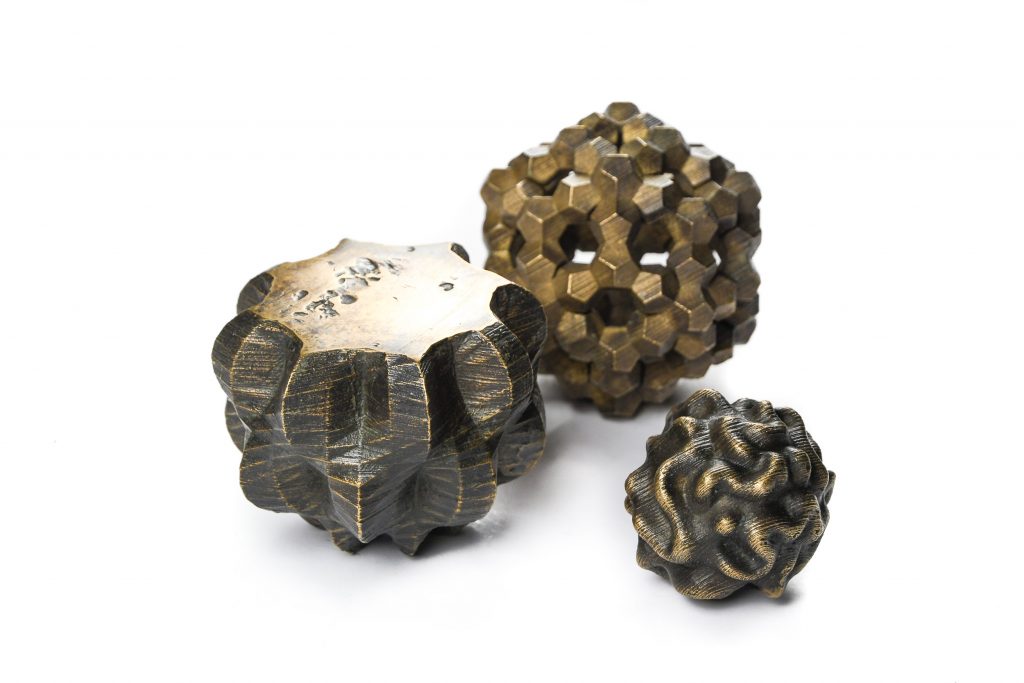
After Ancient Sunlight by Charlotte McCurdy
The algae are bound together by heat and poured into custom-made moulds where they are left to solidify. To improve its resistance to water, the bioplastic is covered with a thin coating of an entirely plant-based waterproofing wax. McCurdy developed the formula because everything available in the market was either petroleum-based, relying on paraffin, or not vegan, relying on beeswax.
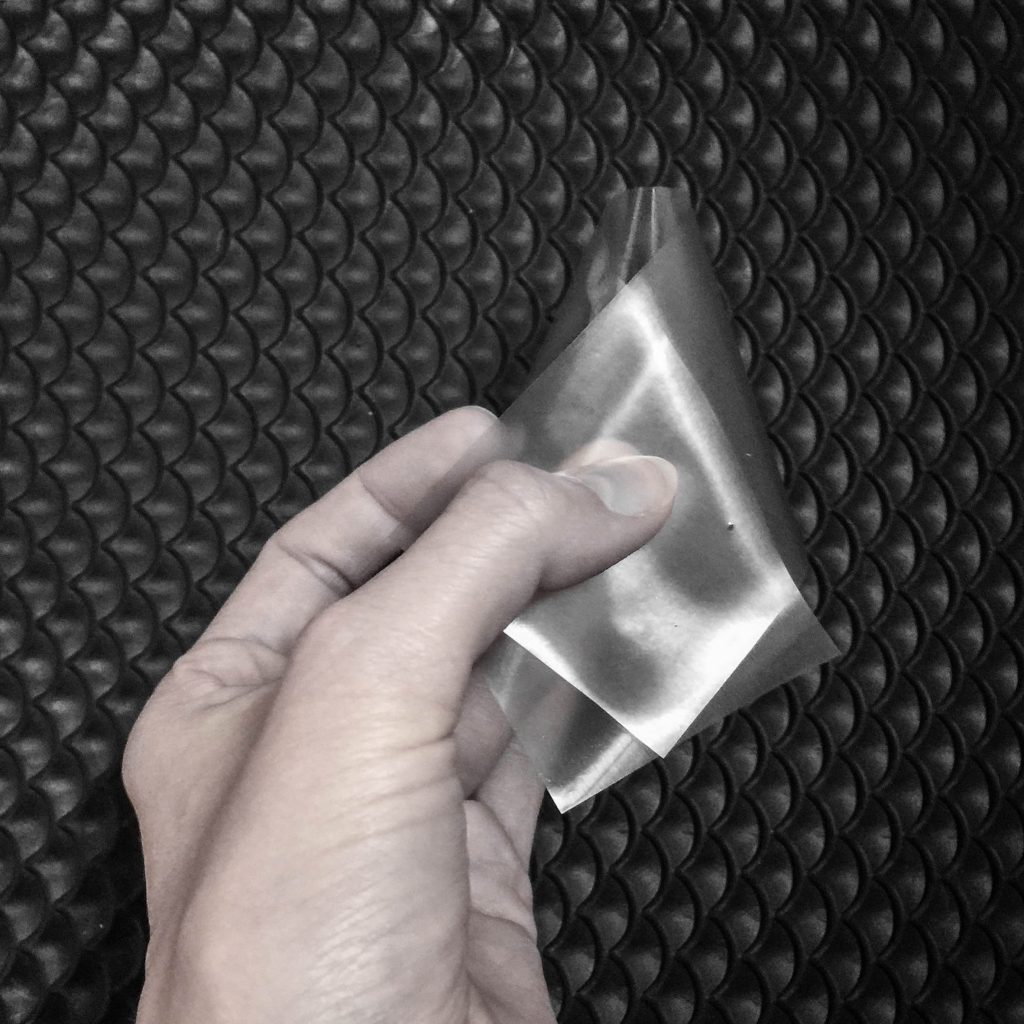
After Ancient Sunlight by Charlotte McCurdy
The sewing pattern is cut into the plastic while it is still in the mould, before being assembled into the finished product in the designer’s studio run on renewable electricity. All of the viscose threads and fasteners that bring the jacket together are also fossil-carbon-free.
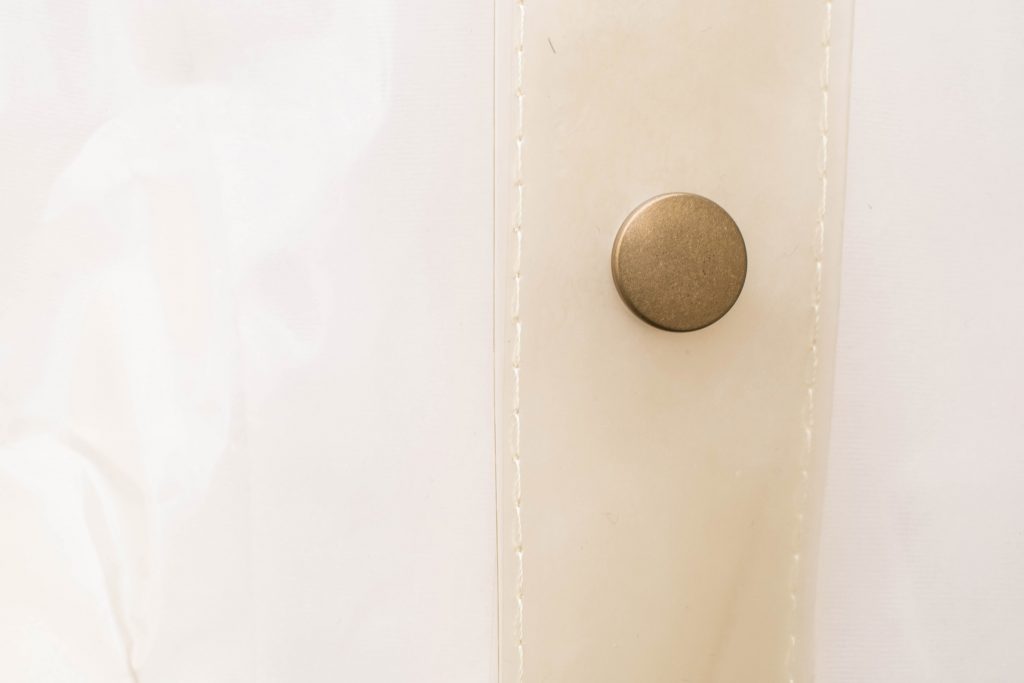
After Ancient Sunlight by Charlotte McCurdy
The project is called After Ancient Sunlight because much of our build environment is made of plastic, cement and steel, which are based on carbon molecules that were photosynthesised from sunlight by organisms millions of years ago. The designer believes that the future of materials is not about no longer using petroleum-based plastic, but rather about “totally rethinking the source of carbon we make our plastics out of”.
The raincoat also serves a more metaphorical function. It raises awareness of the fact that climate change is already manifesting itself in the form of increasingly extreme weather, while demonstrating that the technologies we need to fight the climate crisis are already available to us.
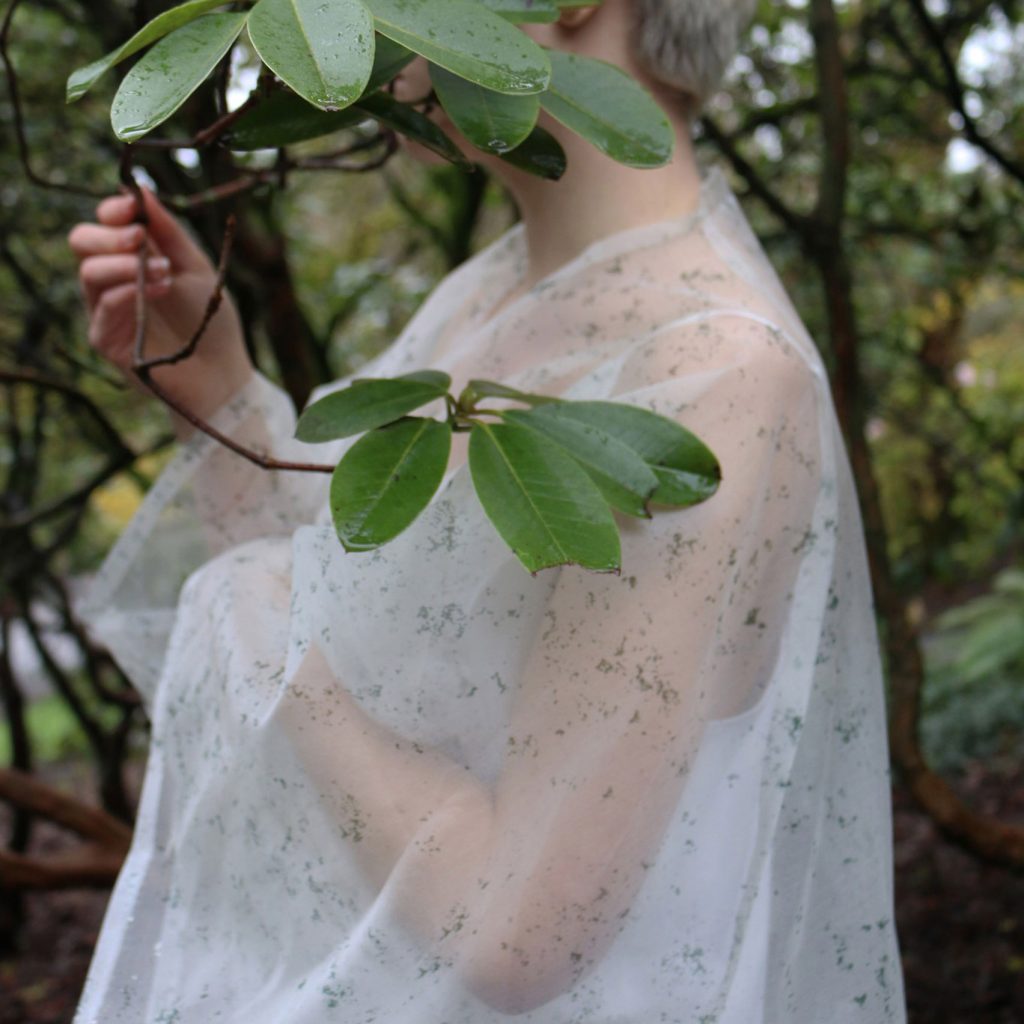
Biogarmentry by Roya Aghighi (also header image)
Created as a more sustainable alternative to fast fashion, Biogarmentry by Roya Aghighi, Canadian-Iranian designer in residence at Material Experience Lab in the Netherlands, is a collection of clothes made from algae that turn carbon dioxide into oxygen via photosynthesis. With the help of a group of scientists at the University of British Columbia, the designer created the first proof of concept for the survival of photosynthetic living cells on natural fabrics – such as different kinds of cellulose and protein based fibers.
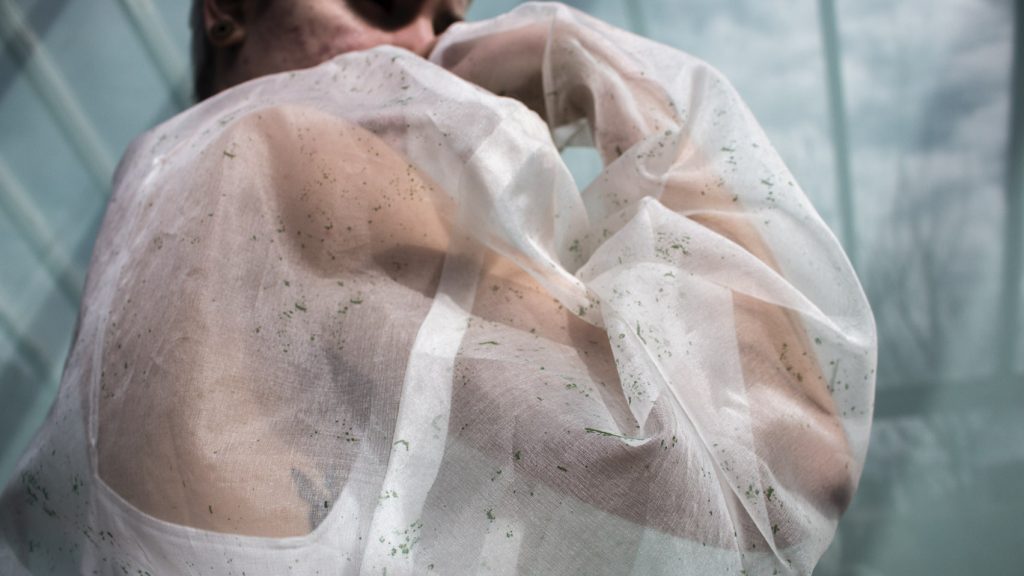
Biogarmentry by Roya Aghighi
To create the first non-woven biodegradable living textile capable of photosynthesis for Biogarmentry, Chlamydomonas reinhardtii, a type of single-cell green algae, are spun together with nano polymers. The resulting fabric, that resembles linen, is activated by being exposed to sunlight. Rather than wash their clothes, the owner would need to spray them with water once a week. By turning carbon dioxide into oxygen, the clothes improve the immediate environment of the wearer. Worn en masse, it could also help regulate carbon emissions.
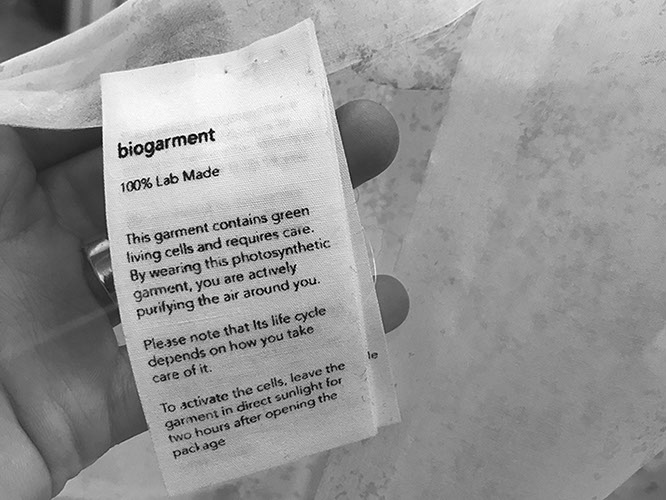
Biogarmentry by Roya Aghighi
Biogarmentry comes with exclusive care instructions in order to help the user keep their garment alive, which encourages a shift in our current perceptions of fashion and how we treat it. Currently the fabric is expected to live for about a month, however the life cycle of the living photosynthetic textile is directly dependent on how it is taken care of. According to Aghighi, by making textiles alive, users will grow emotionally attached to their garments.
After the user is finished with the garment, it could be disposed of via composting.