With concrete being one of the highest-consumed products but also accounting for billions of tons of carbon dioxide release, the industry has recognised the need for more sustainable practices to combat climate change and preserve natural resources. Rather than just mitigating concrete’s negative environmental impact, material researchers set out to create bio-based substitutes, which are derived from renewable resources found in nature and offer a greener alternative to traditional construction materials.
As part of the Maison/0 graduate programme by the LVMH group,Central Saint Martins graduates Brigitte Kock and Irene Roca Moracia have created concrete-like tiles made from Japanese knotweed and shells from American signal crayfish. Annually removal and incineration of these non-native species, which are among the top five threats to biodiversity worldwide and are causing the most ecological and economic damage in the UK, costs the government around £1.8 billion.
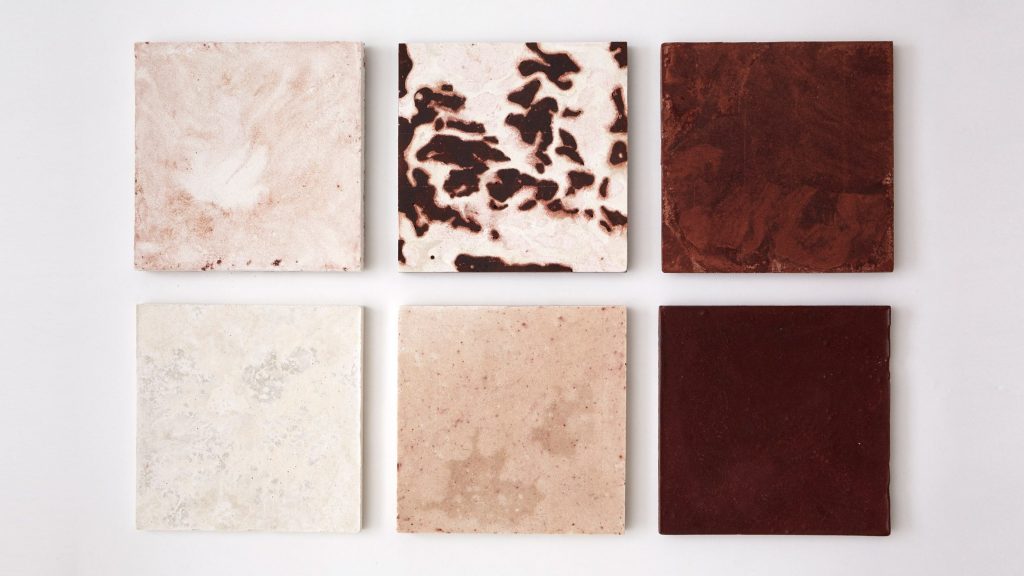
Bio-concrete tiles by Brigitte Kock and Irene Roca Moracia
Japanese knotweed was introduced to the UK in the 1800s and has no natural enemies in the country. When left unchecked, it can grow through concrete, compromising the structural integrity of buildings and roads. Similarly, since they started being imported to the UK in the 1970s, American signal crayfish have decimated the native crayfish population.
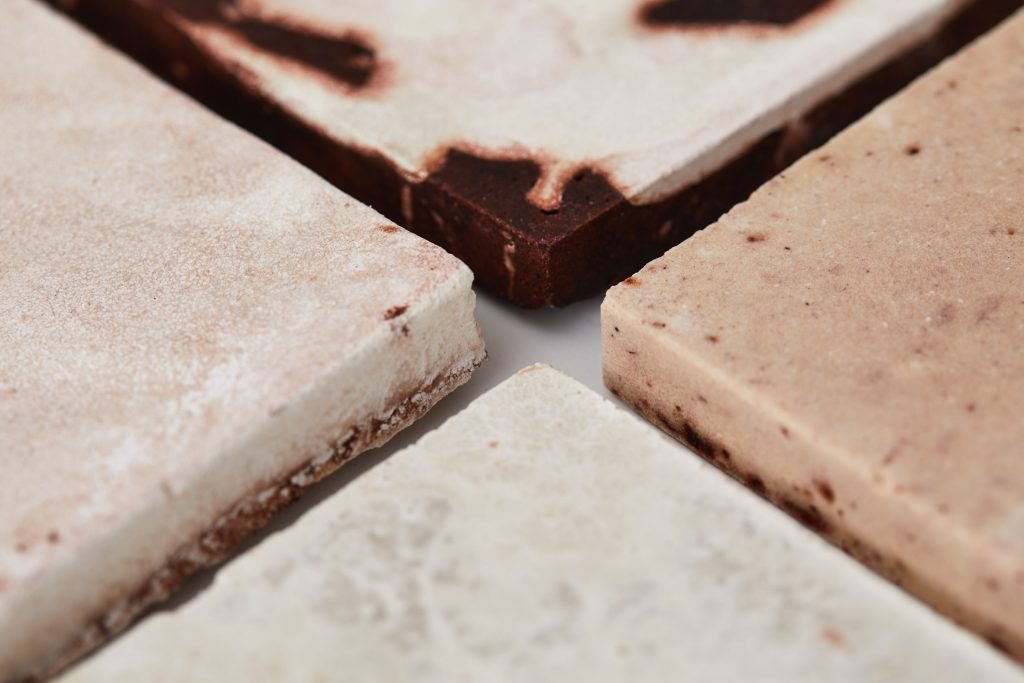
Bio-concrete tiles by Brigitte Kock and Irene Roca Moracia
Rather than having the invasive species labelled as hazardous waste, the duo has found a way to integrate them into a production process so that they create economic as well as ecological benefits.
The researchers sourced both species from specialist removal companies. The knotweed, which is incinerated after removal, acts as the ash binder, while pulverised crayfish shells are used as the aggregate, following the principles developed by the ancient Romans, who utilized a recipe based on the volcanic ash concrete.
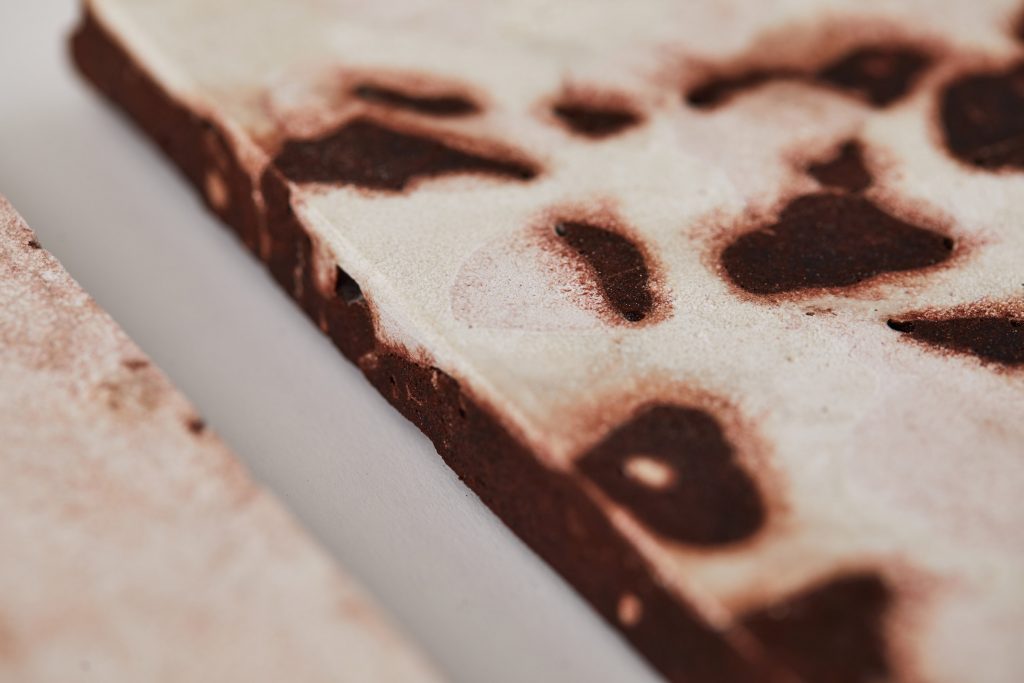
Bio-concrete tiles by Brigitte Kock and Irene Roca Moracia
Combined with water and gelatine, these ingredients create a strong, homogenous material that cures and hardens without the need for added heat. The final colours and textures depend on the curing time and the aggregate’s chemical reactions with the binder and the water.
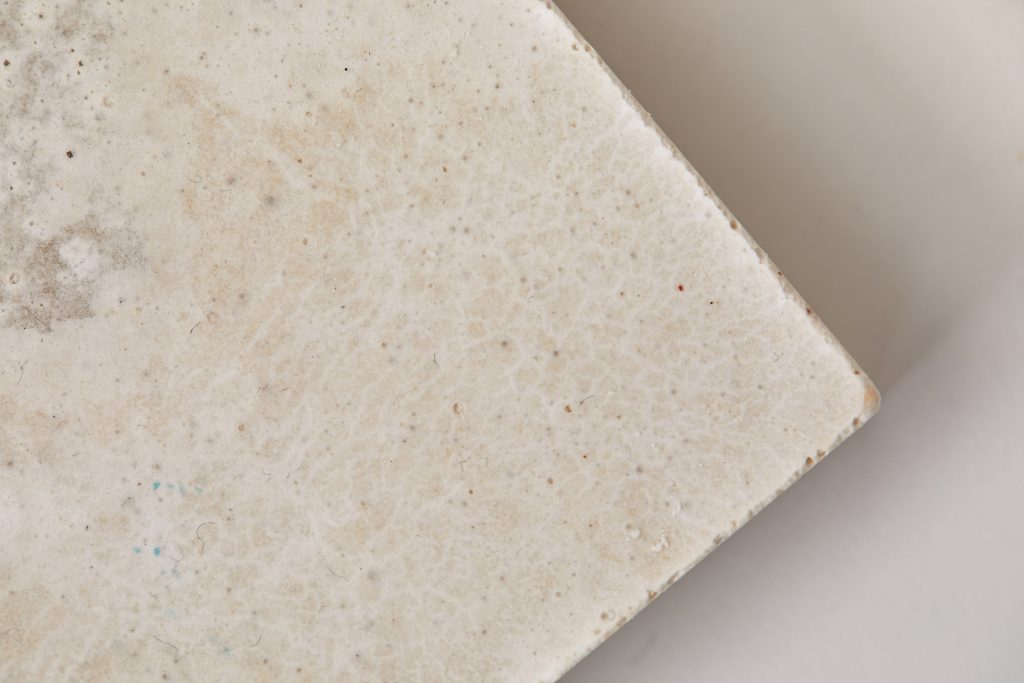
Bio-concrete tiles by Brigitte Kock and Irene Roca Moracia
Through adjusting these variables, the material can replicate various finishes including raw concrete or delicate marble and range in colour from a pale green developed in firing the crayfish shell to a deep burgundy created by including raw knotweed root in the curing process.
The mixture can then be cast into any shape, which the researchers hope would allow it to be used for commercial use.
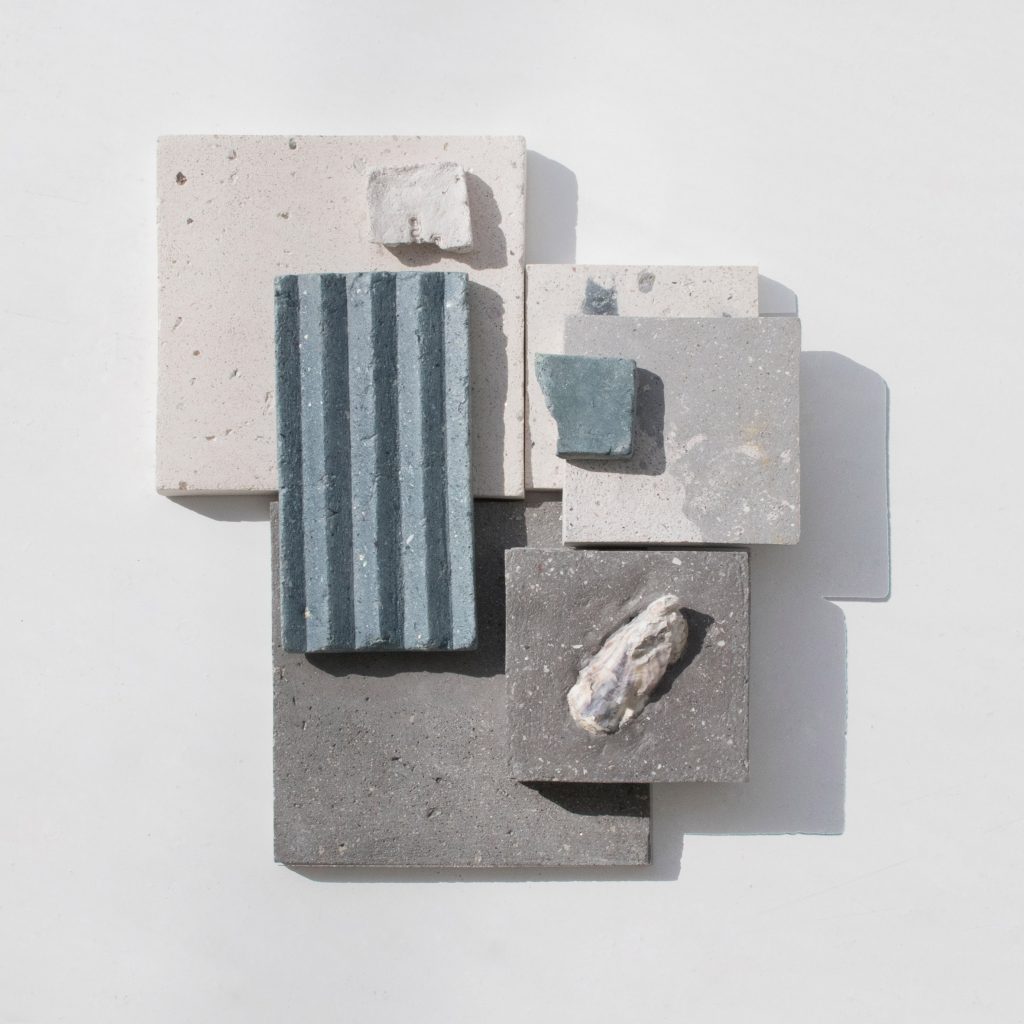
Sea Stone by Newtab-22 (also header image)
Aiming to help alleviate the issue of waste in the seafood industry, which results in seven million tonnes of seashells discarded every year, innovation agency Newtab-22 based in London and Seoul has developed Sea Stone, a zero-waste concrete-like material made from by-products of the seashell salvaged from the seafood and aquaculture industries.
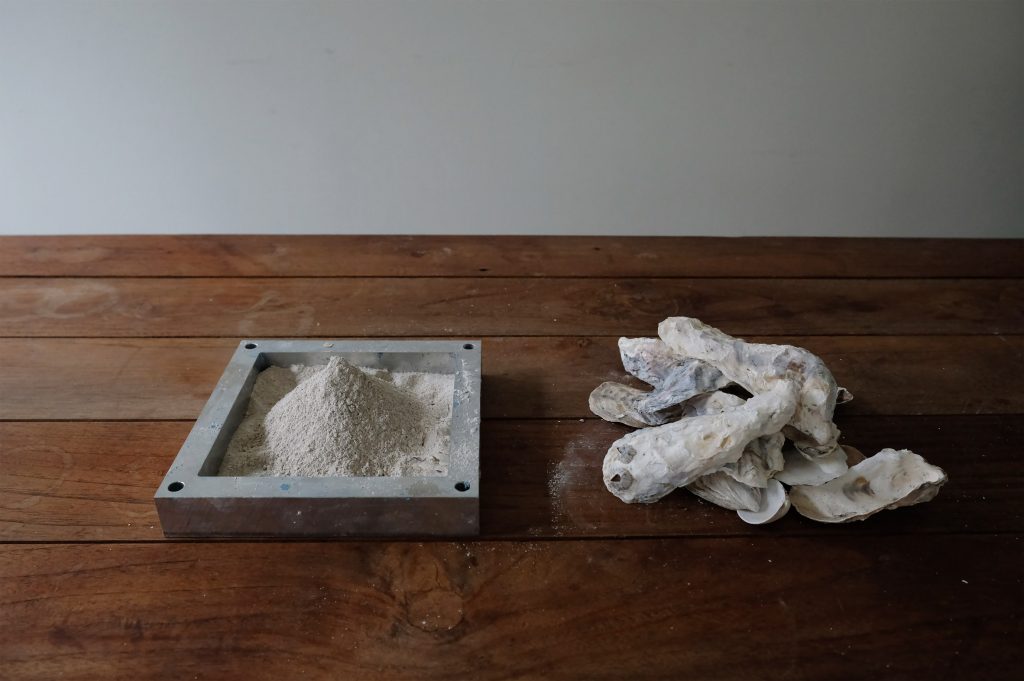
Sea Stone by Newtab-22
The concrete-like material is comprised by ground shells and natural, non-toxic and sustainable binders, including sugar and agar, and features plastic hardness and aesthetic terrazzo-like texture. The process of making Sea Stone involves adding the mixture to a mould and leaving it to solidify into concrete-like pieces. This method is currently carried out manually to avoid the use of heat, electricity and chemical treatments.
It results in variations in the sizes, textures and colours of the shell fragments and means that each piece of Sea Stone is unique. Differences can also occur by altering the quantities of shells and binders, or by adding coloured dyes.
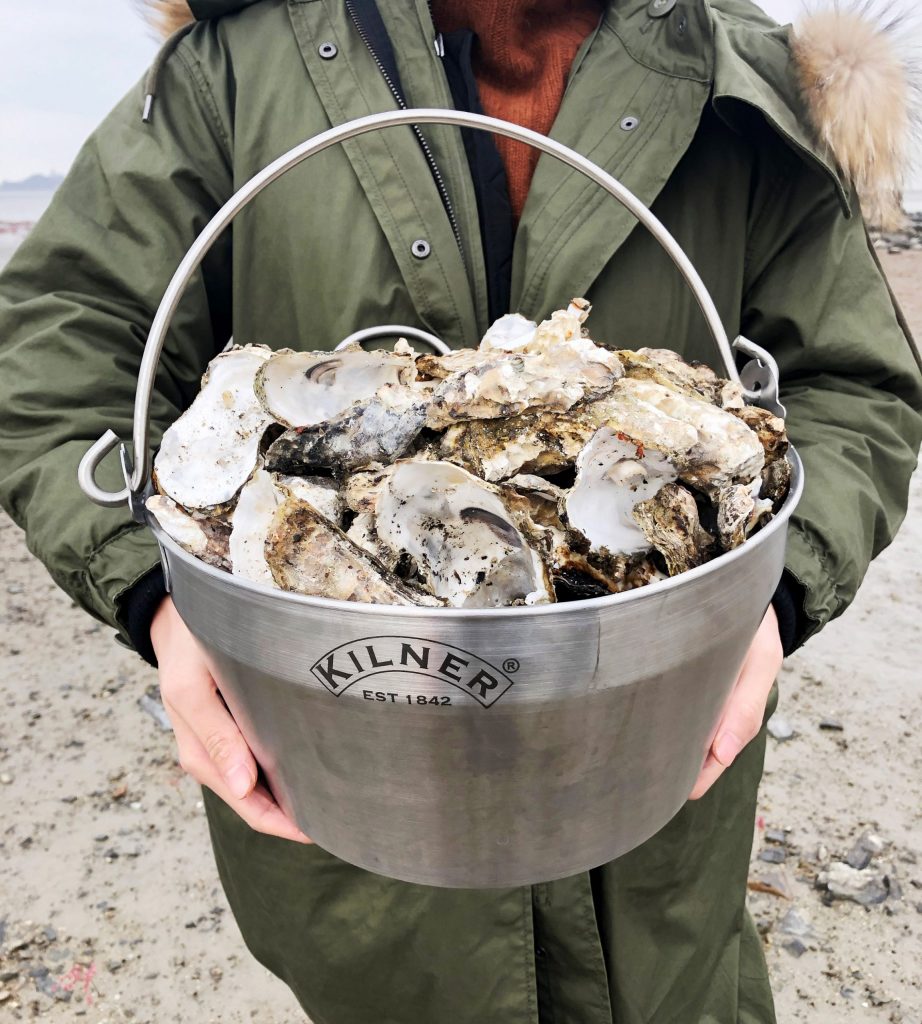
by Newtab-22
Because seashells are rich in calcium carbonate, otherwise known as limestone, which is used to make cement, the two materials share similar properties. This makes Sea Stone a sustainable alternative to concrete in the design of small-scale products. The material has so far been used to make products such as decorative tiles, tabletops, plinths and vases.
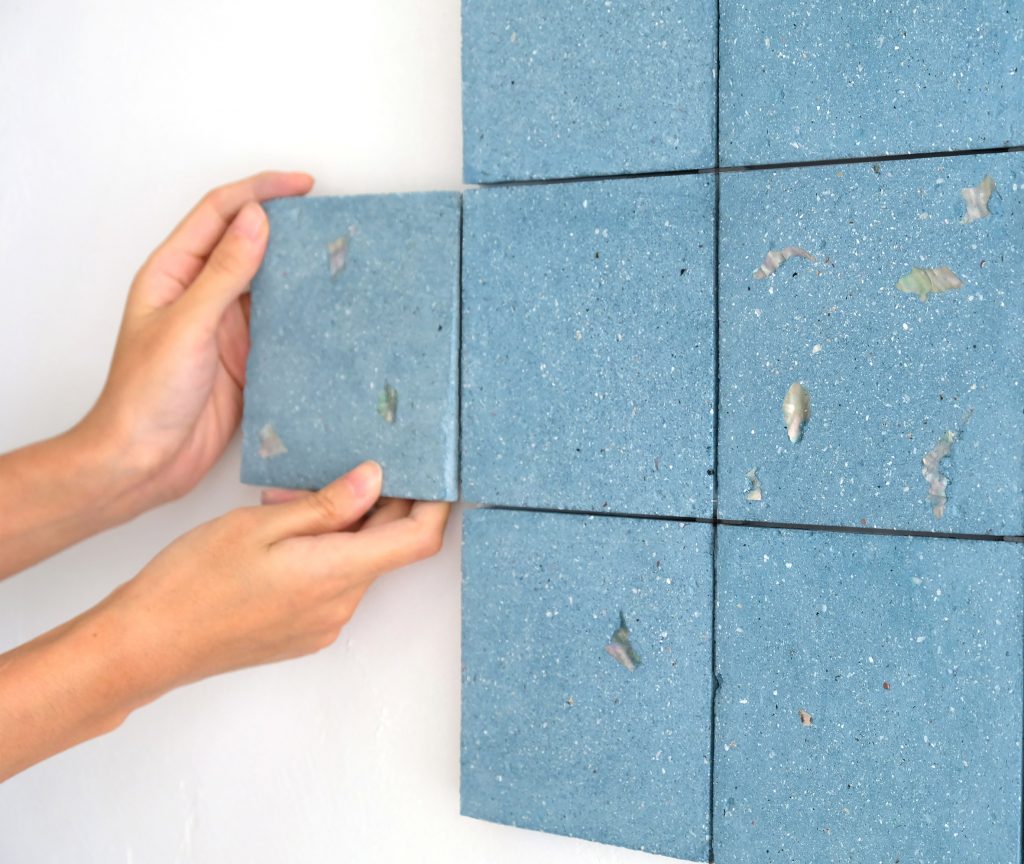
Sea Stone by Newtab-22
The team deliberately do not want to use Sea Stone for large-scale or structural projects. This is because to truly replicate the strength of traditional concrete required in large-scale projects like buildings, an energy-intensive heating process would be required, which accounts for half of all the CO2 emissions that result from using concrete and would therefore lead to secondary pollution.
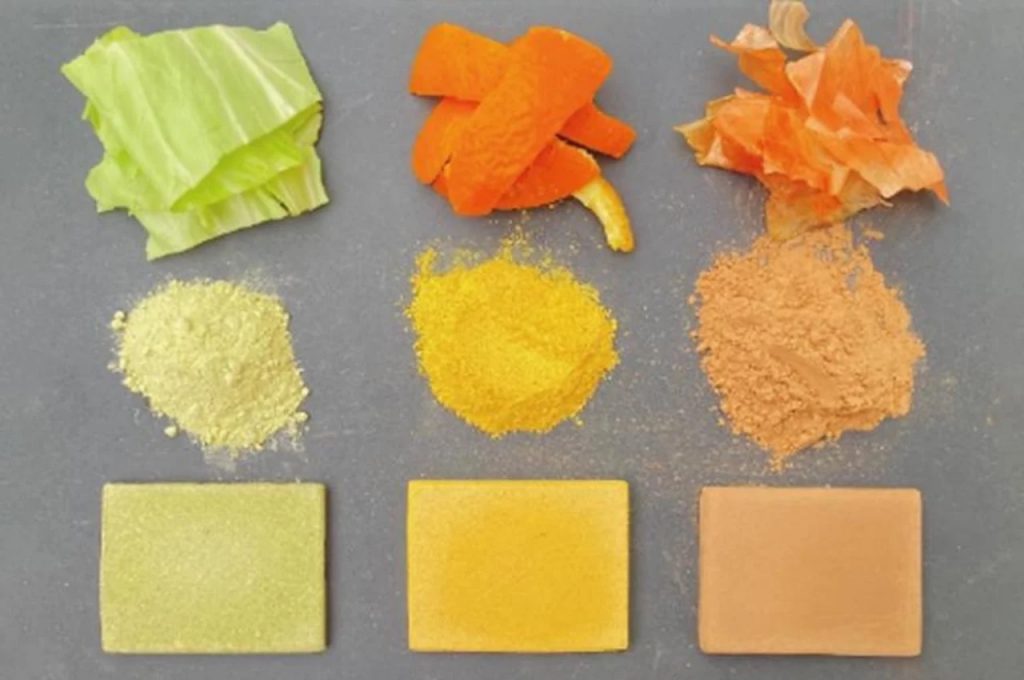
Edible concrete by University of Tokyo
A group of scientists at University of Tokyo creates bio-concrete from food waste like coffee grounds, banana peels, Chinese cabbage, and orange skins. The organic material are dried and mixed with water and seasonings, before being compressed in a high-temperature mould.
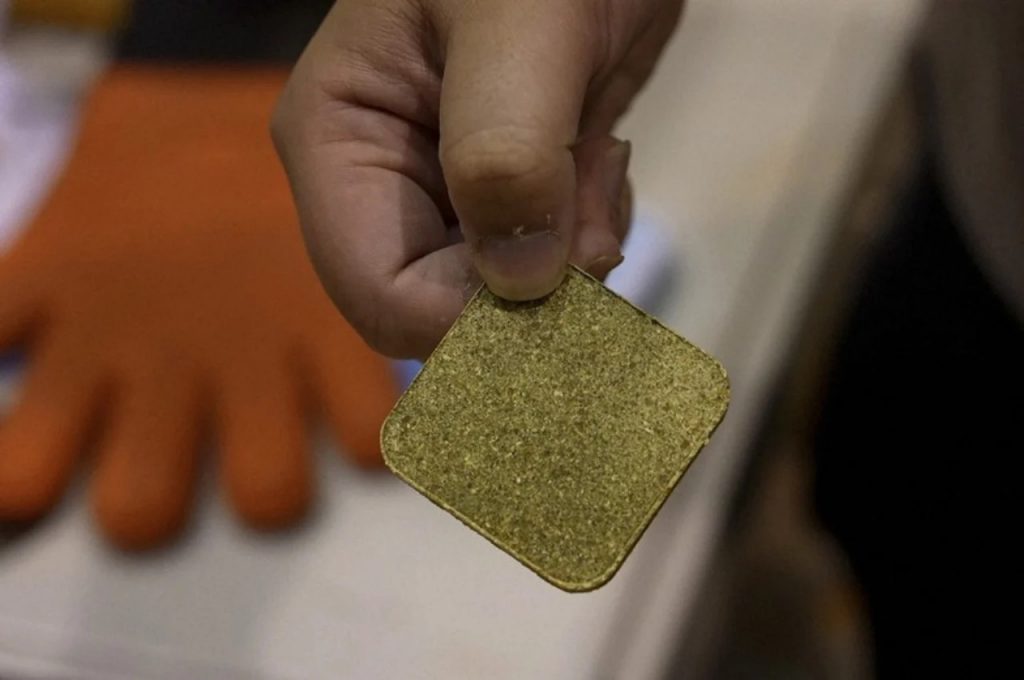
Edible concrete by University of Tokyo
The resulting concrete-like material is three times stronger than actual concrete and has better bending strength. It can also resist rot, funghi, and insects. In fact, the bio-concrete is edible too, although that is probably not the most delicious thing to consume.
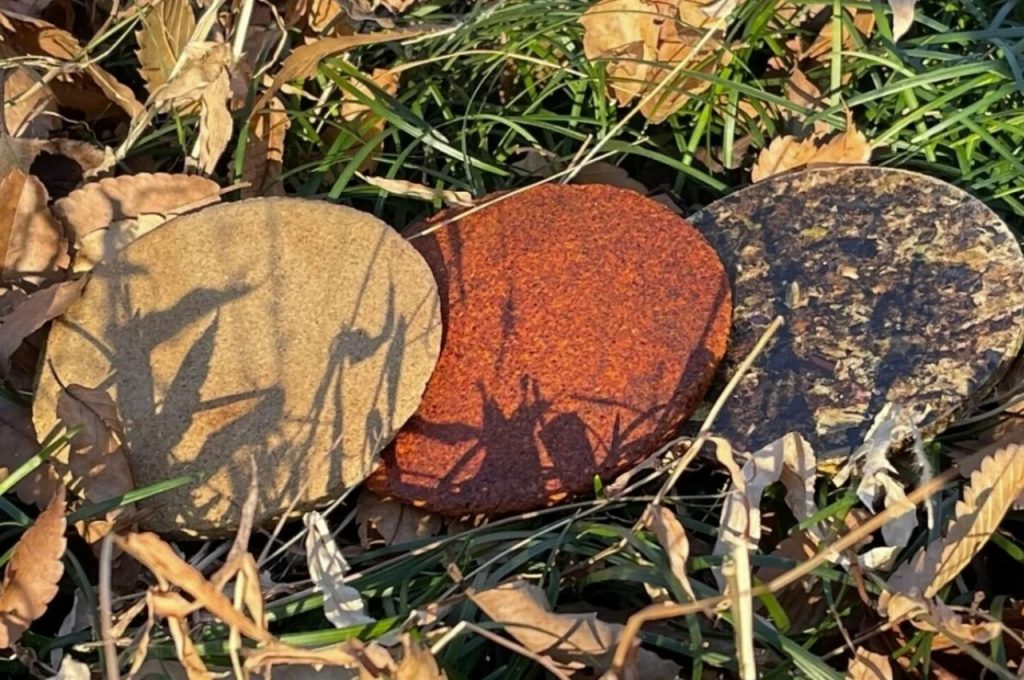
Edible concrete by University of Tokyo