About 22 billion pairs of shoes are manufactured globally each year, the production process emitting enormous amounts of carbon dioxide, enough to contribute about 1.5 percent of the world’s greenhouse gas emissions. Taking the term carbon ‘footprint’ rather too literally, product designers want to reduce impact brought about by production of shoes. Made out of plant-based materials, these shoes designs are biodegradable and do not introduce any chemicals to the earth when they are thrown away.
While conventional shoes often contain leather, rubber, and plastic, all of which have a high carbon impact, the Lace-Up sneakers from the sustainable footwear manufacturer Kengos are med up from corn, rubber, eucalyptus, and cork.
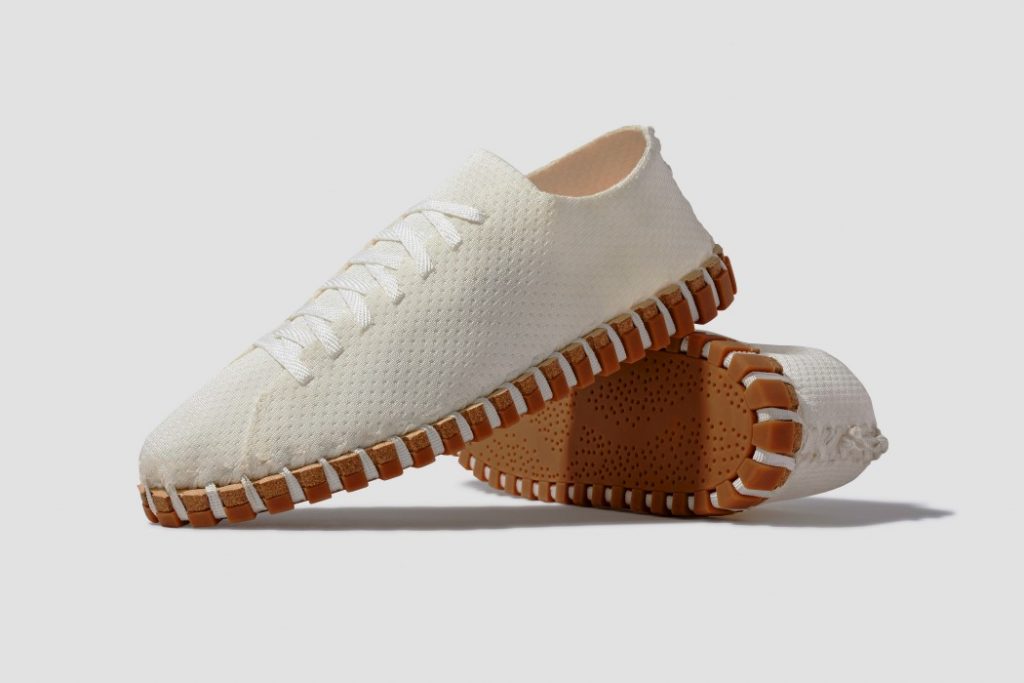
Kengos Lace-Up by Dave Costello & Micah Heftman (also header image)
The company claims that the unique shoes are 98% natural and plant-based, making it environment-friendly and vegan-friendly. The sustainable materials define the unique appearance of the sneakers.
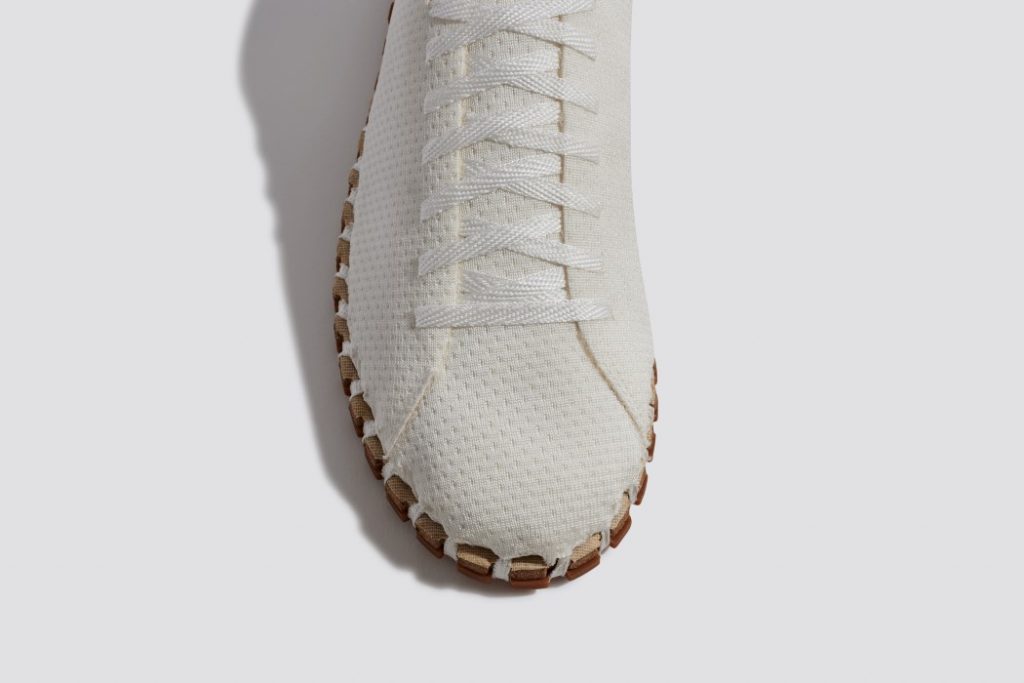
Kengos Lace-Up by Dave Costello & Micah Heftman
The upper body of the shoe is manufactured from Amaize, a corn-based fabric, and lined with eucalyptus fabric on the inside, which allows the sneakers to regulate temperature and absorb sweat. The midsole is made usinh cork, which molds to the shape of one’s foot almost like a foam insert, while the outsole is crafted from Kengos’ patent-pending Pure-Flex rubber, which is durable as a work-boot, but biodegrades nearly 35-times as fast.
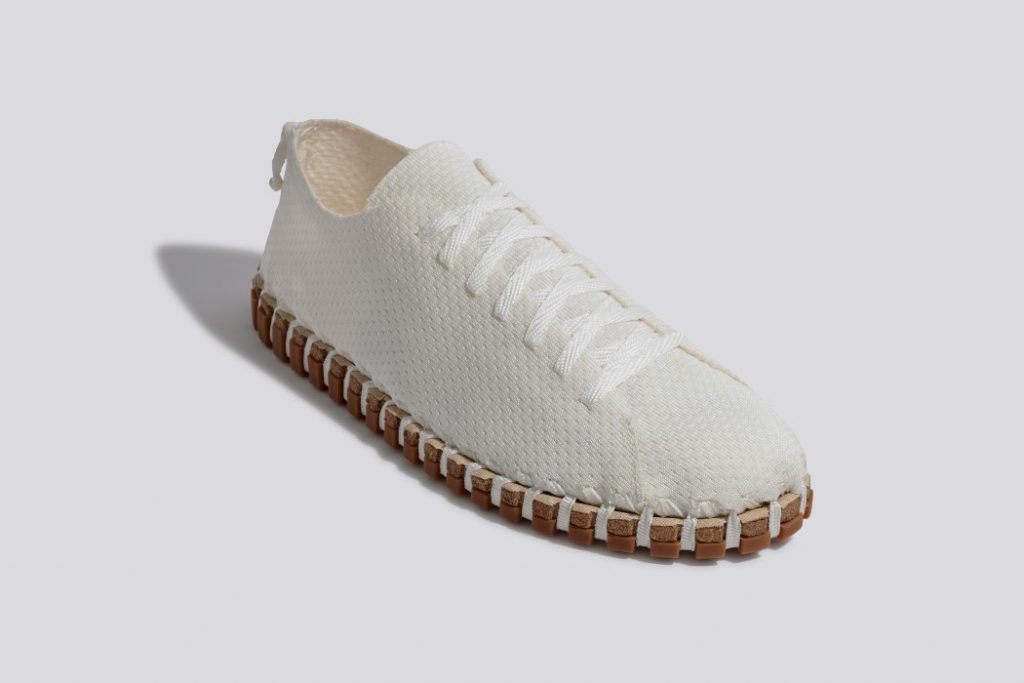
Kengos Lace-Up by Dave Costello & Micah Heftman
The material palette used by Kengos to produce their sustainable Lace-Up’s includes also such innovative plant-based leather alternatives as cactus leather and mushroom leather.
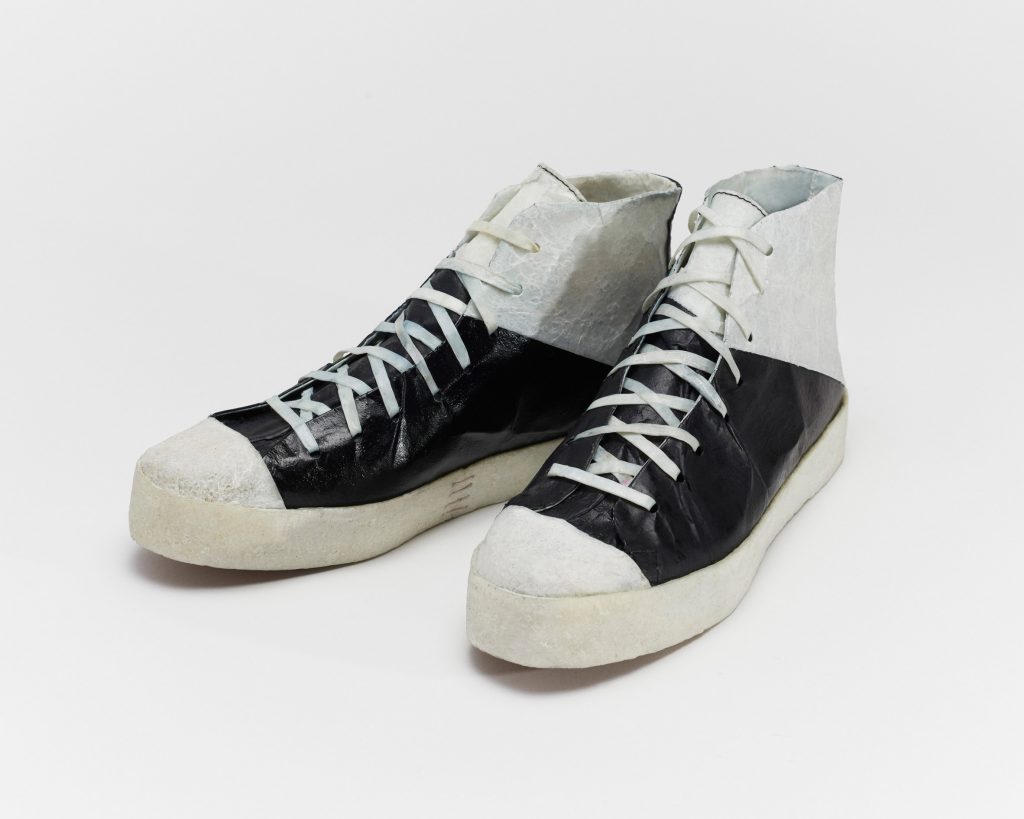
SCOBY shoes by Theanne Schiros and Public School
The leather substitute SCOBY developed by material scientist Theanne Schiros in scientific partnership with researchers from Columbia University’s Materials Research Science and Engineering Center and used by New York streetwear label Public School to create a pair of biofabricated trainers is literally grown by microbes.
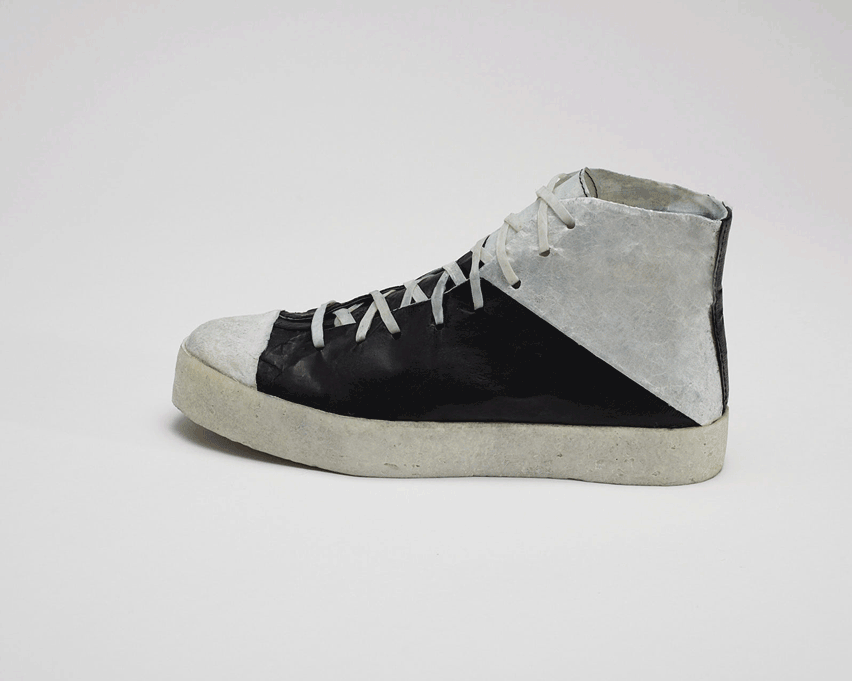
SCOBY shoes by Theanne Schiros and Public School
The name of the material used to produce almost the entire trainer, including the upper, midsole and laces, – SCOBY – is actually an acrobym standing for a symbiotic culture of bacteria and yeast, which is a key ingredient in making kombucha tea.
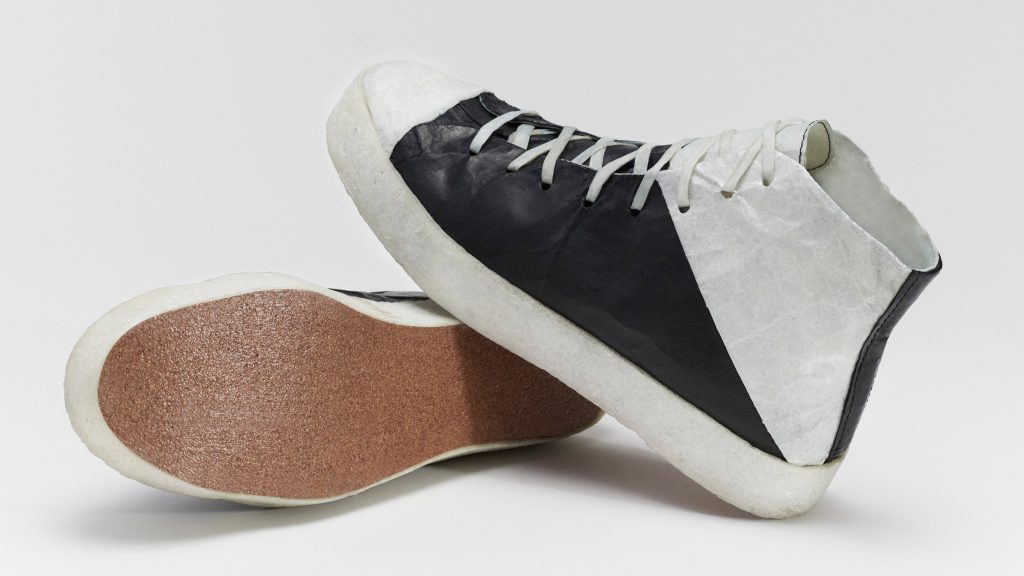
SCOBY shoes by Theanne Schiros and Public School
The team claims that through fermentation, the SCOBY creates a leather substitute that has up to a 97 per cent lower carbon footprint than synthetic polyurethane (PU) leather. The bio-leather has a lifespan of several years, after which it will take about 60 days to break down in a domestic compost heap, returning s nutrients for a healthy ecosystem. Unless buried in a microbe-rich environment, the bio-leather maintains its durability and performance aside from normal wear and tear, comparable to canvas and leather.
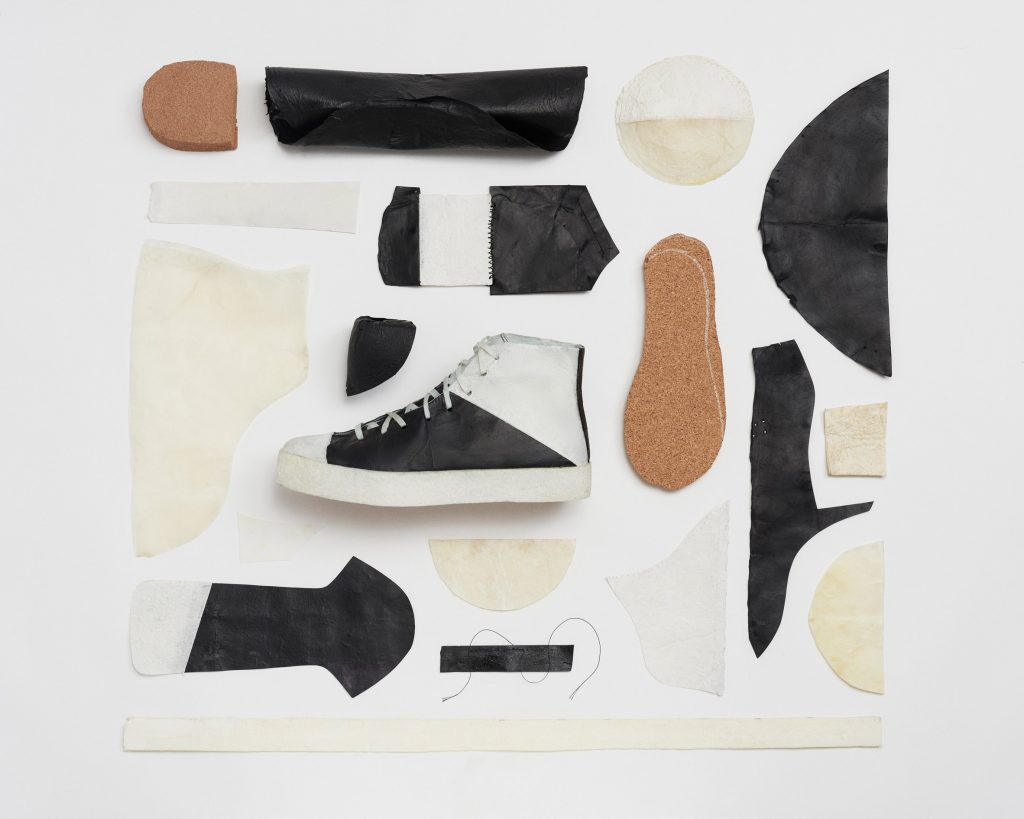
SCOBY shoes by Theanne Schiros and Public School
To biofabricate the trainers’ leather, the material scientist puts the SCOBY into a base of sweetened tea, where it turns the sugar into bacterial nanocellulose (BNC) as part of the fermentation process. To achieve the desired deep, opaque black, she combines indigo pigment, derived from the leaves of the titular shrub, with a binder of fresh soy milk.
The material is then dried in a mould, which eliminates the textile waste associated with traditional pattern cutting. From here, Brooklyn-based shoemaker Anne Marika Verploegh Chassé assembles the trainer using traditional leather moulding techniques. According to the team, the process could be scaled up for commercial production.
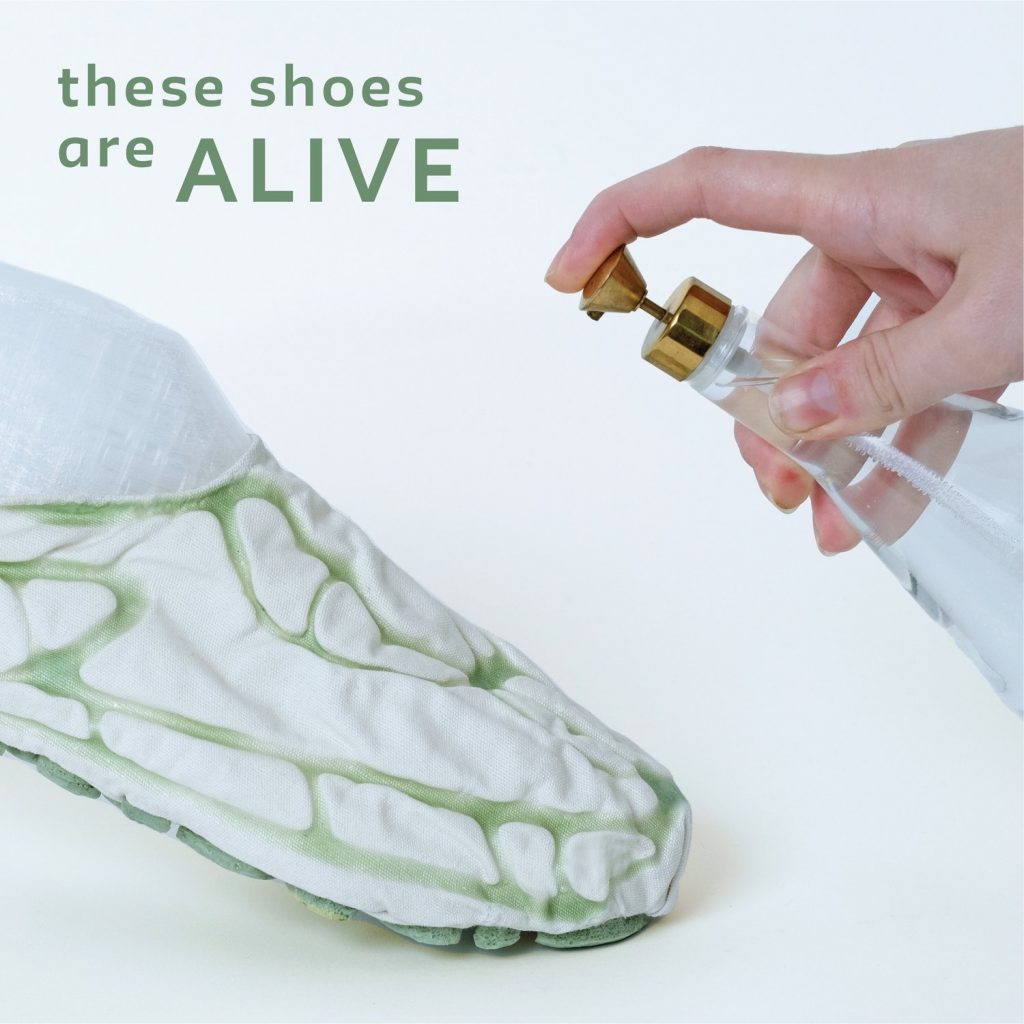
Synthiesis by Jessica Thies
Even though sustainable materials have become a significant part of the production process, the industry still needs a revolutionary idea that can help considerably decrease carbon emissions.
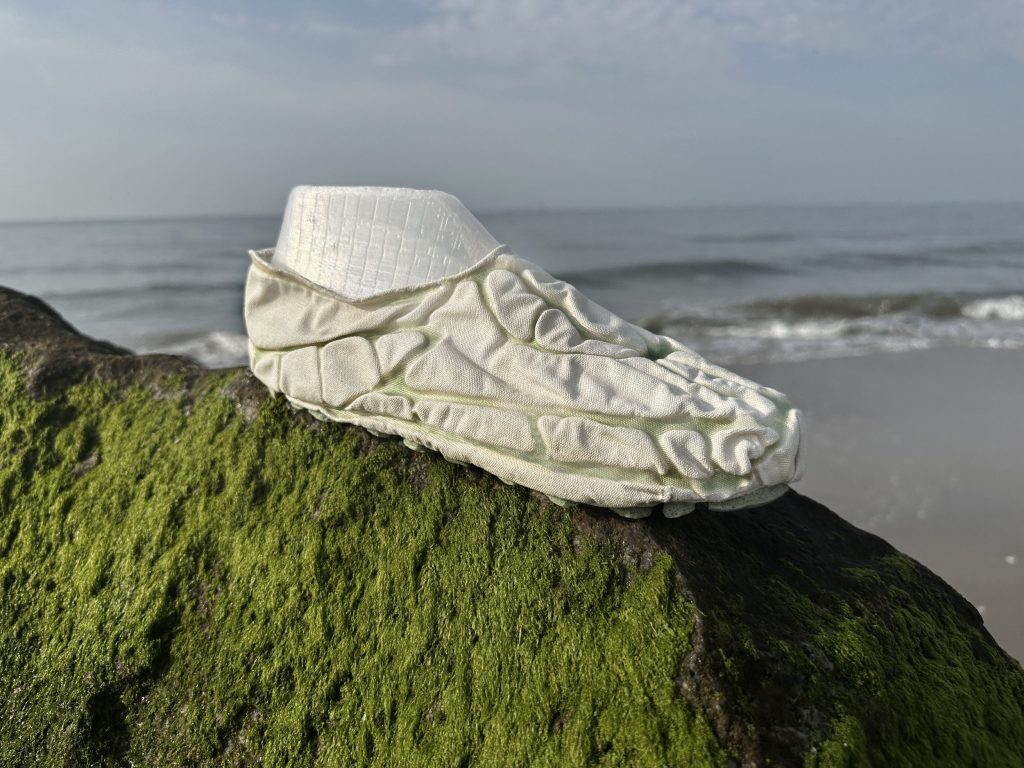
Synthiesis by Jessica Thies
New York based designer and material researcher Jessica Thies believes that merely replacing bio-based materials with synthetic ones won’t help us address the he core issues of over-consumption and exploitation of the natural world. She has developed a pair of concept shoes that is capable of acting like a living organism.
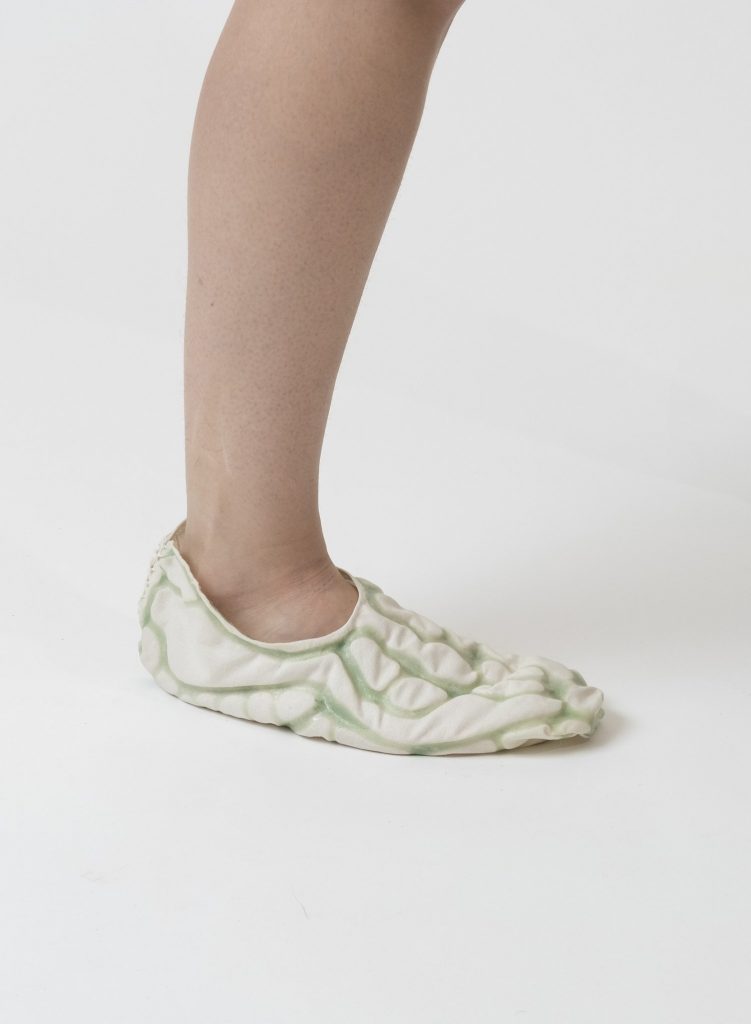
Synthiesis by Jessica Thies
Dubbed Synthiesis, the concept shoes are made from hemp fabric and printed with bio-based ink included with algae that can absorb carbon dioxide from the surroundings and potentially be able to self-clean.
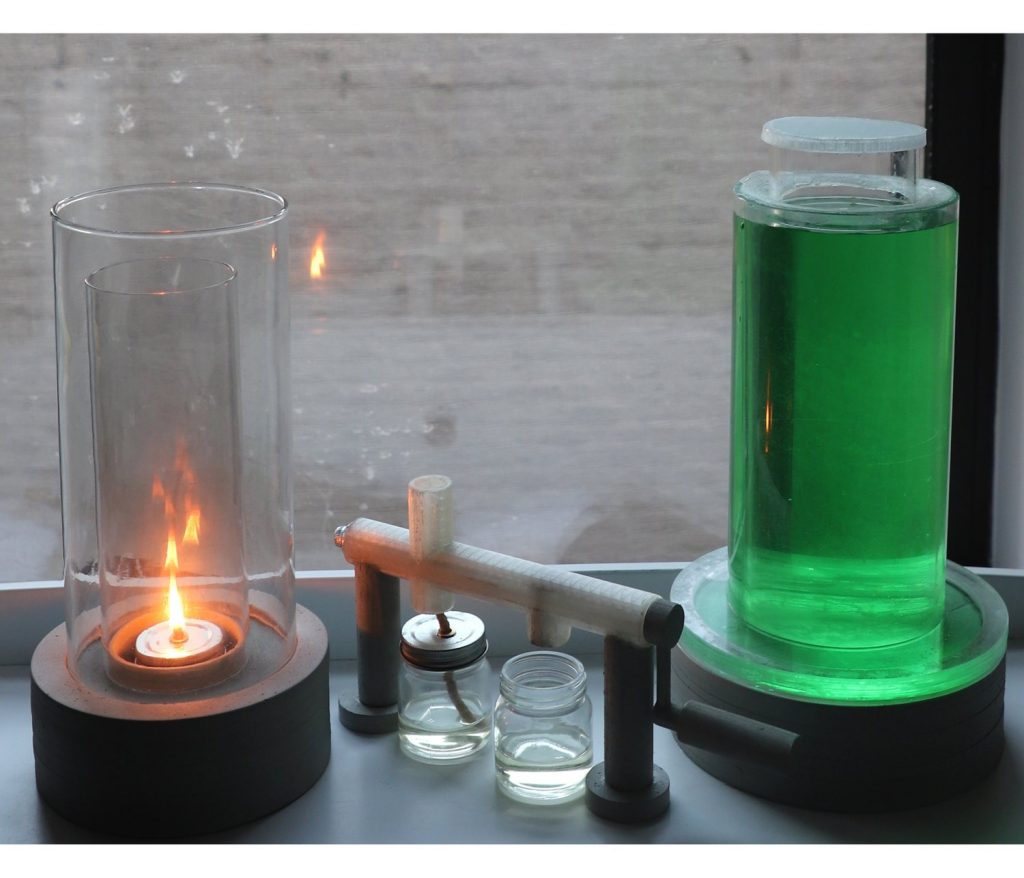
Synthiesis by Jessica Thies
The project is based on the designer’s research into engineered living materials and is part of her thesis at Parsons School of Design. The research affirms that the algae used in the construction can survive a month without supplementary nutrients, and if cared for, it can last much longer – feeding on nutrients and oxygen-producing cyanobacteria using hydroponics, in a manner we grow plants.