On the one hand, tableware is a mundane thing that serves as a background for the food we consume. On the other hand, it can affect your dining experience. Studies have shown that your tableware material can enhance the taste or detract from the flavor. The items in this selection are not what they look like at first sight, and sure enough they will influence your perception of taste.
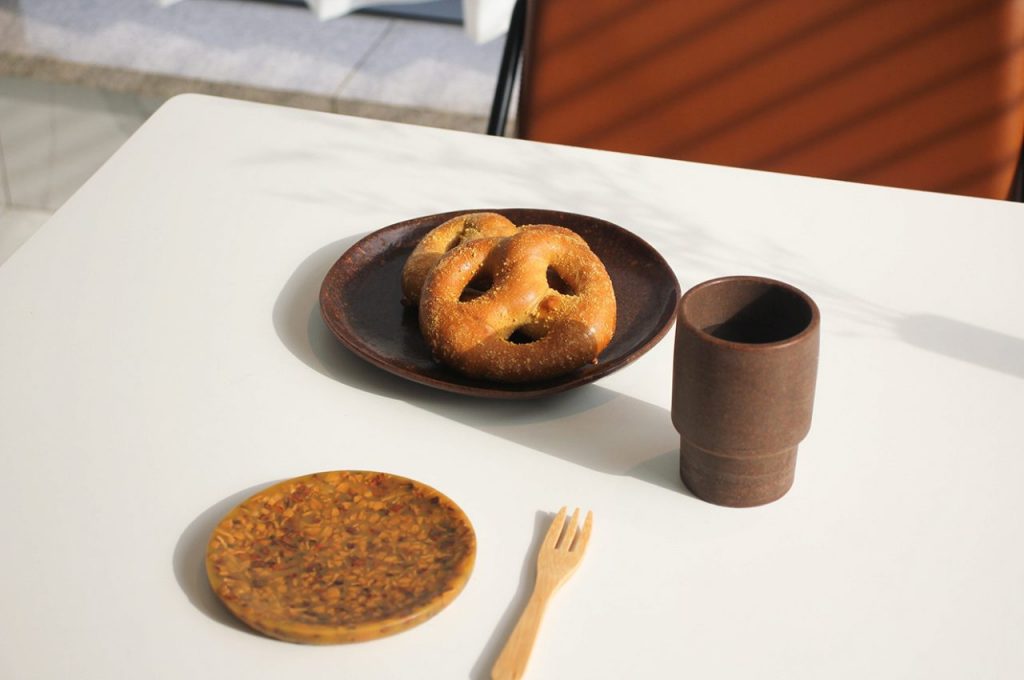
NOS by SooA Choi
Korean designer SooA Choi created a 100% natural material as an alternative to ceramics for manufacturing tableware like small and large plates, glasses, vases, etc. Boasting diverse colours, patterns and light transmission, the material named NOS is produced by mixing enormous volumes of ground walnut shells, which are otherwise considered waste and discarded, with pine resin that serves as a binding agent.
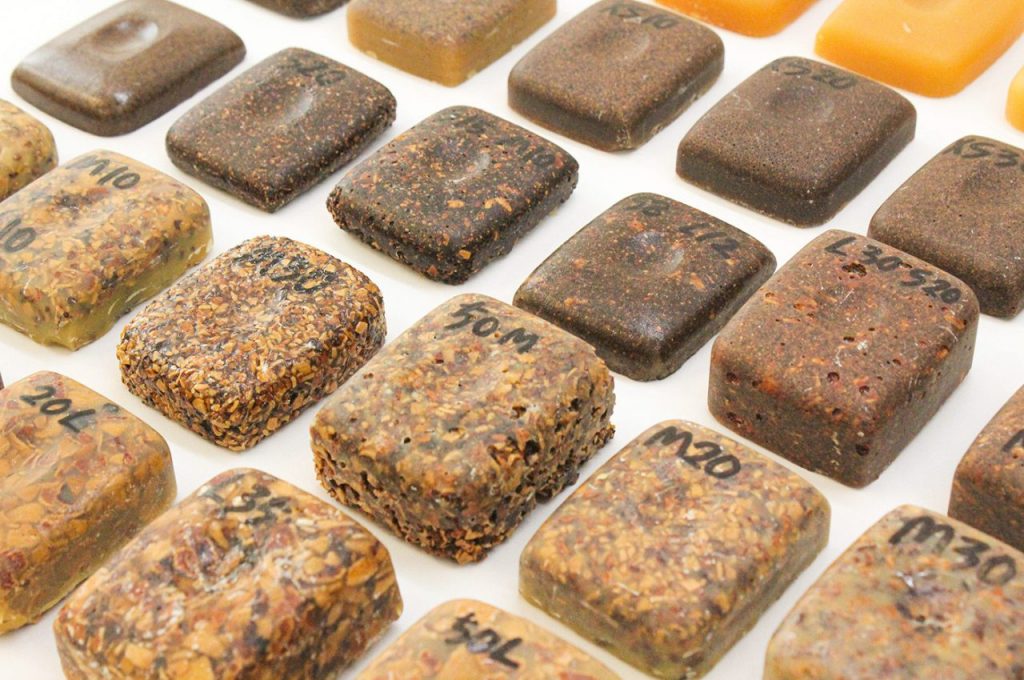
NOS by SooA Choi
The manufacturing technique for NOS is quite simple and highly sustainable. Ground walnut shells are mixed with the appropriate ratio of binders and this substance is then poured into a mold to produce the required shape. The completed form removed from the mold is fired at a high temperature of over 400 degrees to apply the glaze, after which Carnauba wax is poured onto it to increase durability and prevent scratches.
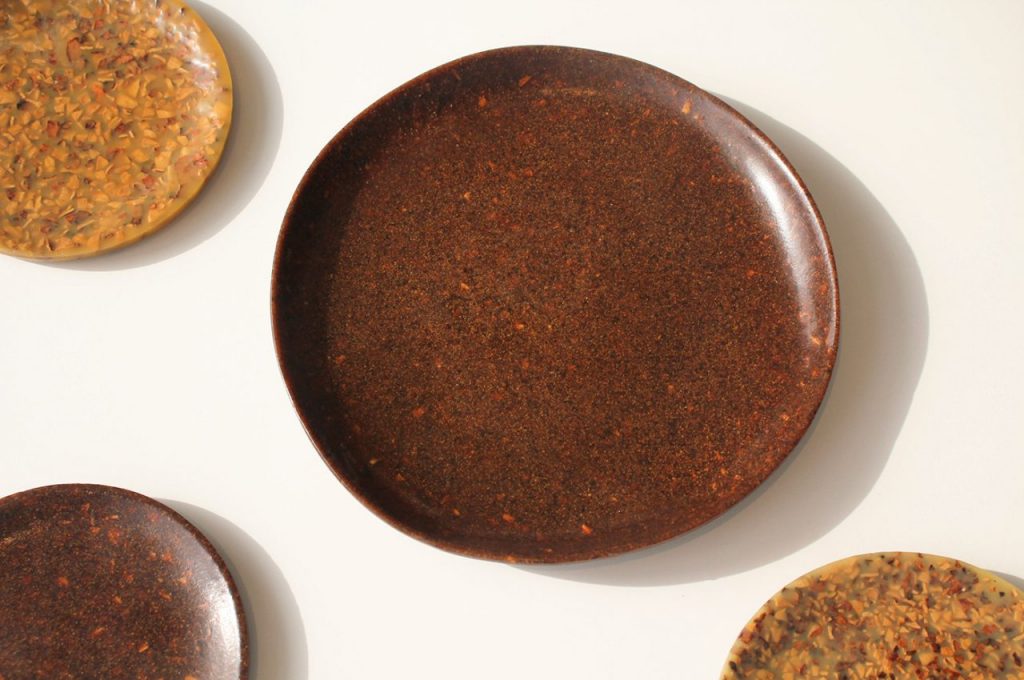
NOS by SooA Choi
Walnut shells are dry and hard, which works to their benefit since it stops insects from entering via holes and crevices, and it also makes them almost odorless. Pine resin is tree sap that is naturally antimicrobial and safe to consume in tiny doses. However, the soldering of pine resin is hazardous to one’s health and should be avoided during the manufacturing of NOS.
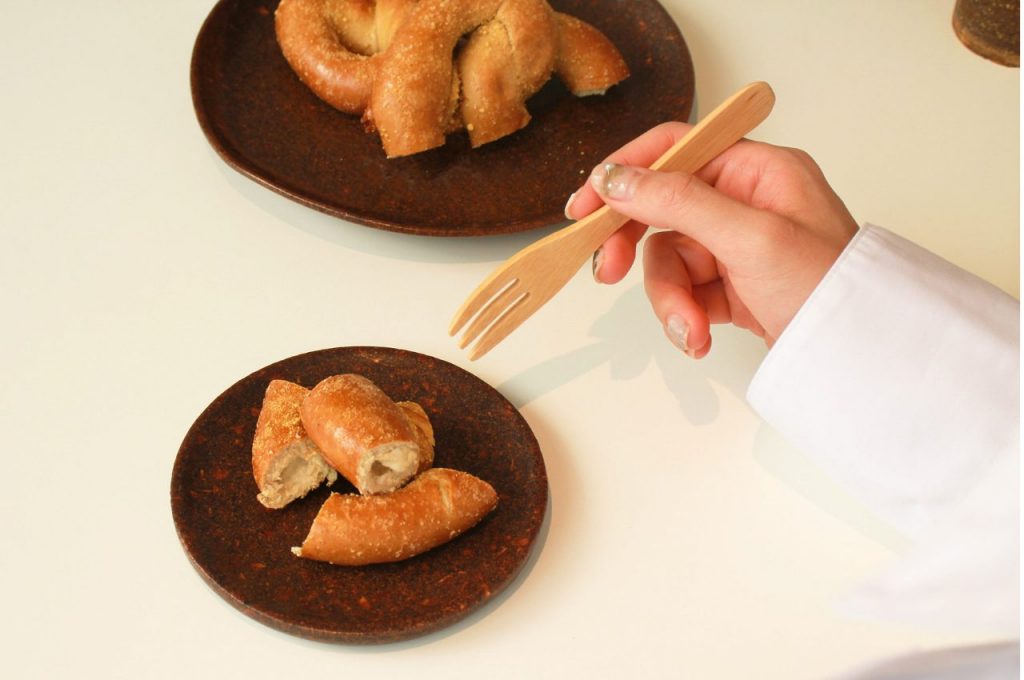
NOS by SooA Choi
Dry and hard, walnut shells are more durable than many other natural materials, which wear away with frequent use. In many everyday situations, the qualities of a walnut shell are similar to those of wood.
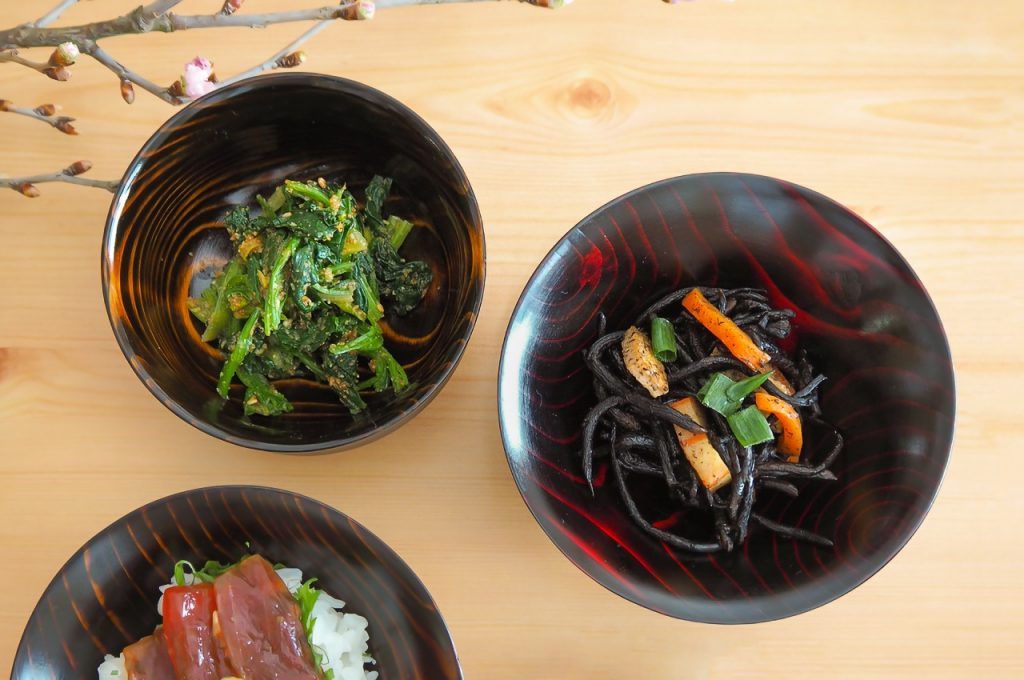
Higashi Shunkei Lacquer Ware
Wood can be a great material to create tableware too. It is not as fragile as ceramics, and has better heat-retention properties, wooden plates and bowls can be washed and reused for decades. Given that wooden is a naturally occurring material, it is sustainable, eco-friendly, and renewable.
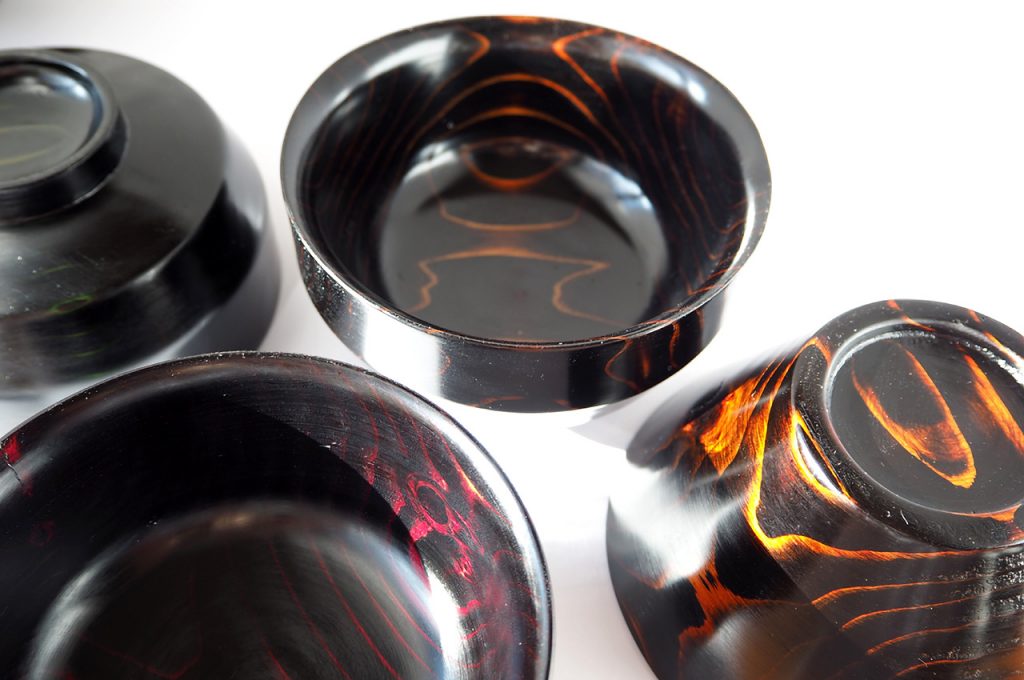
Higashi Shunkei Lacquer Ware
Higashi Shunkei has been spreading the message of wooden tableware for 68 years. Founded in Hida Takayama in Japan, the three-generation-old company had humble beginnings as chopstick makers, moving onto larger tableware including bowls made from cedarwood native to the city of Takayama in Gifu prefecture. The tiny city is famous for its forests, where Higashi Shunkei sources their cedarwood from.
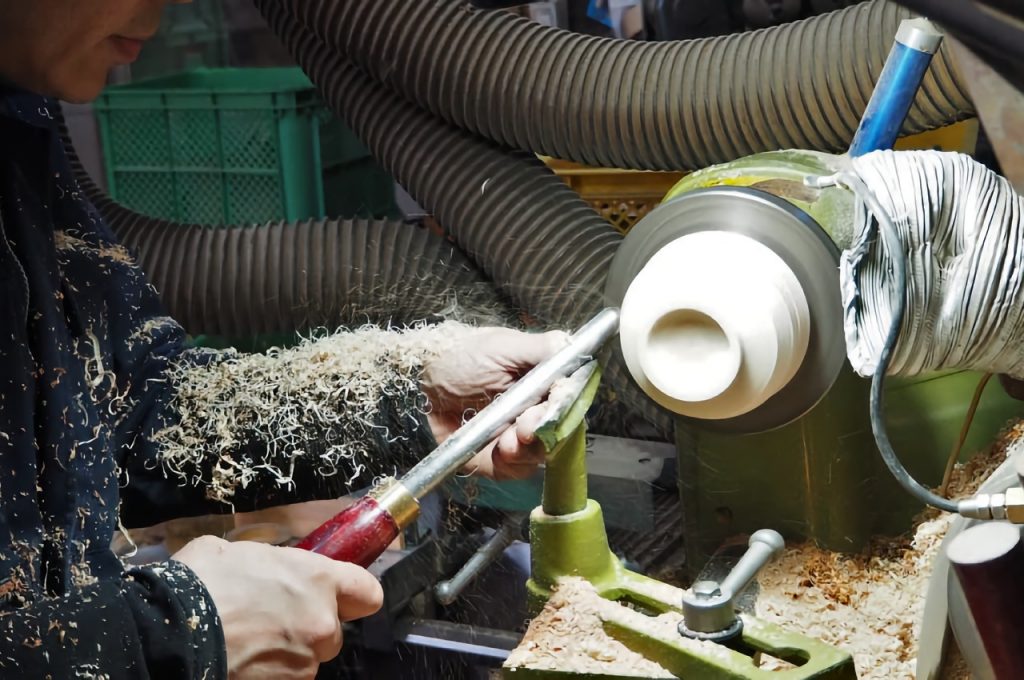
Higashi Shunkei Lacquer Ware
The Hida-Cedar bowls are spun on a wooden lathe, finished, and lacquered using a traditional process called Suri Urushi, in which the bowl gets multiple coats of lacquer – all within Higashi Shunkei’s own workshop. The more lacquer is applied, the stronger the wood becomes. The resulting bowls feel as dense and glossy as ceramic.
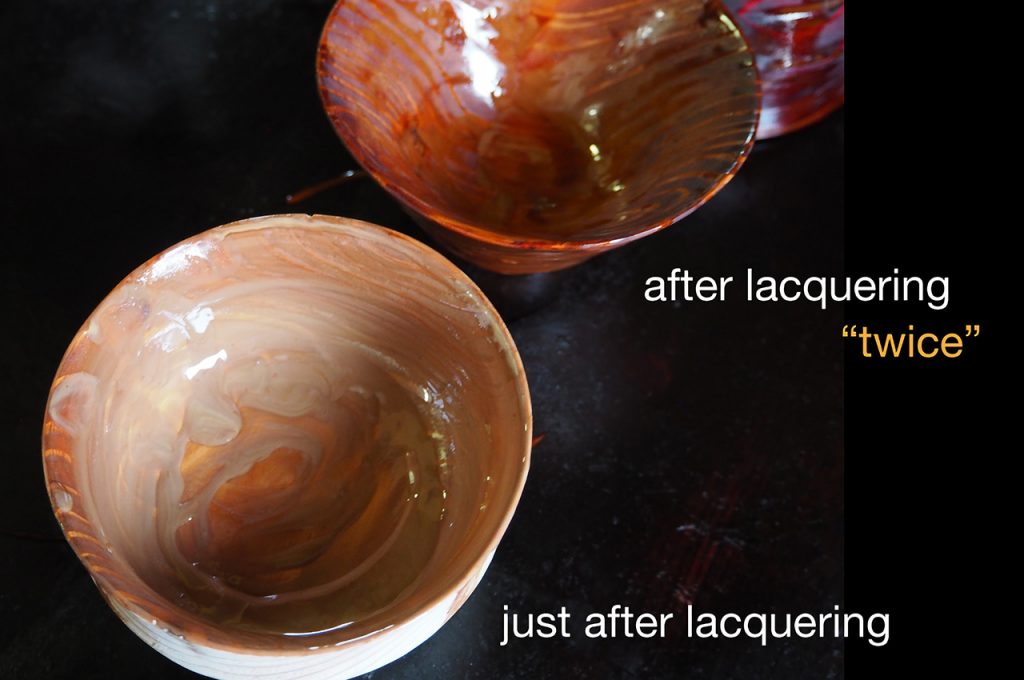
Higashi Shunkei Lacquer Ware
The bowls boast a stunning dark finish with light-colored bands, reminiscent of a tiger’s striped skin. This impressive color is a secret guarded by lacquer artisans who each have their own unique formulas for the clear lacquer. Therefore, the color tone varies in subtle ways depending on the lacquering master, and no two bowls have the same pattern. The very name of the craft is said to come from the fact that the articles produced initially had a similar coloring to Hishunkei tea containers.
The bowls are easy to stack and store, and come in two shapes – one for rice, and another for soups, broths, and ramens.
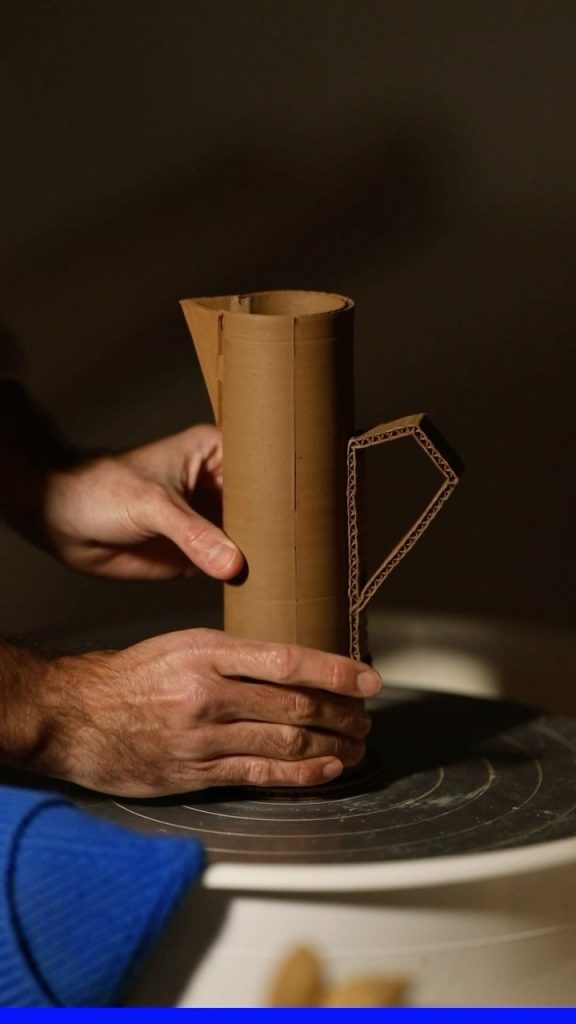
“Cardboard” ceramics by Jacques Monneraud (also header image)
The collection of ceramic objects created by French designer Jacques Monneraud looks as if they’d soak right through if filled with water. He creates ceramic pieces that look as if they were made of pieces of cardboard, taped together.
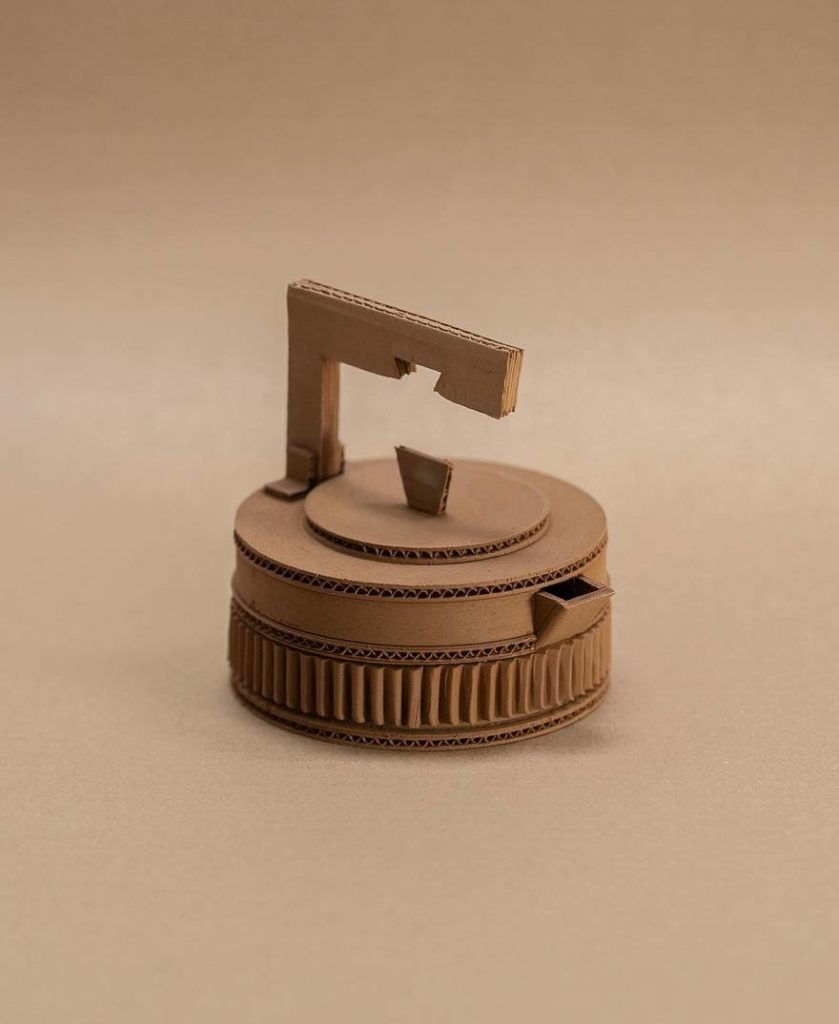
“Cardboard” ceramics by Jacques Monneraud
Prior to the pandemic, Monneraud had a long career as a creative director in an advertising company in Paris. However, in 2021 he quit his job to pursue pottery full-time and completed a ceramics degree.
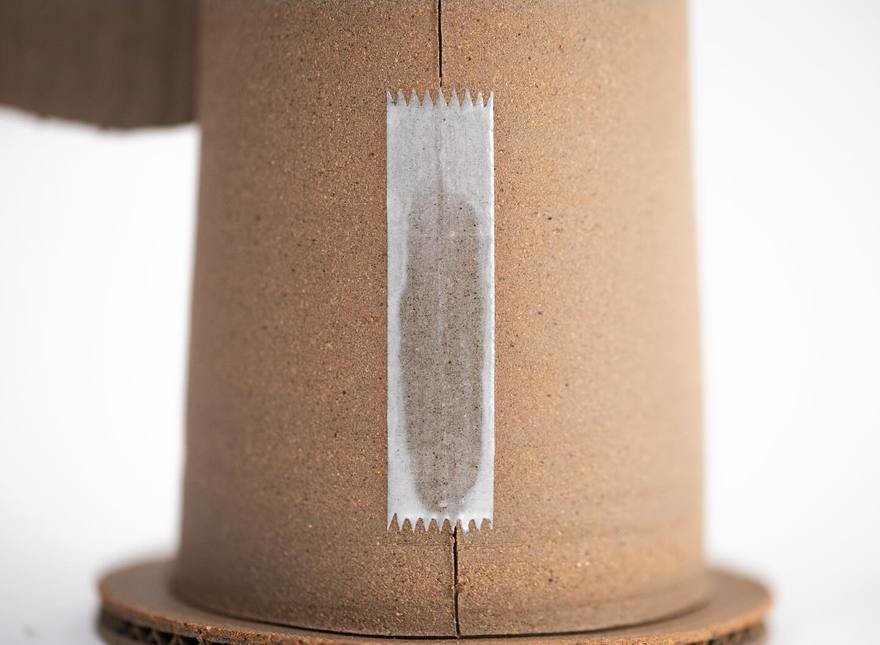
“Cardboard” ceramics by Jacques Monneraud
The most challenging part of his work is to recreate the raw appearance of cardboard. After a series of research and testing of different types of clay and a variety of consistencies, he landed on a mix that evoked the texture. The precise application of thin glaze on the unglazed pieces is utilized to emulate a delicately-applied piece of clear tape. The designer admits that corrugation is especially painstaking to craft.
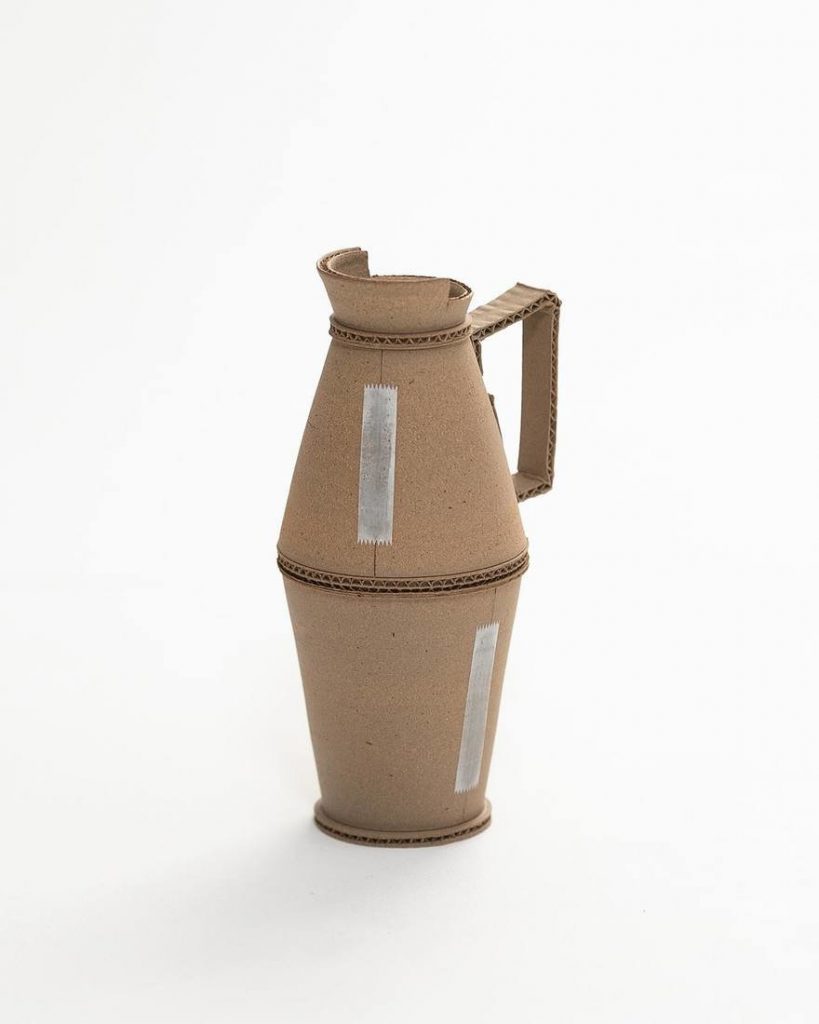
“Cardboard” ceramics by Jacques Monneraud
According to Monneraud, the project is a mockery of our world of overproduction and overconsumption, for this “cardboard” is not meant for throwing away but rather could last 3000 years.